Gate valves are commonly used in various industries to control the flow of fluids. The manufacturing processes for gate valve bodies play a crucial role in ensuring their precision and quality. Here are some techniques typically employed for manufacturing gate valve bodies:
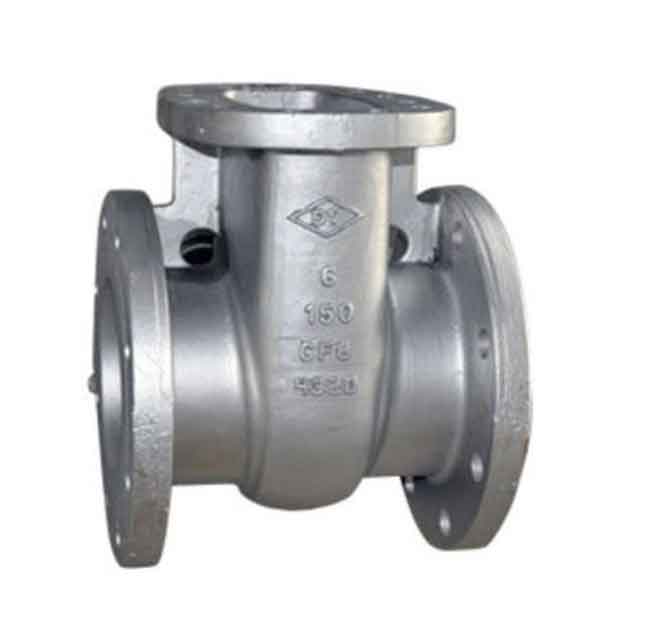
- Casting: Casting is a widely used process for manufacturing gate valve bodies. It involves pouring molten metal, such as cast iron, stainless steel, or bronze, into a mold. The mold is usually made from sand, ceramic, or investment casting materials. Casting allows for complex shapes and can produce gate valve bodies with good dimensional accuracy.
- Machining: Machining processes are employed to achieve precise dimensions, smooth surfaces, and tight tolerances. After casting, the gate valve body undergoes various machining operations, such as milling, drilling, turning, and grinding. CNC (Computer Numerical Control) machines are commonly used for accurate and automated machining processes.
- Forging: Forging is another method used for manufacturing gate valve bodies, especially for high-pressure applications. In this process, a solid piece of metal is heated and shaped using mechanical force, often with the aid of dies and hammers. Forged gate valve bodies offer improved strength, durability, and resistance to fatigue compared to cast counterparts.
- Welding: Welding is utilized to join different components of a gate valve body together. It ensures the structural integrity and leak-tightness of the assembly. Common welding techniques include TIG (Tungsten Inert Gas), MIG (Metal Inert Gas), and stick welding, depending on the materials used.
- Heat Treatment: Heat treatment processes, such as annealing, quenching, and tempering, are employed to enhance the mechanical properties of gate valve bodies. Heat treatment can improve hardness, strength, and resistance to wear and corrosion, resulting in higher quality and durability.
- Quality Control: Throughout the manufacturing process, rigorous quality control measures are implemented to ensure precision and quality. This includes dimensional inspection, non-destructive testing (such as ultrasonic or X-ray testing), pressure testing, and visual inspection. These tests verify the integrity, accuracy, and performance of the gate valve bodies before they are released for use.
It’s worth noting that specific manufacturing techniques may vary depending on factors such as the material used, the size of the gate valve, and the industry requirements. Manufacturers often adhere to industry standards, such as API (American Petroleum Institute) or ASME (American Society of Mechanical Engineers), to ensure the precision, quality, and reliability of gate valve bodies.