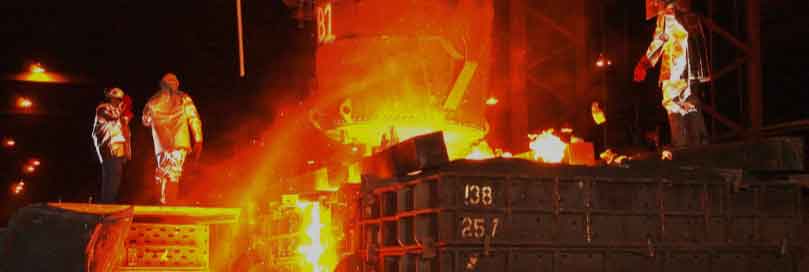
Sand casting is a widely used casting process that involves creating a mold from sand and pouring molten metal into it to produce solid metal parts. This versatile and cost-effective technique has been employed for centuries and remains a fundamental method in the foundry industry. Let’s explore the basics of sand casting, from sand molds to solid metal parts.
Sand Casting Process Overview
The sand casting process can be divided into the following key steps:
- Pattern Creation: The process begins with the creation of a pattern, typically made from wood, plastic, or metal. The pattern replicates the shape and features of the desired final part.
- Mold Preparation: A two-part mold, known as a flask, is made from a special sand mixture. The pattern is placed in one half of the flask, and the sand is packed tightly around it to form the impression or mold cavity. The other half of the flask is then placed on top, creating a complete mold.
- Pattern Removal: The flask is separated, and the pattern is removed from the sand mold, leaving behind a cavity in the shape of the desired part. To facilitate pattern removal, draft angles are incorporated into the pattern design.
- Mold Assembly: The two halves of the mold are reassembled, ensuring proper alignment, and creating a closed mold ready for casting.
- Metal Pouring: Molten metal, such as aluminum, iron, brass, or bronze, is poured into the mold cavity through channels called gates and risers. The metal flows into the mold, replacing the void left by the pattern.
- Cooling and Solidification: The filled mold is left undisturbed to allow the molten metal to cool and solidify within the mold cavity. The solidification process may be accelerated by the use of cooling techniques or the addition of chills, which are pre-cooled metal inserts.
- Mold Breakout: Once the metal has solidified, the mold is broken apart, and the solid metal part, known as the casting, is removed. The mold materials, including the sand, are often recycled for future use.
- Finishing: The casting may undergo various finishing operations to remove excess material, smooth rough surfaces, and achieve the desired final shape. Finishing processes may include grinding, machining, heat treatment, and surface treatments like painting or plating.
- Inspection and Quality Control: The casting is inspected to ensure it meets the desired specifications and quality standards. Non-destructive testing methods, such as visual inspection, X-ray, or ultrasonic testing, may be employed to identify any defects or imperfections.
Advantages and Considerations of Sand Casting
Sand casting offers several advantages and considerations:
Advantages:
- Versatility: Sand casting can produce parts of various sizes, complexities, and shapes, including those with intricate details, undercuts, and internal cavities.
- Cost-Effective: Sand casting is a cost-effective method, as it requires relatively simple equipment and tooling compared to other casting processes. It is well-suited for both small and large production runs.
- Material Versatility: Sand casting can accommodate a wide range of metals and alloys, including ferrous and non-ferrous materials.
- Design Flexibility: Sand casting allows for design flexibility, as patterns can be easily modified or replaced to accommodate design changes or custom requirements.
- Recycling: The sand used in sand casting can be recycled and reused, reducing waste and environmental impact.
Considerations:
- Surface Finish: Sand casting typically results in a rougher surface finish compared to other casting methods, requiring additional finishing operations for smoother surfaces.
- Dimensional Accuracy: Achieving tight dimensional tolerances may be challenging in sand casting, as the sand mold may experience slight shrinkage or distortion during the casting process.
- Production Time: Sand casting may have a longer production time compared to other casting methods due to the mold preparation and cooling time required for solidification.
- Pattern Maintenance: Patterns used in sand casting may experience wear and tear over time and require periodic maintenance or replacement.
Applications of Sand Casting
Sand casting finds applications in various industries, including automotive, aerospace, machinery, marine, and art foundries. It is commonly used to produce components such as engine blocks, cylinder heads, pump housings, gears, brackets, and artistic sculptures.
Conclusion
Sand casting is a foundational casting process that has been used for centuries to produce solid metal parts. By utilizing sand molds and pouring molten metal into them, sand casting offers versatility, cost-effectiveness, and material flexibility. While it may require additional finishing operations and have certain limitations, sand casting remains a crucial method for manufacturing a wide range of metal parts for diverse industries.