From sand to solid, resin sand casting is a fascinating metal casting technique that transforms ordinary sand into intricate and robust metal components. Let’s delve into the step-by-step process of resin sand casting to gain a deeper understanding of this remarkable technique:
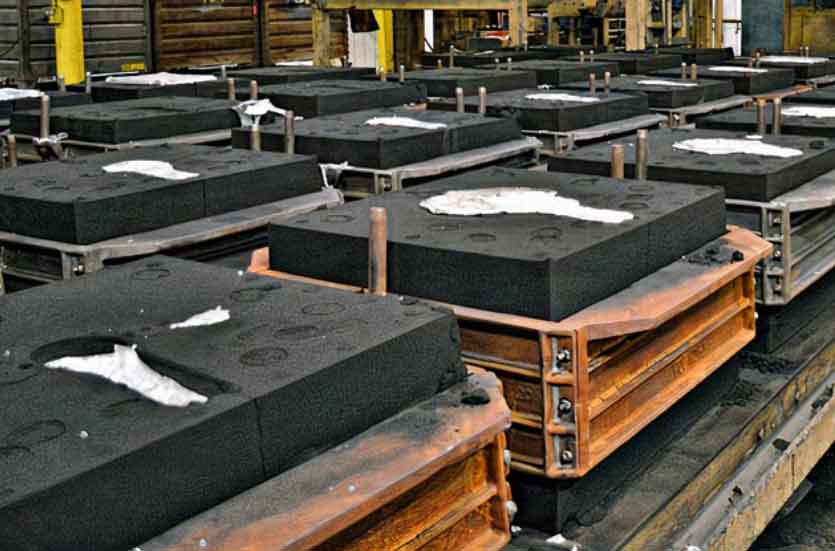
1. Pattern Making:
The journey begins with the creation of a pattern, which is a replica of the final metal component. Skilled pattern makers or engineers craft patterns using materials like wood, plastic, or metal. The pattern must accurately represent the desired shape, size, and features of the casting.
2. Mold Preparation:
In resin sand casting, a two-part mold is used, comprising the “drag” (lower part) and the “cope” (upper part). The pattern is placed inside the drag, and a specially formulated sand, coated with a resin binder, is carefully packed around it. The resin binder provides the sand with the necessary strength and cohesion to withstand the molten metal.
3. Resin Coating:
To create a strong and stable mold, the sand grains are coated with a resin binder. The type of resin used can vary depending on the specific requirements of the casting. Common resins include phenolic urethane or furan resin. The coated sand is applied in layers and compacted to achieve the desired density.
4. Curing:
After the mold is fully packed and compacted, it undergoes a curing process. Curing involves allowing the resin to harden and bond with the sand particles, forming a robust and stable mold. This step is crucial as it ensures the mold retains its shape during the subsequent metal pouring and solidification stages.
5. Mold Assembly:
With the drag fully cured, the cope is placed on top, and the two halves are securely fastened together. The combination of the drag and cope creates a cavity that matches the shape of the desired metal component.
6. Pouring:
The next exciting phase is the pouring of molten metal into the prepared mold. The molten metal, typically aluminum, iron, or steel, is carefully introduced into the mold through a gating system. The gating system controls the flow of the metal and helps minimize potential defects in the casting.
7. Cooling and Solidification:
As the molten metal fills the mold, it starts to cool and solidify into the shape of the pattern and the mold cavity. The cooling time is carefully managed to ensure uniform solidification without the formation of defects such as shrinkage or porosity.
8. Mold Removal and Finishing: Once the metal has completely solidified, the mold is opened, and the casting is carefully removed. The casting may require additional finishing processes, such as removing excess material, grinding, machining, or surface treatments, to achieve the final desired specifications.
9. Inspection and Quality Control:
Before the casting is deemed ready for use, it undergoes thorough inspection and quality control measures. This ensures that it meets the required dimensional accuracy, surface finish, and mechanical properties as per the design specifications.
Resin sand casting is a versatile and precise metal casting technique that combines skilled craftsmanship, innovative materials, and engineering to create a wide range of metal components for various industries. Its ability to produce complex and high-quality castings has made it a popular and reliable choice in modern manufacturing.