Gravity casting and semi-continuous casting are two different techniques used in the metal casting process. Let’s compare them based on various factors:
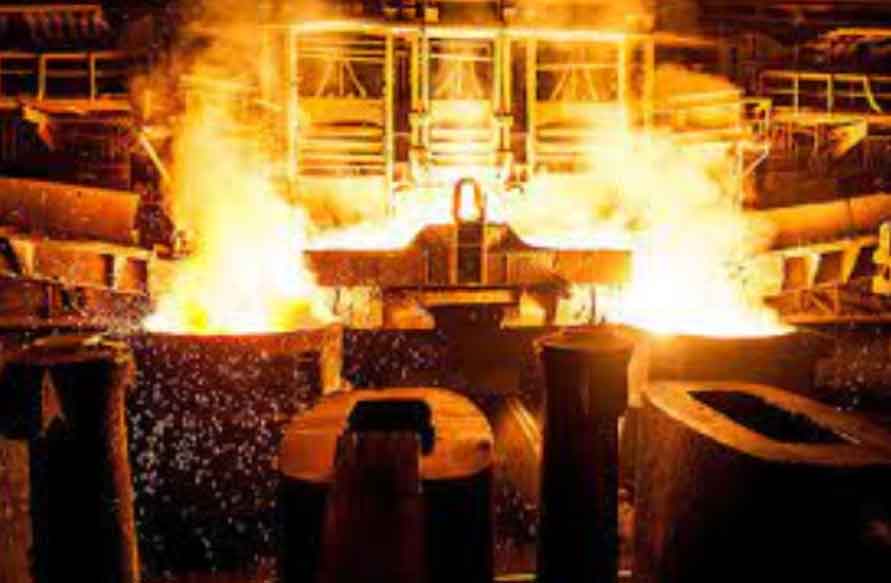
- Casting Process:
- Gravity Casting: Gravity casting, also known as permanent mold casting, relies on gravity to fill the mold cavity with molten metal. The molten metal is poured into a reusable mold made of materials such as steel or cast iron.
- Semi-Continuous Casting: Semi-continuous casting involves the continuous pouring of molten metal into a water-cooled mold. The mold is typically made of copper and has a specific shape to produce continuous castings.
- Casting Flexibility:
- Gravity Casting: Gravity casting is suitable for producing a wide range of shapes and sizes, including complex geometries. The use of reusable molds allows for good detail reproduction and surface finish.
- Semi-Continuous Casting: Semi-continuous casting is commonly used for producing long, continuous sections of metal, such as billets, slabs, or bars. It is less suitable for producing complex-shaped castings.
- Production Rate:
- Gravity Casting: The production rate in gravity casting is generally slower compared to semi-continuous casting. Each casting requires the molten metal to solidify completely before the mold can be reused for the next casting.
- Semi-Continuous Casting: Semi-continuous casting is a high-production-rate technique. It allows for the continuous production of metal sections, enabling a faster and more efficient casting process.
- Equipment and Setup:
- Gravity Casting: Gravity casting requires molds made of durable materials like steel or cast iron, which can withstand repeated use. The setup includes pouring mechanisms, gating systems, and cooling arrangements.
- Semi-Continuous Casting: Semi-continuous casting utilizes a simpler setup consisting of a water-cooled mold, tundish, and continuous casting machine. It can be integrated into existing production lines more easily.
- Cost:
- Gravity Casting: Gravity casting can have lower equipment costs compared to semi-continuous casting, as it doesn’t require complex continuous casting machines. However, the cost of creating and maintaining reusable molds should be considered.
- Semi-Continuous Casting: Semi-continuous casting may have higher equipment costs due to the need for continuous casting machines and water-cooled molds. However, it can be more cost-effective for large-scale production of standardized metal sections.
- Material Selection:
- Gravity Casting: Gravity casting is suitable for various metals and alloys, including aluminum, zinc, copper, and certain types of steels. The choice of material depends on factors such as melting temperature, fluidity, and mold compatibility.
- Semi-Continuous Casting: Semi-continuous casting is commonly used for metals like steel, aluminum, and copper alloys, particularly for large-scale production of standard shapes.
In summary, gravity casting and semi-continuous casting have different applications and advantages:
- Gravity casting is suitable for producing a wide range of shapes and sizes, including complex geometries, but has a slower production rate.
- Semi-continuous casting is ideal for continuous production of long sections, with a faster production rate, but is less suitable for complex-shaped castings.