By imitating the surface characteristics of wear-resistant organisms, the bionic non smooth surface morphologies of point, strip and mesh are abstracted. Different bionic non smooth surface morphologies were prepared on the surface of gray cast iron by laser surface treatment, and the influence of different coupling element characteristics on the fatigue wear resistance of gray cast iron was revealed:
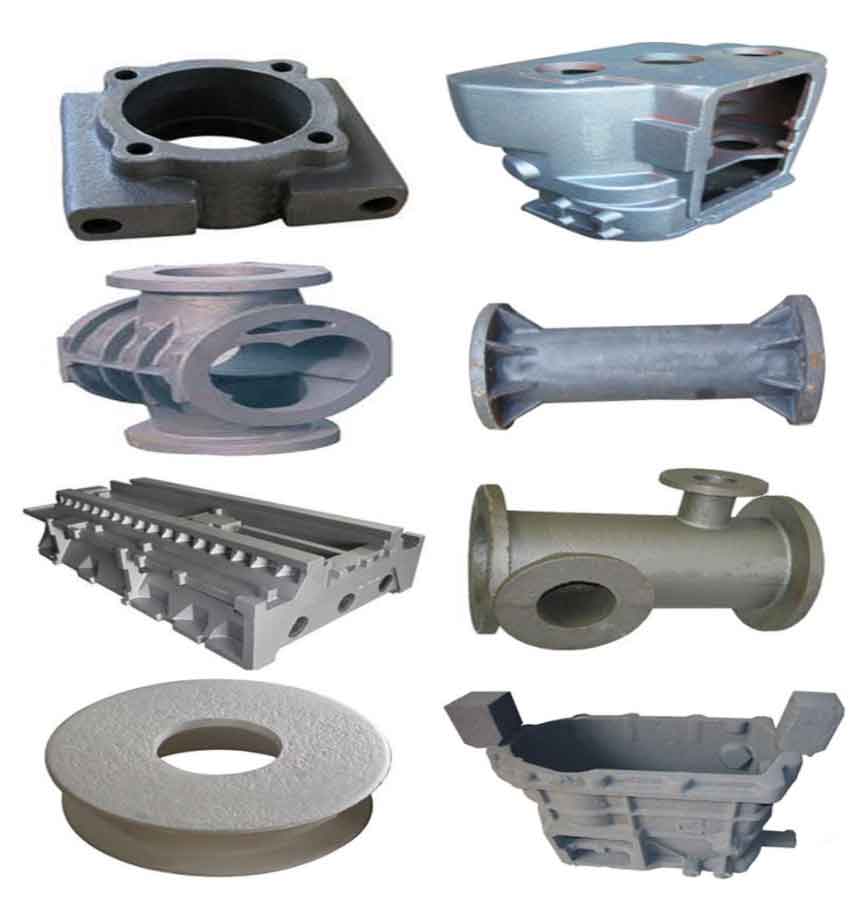
- The bionic coupling sample with mesh unit has the best fatigue wear resistance, and its wear weight loss reduction rate is as high as 53%, followed by the bionic coupling sample with strip unit, and its wear weight loss reduction rate is as high as 29%, while the bionic coupling sample with dot unit is the worst, and the wear weight loss reduction rate is only 23%.
- For the bionic coupling specimen with strip unit, the effect of different unit orientation on its fatigue wear resistance is different. When the element is at 60 ° to the rolling direction, the maximum shear stress plane is dispersed to different planes, so it has the best fatigue wear resistance, and the reduction rate of wear weight loss is 43.5%; When the direction of the element is parallel to the rolling direction, the maximum shear stress plane exists in one plane, and the fatigue defects of gray cast iron are easy to occur, and the loss of wear weight is reduced by 29%; When the direction of the unit body is perpendicular to the rolling direction, the maximum shear stress plane is dispersed, but the roller acts directly on the substrate within a certain time, so it has the worst fatigue wear resistance, and the reduction rate of wear weight loss is only 17.6%.
- The effect of unit arrangement density on fatigue wear resistance of gray cast iron is nonlinear. When the distance between the elements is greater than 2mm, the surface strengthening area leads to the improvement of the fatigue wear resistance of gray cast iron, and the fatigue wear resistance of the bionic coupling specimen increases with the decrease of the distance; When the spacing between elements is less than 2mm, the inconsistent deformation seriously restricts the improvement of fatigue wear resistance of gray cast iron, making fatigue defects more likely to appear in the joint area between elements and matrix. The fatigue wear resistance of gray cast iron decreases with the decrease of spacing. In practical application, the optimum spacing of element bodies should be determined according to the actual load.
- By means of laser carburizing, the lack of carbon atoms in local areas during laser treatment can significantly increase the content of carbides in carburized unit, up to 60-70%. In addition, different processing conditions have different effects on the improvement of fatigue wear resistance of gray cast iron: (a) the cross-sectional area of carburized unit is proportional to the laser energy density, the grain size decreases with the increase of laser energy density, and the content, density and strength of carbides in the unit increase with the increase of processing energy density, Thus, it shows a higher degree of strengthening in the unit area and the improvement of fatigue wear resistance. (b) The thickness of carbon coating has no obvious effect on the size of carburized unit, but seriously affects the microstructure of carburized unit: the grain refinement and carbide content in the unit increase with the decrease of carbon layer thickness, and the contents of martensite, austenite and ledeburite in the carburized unit increase significantly. When the thickness of the carbon layer reaches a critical value of 0.3mm, the structure of the transition zone of the unit body is completely transformed into sorbite. The fatigue wear resistance of the bionic coupling samples prepared under different carbon layer thickness increases with the decrease of carbon layer thickness.
- Using laser alloying method, W and Cr alloy elements were added to prepare biomimetic unit. The existence of W element can form Fe-W carbides to strengthen the grain boundary, while the existence of Cr element can precipitate a large amount of crxcy on the crystal, and form Fe Cr carbides at the grain boundary to strengthen the grain boundary and crystal particles at the same time. With the existence of cr+w element, w element can further strengthen the grain boundary on the Cr Element strengthening mechanism, and can slightly increase the solubility of Cr element in the unit body. Under the joint influence of solid solution strengthening, dispersion strengthening, fine grain strengthening mechanism and the simultaneous strengthening of crystal particles and grain boundaries, compared with the bionic coupling samples prepared by adding a single alloy element, the bionic coupling samples prepared by adding mixed alloy elements show better fatigue wear resistance of gray cast iron.
- With the increase of carbide content, grain boundary and grain strength in the unit body, the resistance to crack propagation in the unit body is significantly enhanced, which separates the connection of fatigue cracks in different matrix areas and reduces the size of fatigue defects on the surface of gray cast iron. In addition, the existence of the element body can effectively share the surface contact stress and reduce the contact stress in the matrix area. The degree of reduction increases with the strengthening degree of the element body.
- Due to the influence of impurities, foreign matters and the fragile area of gray cast iron, the sample has a large wear weight loss at the initial stage of wear; With the increase of the number of cycles, the surface work hardening and friction coefficient of the sample decrease, and the weight loss of the wear obviously decreases and remains stable, entering a stable wear period. The wear rate of gray cast iron in stable period can be used as the evaluation standard of fatigue wear resistance of gray cast iron.
- There are three ways for the formation of fatigue defects in gray cast iron: first, the metal particles in the area surrounded by annular or sub annular fatigue cracks fall off to form surface delamination and spalling, which are generally attached to both sides of the crack or graphite and the graphite tip; Secondly, due to the influence of adhesive wear, a large number of pits appear on the surface of the sample and gather to form pitting; Thirdly, high stress is generated in the local area, and the metal particles are crushed, resulting in the removal of metal particles on the surface.