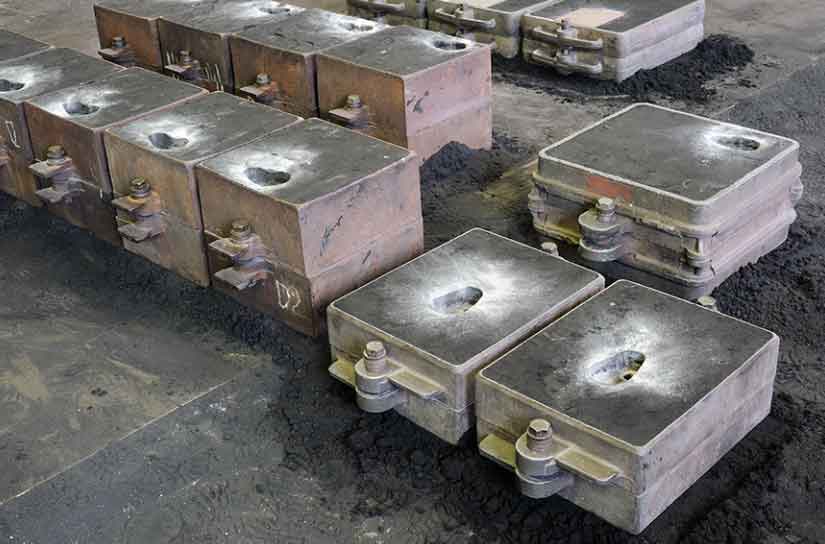
Resin sand casting, also known as resin-bonded sand casting or no-bake sand casting, is a metal casting process that uses a mixture of high-quality sand and synthetic resins as the molding material. It is widely used in the manufacturing industry to produce complex metal components with excellent dimensional accuracy and smooth surface finishes. Here’s a step-by-step overview of the resin sand casting technique:
- Pattern Creation: The first step in resin sand casting is creating a pattern that represents the final shape and dimensions of the desired metal component. Patterns can be made from various materials, such as wood, plastic, or metal, and they are used to create the mold cavity.
- Mold Preparation: A box, called a flask, is placed around the pattern to form a mold cavity. The flask is typically made of metal or wood and has two halves: the cope and the drag. The cope is the top half, and the drag is the bottom half of the mold.
- Sand Mixing: High-quality sand is mixed with a precise amount of synthetic resin binder. The resin is typically a two-part chemical compound that is mixed thoroughly with the sand to form a homogeneous mixture.
- Molding: The sand-resin mixture is carefully and evenly packed around the pattern in the drag half of the flask. The cope is then placed over the drag, and the sand is packed around the cope pattern as well. The sand is compacted to ensure a dense mold.
- Pattern Removal: Once the sand has been packed around the pattern, the pattern is removed, leaving behind a cavity in the sand corresponding to the shape of the pattern. The pattern can be reused to create multiple molds.
- Core Placement (Optional): For castings with internal cavities, cores made of sand and resin can be inserted into the mold to form the internal features of the component.
- Closing the Mold: The cope and drag halves are assembled and securely clamped together to close the mold, which is now ready for metal pouring.
- Metal Pouring: Molten metal, such as iron, steel, aluminum, or bronze, is poured into the mold cavity through a gating system, which ensures proper flow and minimizes the formation of defects.
- Solidification and Cooling: The molten metal cools and solidifies within the mold cavity, taking the shape of the pattern and core (if used).
- Mold Breakout: After the metal has solidified, the mold is opened, and the casting is removed. Any excess sand is removed, and the casting is cleaned and finished as needed.
- Finishing Operations: Depending on the application and requirements, additional finishing operations, such as grinding, machining, and surface treatments, may be performed to achieve the desired final product.
Resin sand casting offers numerous advantages, including excellent dimensional accuracy, smooth surface finish, and the ability to create complex geometries, making it a versatile and widely used process in various industries.