Pump valve is a kind of equipment basic component with large quantity, wide range and various varieties, which is widely used in all walks of life. It is an important industry in China’s machinery industry, with an annual growth rate of about 30% in recent years. Castings account for a large proportion in pump valve products, and the weight ratio can reach 60% – 80%. The quality of pump valve casting directly affects the performance, efficiency and quality of pump valve products. The pump valve casting has the characteristics of thin wall, complex shape, multi group of clay core forming, etc., and the requirements of casting size accuracy, surface roughness, internal structure density and other aspects are high [3]. With the increase of domestic labor cost and the improvement of national requirements for energy conservation and environmental protection, the traditional casting production mode has become a bottleneck restricting the further development of pump and valve industry and the upgrading of industrial clusters. The development of advanced molding technology and mechanized production line for pump valve castings has become one of the keys to improve the quality and manufacturing level of pump valve castings, the quality of pump valve products and the development of the national pump valve industry. The technology of iron mold sand covering casting is a new technology which is mainly popularized by the state. It is suitable for mass production of castings. It has been well applied in the production of automobile parts castings. A mature production technology of iron mold sand covering casting has been formed, and mechanized and automatic production line of iron mold sand covering casting is used to organize production. The research and development of the foundry technology and production line of sand-coated iron mold for pump and valve castings will help to improve the quality and production efficiency of pump and valve castings, improve the foundry production conditions of pump and valve castings, save energy and reduce emissions, and raise the production level of domestic pump and valve castings to a higher level, so as to promote the comprehensive competitiveness of pump and valve products in China.
Pump valve castings mainly include: pump body, front and rear water outlet section, bracket, valve body, blade, etc. as shown in Fig. 1. The main features of castings are thin wall, light weight, complex shape, high dimensional accuracy requirements, and smooth surface requirements. Generally, the material of castings is gray cast iron with HT200 brand or above. The weight of the casting is 5-15 kg.
1. Characteristics of pump valve casting
(1) The casting is thin-walled and light in weight, and the solidification cooling speed of the casting is relatively fast.
(2) The shape and inner cavity of the casting are relatively complex, so it is difficult to mold many parts, so it is necessary to use curved surface mold or place clay core to form a complete mold.
(3) Because part of the internal part of the mold adopts the way of internal and external clay core forming, so there are two ways of heat transfer in the whole mold: iron mold sand covered casting and sand mold casting.
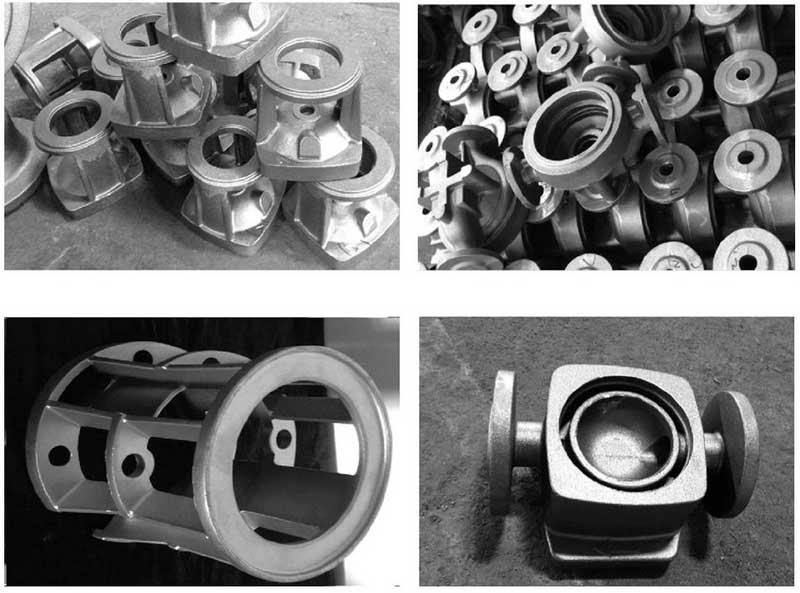
2. Sand coating process of iron mold for pump valve casting
According to the characteristics of sand-covered iron mold casting of pump valve castings and production organization of production line, more than one mold is generally used for sand-covered iron mold casting of pump valve castings, such as two pieces of one mold, four pieces of one mold, six pieces of one mold, etc. The shape and structure of the pump valve casting is complex. In the process of sand covered casting, horizontal or curved parting is adopted, and the parting surface is the iron plane.
The pump valve castings with thin wall and large specific surface area are easy to produce defects of cold separation and insufficient pouring in the production process of iron mold sand covering casting. Therefore, unlike the semi closed pouring system adopted by the general automobile castings, in order to ensure a certain filling pressure and speed in the pouring process, the pump valve castings adopt the closed pouring system in the iron mold sand covering casting process, The area ratio of the pouring system is: F direct: F transverse: f internal = 1.3:1.2:1. In particular, in the design of the gating system, it is necessary to ensure that the molten iron has a certain static head. Generally, side pouring is adopted. Each casting adopts multiple internal sprues. The position of the internal sprue is generally on the flange edge of the casting or the position where the casting can be solidified at the same time, as shown in Figure 2.
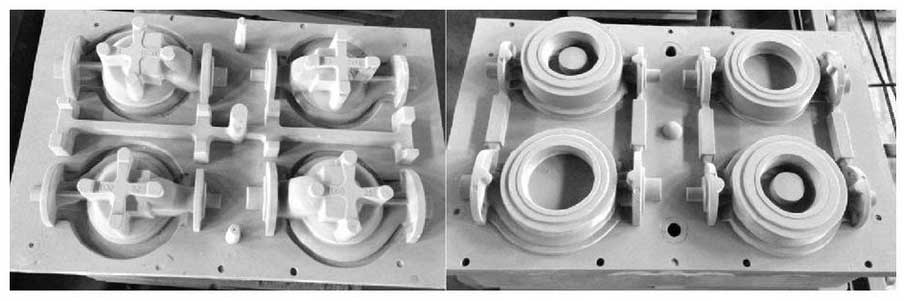
The thickness of sand coating layer and iron mold is one of the important technological parameters in the process of iron mold sand covering casting. Combined with the solidification and cooling characteristics of gray cast iron and the melting treatment process of molten iron, the sand coating thickness of pump valve casting is designed as 6-8mm, and the sand coating thickness of pouring system is 10-15mm, as shown in Figure 3. The thickness of the iron mold varies from 15 mm to 20 mm according to the solidification cooling requirements of the casting. Under these conditions, the temperature range of the mold after pouring may not reach 180 ~ 250 ℃.
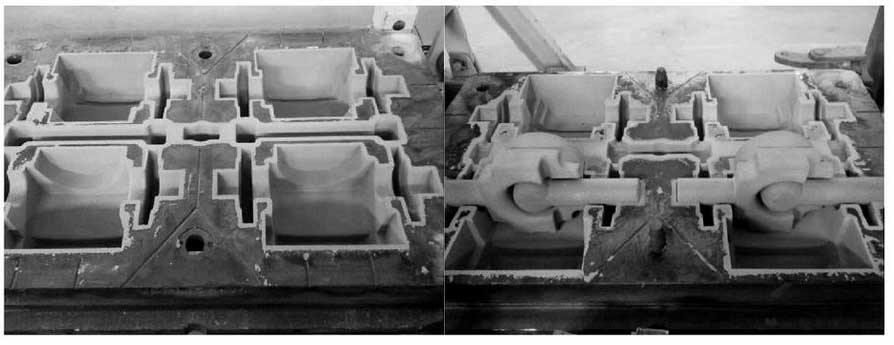