Because the motor shell is cylindrical structure, the bottom pouring system is more suitable for the flat pouring because of the gate location. For the same casting, the cross-section size of the inner gate basically has no room for change. Even if it floats in a large range (even several times), it can still get the ideal casting. Therefore, for the internal gate, the selection of location is far more important than the selection of section. Because the shell is cylindrical in shape, no matter how it rotates, there is no flat surface towards the bottom of the sand box, so it is obvious that only one internal gate can not meet the mold filling requirements. When multiple internal gates are arranged, due to the relationship between the columns and the differences between the lengths of multiple internal gates, the liquid metal is The flow rate in the cavity is different. The flow rate of each gate is different, which makes the filling of metal liquid disorder, and the direction of the decomposition of products is out of order. When the flat pouring method is adopted, the schematic diagram of the bottom pouring system is as shown in the figure.
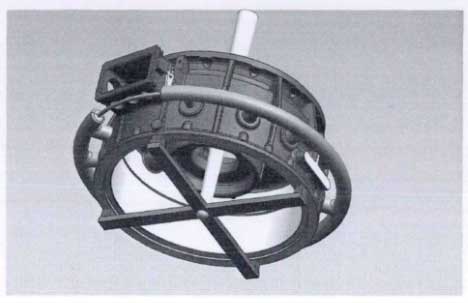
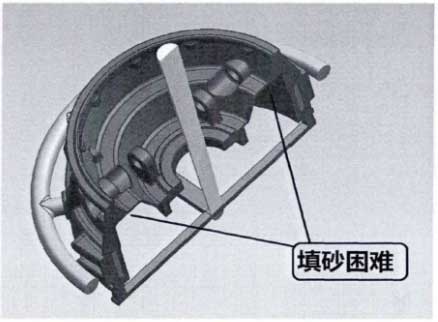
In the above figure, the white cylinder in the middle is the sprue, the purple part is the transverse sprue, and the red part is the internal sprue. As a whole, the pouring method is rain pouring. After buffering, the metal liquid from the direct sprue enters the internal sprue from the transverse sprue, and then starts to evenly fill the EPS pattern from the bottom to the top. The feeding riser of this casting method is also very convenient. It can be arranged on the upper end of the motor shell, and the upper end is the processing surface, which contains the 4mm machining allowance. After the machine is processed, the defects of the riser will be milled out and the qualified products can be obtained. However, the problem of the gating system is that the foam pattern and the water jacket core and the gating system can not be assembled to the motor housing. The sand inside the stator mounting block (as shown), even if there is a vibrating machine, it is very difficult to fill it with dry sand. The EPS foam wrapped without dry sand is bound to be poured through the gravity of the molten metal, and eventually the sarcomas are formed on the casting surface.
It can be seen that flat casting is not suitable for castings. The vertical pouring scheme can solve the above problems. After the pattern is erected, the dry sand can be easily filled from the two ends of the shell. The vertical pouring method also saves the space of the sand box. In a limited volume, more castings can be poured at one time. Through the analysis of the outer shape of the motor shell, it can be found that there is a outlet box on its outer surface, which is used for the internal and external circuit wiring after the motor shell is installed. The end face needs to be processed, including the processing amount. This position is in the vertical pouring mode. If this face is upward, the processing end face of the outlet box will be at the highest position of the whole casting, which is the last solidified part of the casting. If the riser is placed in the Here, whether in the pouring process or in the later machining process, it is very helpful to improve the product quality. In lost foam casting, riser not only plays a role of feeding, but also improves the temperature of the final filling liquid metal and the effect of exhaust and slag collection, so as to avoid the defects such as porosity, slag inclusion and slag like cold shut on the surface of the casting.