Cast iron generally refers to a multi-component iron carbon alloy with a C content of more than 2.0% (wt%, the same below). Generally, the C content of industrial cast iron is 2.5-3.5%. C mostly exists in the form of graphite in gray cast iron, and a small amount exists in the form of Fe3C. In addition to C, grey cast iron also contains 1-3% Si, Mn, P, s and other elements. C. Si, Mn, s and P are the five basic elements in cast iron. In addition, according to the service conditions and required properties of castings, cast iron also contains Ni, Cr, Mo, A1, Cu, Sb, V and other alloy elements.
The content of C in grey cast iron is high, and its matrix structure varies according to the cooling and solidification process. Generally, it can be divided into three categories: ferrite matrix grey cast iron, pearlite ferrite matrix grey cast iron and pearlite matrix grey cast iron.
According to the microstructure analysis of grey cast iron, the difference in classification is actually the content of different forms of C in cast iron. Its main types are compound carbon (Fe3C) and G (graphite). When Fe3C is 8%, it is pearlitic grey cast iron; When Fe3C is less than 0.8%, it belongs to pearlite ferrite grey cast iron; When C exists only in g state, it is a ferritic grey cast iron.
Chapter 1: The Basic Characteristics of Gray Cast Iron Castings
Grey cast iron is a type of cast iron known for its distinctive graphite microstructure, which gives it its name. It is widely used in various industrial applications due to its unique properties and characteristics. Here are the basic characteristics of grey cast iron:
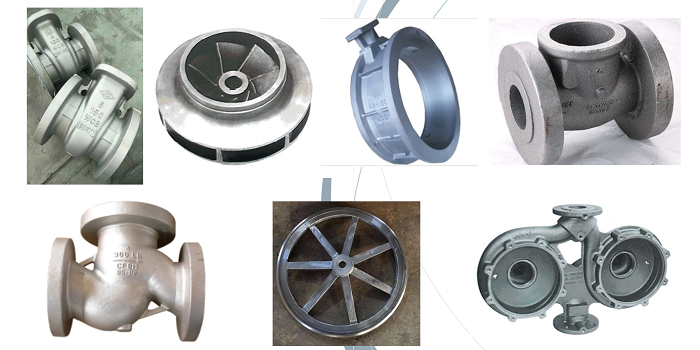
Alloy Composition:
- Grey cast iron is primarily composed of iron and carbon, along with silicon, manganese, sulfur, and phosphorus as impurities and alloying elements.
- The carbon content is relatively high, usually ranging from 2.5% to 4.0%. This high carbon content is responsible for the formation of graphite flakes.
Microstructure:
- The hallmark feature of grey cast iron is its graphite microstructure, which appears in the form of flake-like particles.
- The graphite flakes are embedded within a matrix of ferrite and pearlite phases.
Mechanical Properties:
- Grey cast iron exhibits good compressive strength due to the presence of graphite flakes, which act as stress relievers and prevent crack propagation.
- It has low tensile strength and ductility compared to other cast irons and metals, making it less suitable for applications requiring high impact or tensile loading.
- Grey cast iron has good wear resistance, making it suitable for applications involving sliding or abrasive wear conditions.
- It has good machinability, allowing for easy machining of components.
Effect on Performance and Applications:
- The presence of graphite flakes gives grey cast iron its characteristic gray color and provides lubrication and vibration damping properties, making it suitable for applications involving sliding or reciprocating motion, such as engine cylinder blocks, piston rings, and brake drums.
- The low cost and ease of casting make grey cast iron an attractive choice for various applications where high tensile strength is not a critical requirement.
- The wear resistance and dimensional stability of grey cast iron make it suitable for applications like machine tool beds, gears, and automotive components.
- The brittleness and low impact resistance of grey cast iron limit its use in applications subjected to high impact loads or dynamic stresses.
In summary, the unique microstructure of grey cast iron, characterized by graphite flakes, imparts specific mechanical and physical properties that influence its performance and applications. While its low cost and wear resistance make it suitable for certain applications, its brittleness and limited tensile strength need to be considered when selecting grey cast iron for specific engineering and manufacturing purposes.
Chapter 2: The Main Alloying Elements of Gray Cast Iron Castings
The main alloying elements in grey cast iron are carbon (C), silicon (Si), phosphorus (P), and sulfur (S). These elements play a crucial role in determining the microstructure and properties of grey cast iron. Here’s how each alloying element affects the properties of castings:
- Carbon (C):
- Carbon is the primary alloying element in grey cast iron, typically ranging from 2.5% to 4.0%.
- Carbon influences the formation of graphite flakes within the microstructure. Higher carbon content promotes the formation of larger graphite flakes.
- Graphite flakes provide lubricity and vibration damping properties, enhancing wear resistance and reducing friction between surfaces.
- The presence of graphite also affects the mechanical properties. While it provides good compressive strength and wear resistance, it reduces tensile strength and ductility, making grey cast iron brittle.
- Silicon (Si):
- Silicon is added to grey cast iron primarily to promote the formation of graphite flakes and stabilize the graphite morphology.
- Silicon encourages the formation of a fine and uniform graphite structure, improving the machinability and casting performance.
- It increases fluidity during casting, reducing the risk of shrinkage defects and promoting a sound casting structure.
- Silicon also enhances the resistance of grey cast iron to oxidation and corrosion.
- Phosphorus (P):
- Phosphorus is typically considered an impurity in grey cast iron and is often controlled to low levels (usually below 0.1%).
- Higher levels of phosphorus can lead to the formation of brittle phosphide compounds, reducing the mechanical properties and ductility of the iron.
- Phosphorus can also contribute to the formation of white cast iron, which is harder but more brittle than grey cast iron.
- Sulfur (S):
- Sulfur is another impurity that is usually controlled to low levels in grey cast iron (typically below 0.1%).
- High sulfur content can lead to the formation of sulfide inclusions, which can decrease the mechanical properties and increase brittleness.
- Sulfur can also affect the machinability of castings. A moderate sulfur content can improve machinability, while excessive sulfur can have negative effects.
In summary, the alloying elements carbon, silicon, phosphorus, and sulfur have significant effects on the microstructure, mechanical properties, and performance of grey cast iron. Balancing these elements is important to achieve the desired combination of wear resistance, machinability, casting performance, and mechanical strength for specific applications.
Chapter 3: The Microstructure of Gray Cast Iron Castings
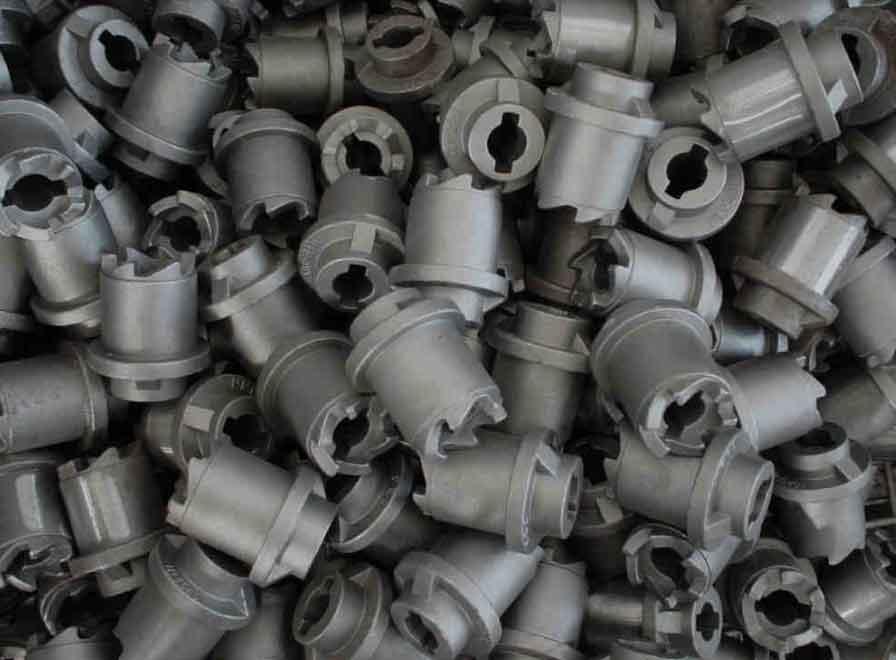
The microstructure of grey cast iron castings is characterized by the presence of graphite flakes within a matrix of ferrite and pearlite. This unique microstructure gives grey cast iron its distinctive properties and affects its performance in various applications. The microstructure can be further categorized into different types based on the distribution and size of graphite flakes:
- Type A (Flake Graphite):
- In this microstructure, graphite flakes are randomly distributed throughout the matrix.
- This type of microstructure is often associated with higher carbon content and slower cooling rates during solidification.
- It provides good wear resistance, thermal conductivity, and damping properties, making it suitable for applications involving sliding or reciprocating motion.
- Type B (Kish Graphite):
- In this microstructure, graphite flakes are concentrated along grain boundaries or certain regions.
- It can result from specific solidification conditions and impurities such as sulfur.
- This type of microstructure may have reduced mechanical properties compared to Type A, but it can still offer good machinability and wear resistance.
- Type C (Compacted Graphite):
- This microstructure is intermediate between flake graphite and nodular graphite (ductile iron).
- It exhibits a combination of flake-like and spheroidal graphite, resulting in improved mechanical properties compared to conventional grey cast iron.
- Compacted graphite iron offers enhanced tensile strength, thermal conductivity, and damping characteristics.
The impact of different microstructural types on the performance of grey cast iron castings includes:
- Wear Resistance: The presence of graphite flakes provides self-lubricating properties and reduces friction, contributing to excellent wear resistance. Type A and Type B microstructures are particularly suited for wear-prone applications.
- Thermal Conductivity: The graphite flakes in the microstructure enhance thermal conductivity, making grey cast iron suitable for applications involving heat transfer, such as engine blocks and cookware.
- Damping Capacity: The graphite flakes also contribute to vibration damping properties, making grey cast iron ideal for components that require noise and vibration reduction.
- Machinability: Grey cast iron with Type A and Type B microstructures is easily machinable due to the presence of graphite, which acts as a chip breaker during machining.
- Tensile Strength and Ductility: The presence of graphite flakes in grey cast iron reduces tensile strength and ductility compared to other materials. While this may limit its use in certain load-bearing applications, it is advantageous for components subjected to compressive loads.
- Impact Resistance: The brittleness associated with graphite flakes can lead to reduced impact resistance. Careful design and consideration of loading conditions are necessary to avoid brittle failure.
In summary, the microstructure of grey cast iron castings, characterized by the distribution and type of graphite flakes within the matrix, significantly influences the material’s properties and performance. The choice of microstructure depends on the specific requirements of the application, balancing factors such as wear resistance, machinability, thermal conductivity, and mechanical strength.
Chapter 4: The Wear Resistance and Corrosion Resistance of Gray Cast Iron Castings
Grey cast iron castings exhibit good wear resistance and moderate corrosion resistance, making them suitable for various applications where these properties are important. Here’s an overview of the wear and corrosion resistance of grey cast iron castings:
Wear Resistance:
- Grey cast iron’s wear resistance is primarily attributed to the presence of graphite flakes in its microstructure.
- The graphite flakes act as solid lubricants, reducing friction and wear between surfaces in sliding or reciprocating motion.
- This self-lubricating property makes grey cast iron suitable for applications involving frictional wear, such as brake components, engine cylinders, piston rings, and gears.
- In abrasive wear conditions, the matrix material surrounding the graphite flakes provides additional resistance.
Corrosion Resistance:
- Grey cast iron has moderate corrosion resistance, but it is not as corrosion-resistant as some other materials like stainless steel or certain non-ferrous alloys.
- The presence of graphite in the microstructure can create microgalvanic cells, leading to localized corrosion in the presence of moisture and corrosive environments.
- Grey cast iron can be susceptible to forms of corrosion such as uniform corrosion, pitting corrosion, and graphitic corrosion (where graphite is selectively corroded).
- Corrosion resistance can be improved by applying protective coatings, such as paints or metal platings, to create a barrier between the casting surface and the corrosive environment.
It’s important to note that the wear and corrosion resistance of grey cast iron can be influenced by factors such as the alloy composition, microstructure, surface finish, operating conditions, and the presence of impurities. For applications where enhanced wear or corrosion resistance is required, surface treatments or coatings can be applied to improve the material’s performance.
When selecting grey cast iron for a specific application, it’s essential to carefully consider the intended operating environment, the type of wear or corrosion expected, and whether additional measures are needed to enhance the material’s resistance to these factors.
Chapter 5: The Application of Grey Cast Iron Castings
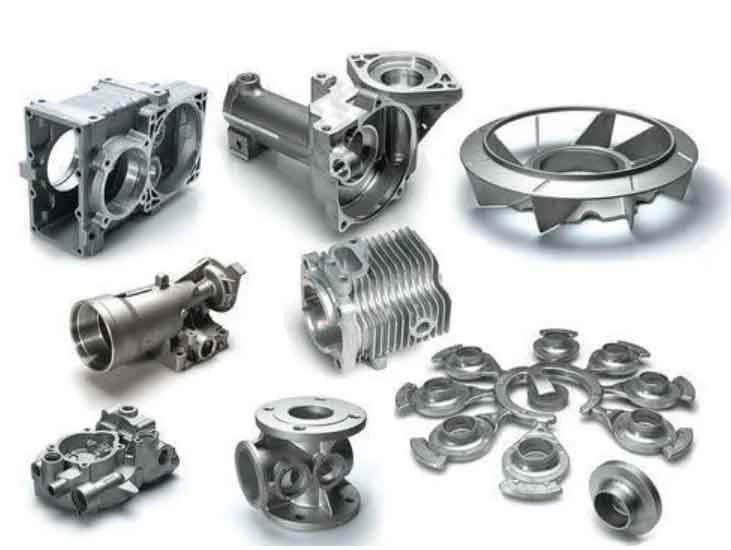
Grey cast iron, known for its unique properties and ease of casting, finds application in various industries due to its excellent machinability, good thermal conductivity, and damping properties. Some common applications of grey cast iron castings include:
- Automotive Industry:
- Engine blocks, cylinder heads, brake components, and suspension parts benefit from grey cast iron’s thermal stability, durability, and noise-damping properties.
- Machinery and Equipment:
- Gearboxes, machine bases, and components requiring vibration dampening and stability are commonly made from grey cast iron.
- Pipes and Fittings:
- Grey cast iron is used in water pipes, drainage systems, and other plumbing applications due to its corrosion resistance and pressure-bearing capabilities.
- Construction:
- Manhole covers, grates, and other construction components require grey cast iron’s strength and durability.
- Agricultural Equipment:
- Tractor parts, plow components, and agricultural machinery often utilize grey cast iron’s wear resistance and toughness.
- Railway Industry:
- Components like brake shoes, rail joints, and couplings benefit from grey cast iron’s friction and heat resistance.
- Energy Generation:
- Wind turbine components, generator casings, and other parts benefit from grey cast iron’s stability and heat resistance.
- Cookware and Appliances:
- Cookware, stoves, and other household appliances use grey cast iron due to its excellent heat retention and even heating properties.
- Valves and Pumps:
- Valves, pumps, and other fluid-handling equipment utilize grey cast iron’s corrosion resistance and durability.
- Heavy Industrial Machinery:
- Rollers, frames, and heavy machinery components are often made from grey cast iron due to its load-bearing capacity.
- Automated Machinery:
- Grey cast iron’s vibration-damping properties are valuable for machinery that requires precision and reduced noise.
- Machine Tools:
- Machine tool structures, such as lathe beds and milling machine bases, often use grey cast iron for stability and precision.
Grey cast iron’s versatility makes it a preferred material for a wide range of applications, particularly when a combination of strength, stability, damping, and ease of casting is required. Advances in metallurgy and casting techniques continue to expand the possibilities for grey cast iron’s applications in modern industries.
Chapter 6: The Heat Treatment Methods of Gray Cast Iron Castings
Heat treatment of grey cast iron involves various processes aimed at altering its microstructure and mechanical properties to meet specific requirements. While grey cast iron is not as amenable to heat treatment as some other materials due to its graphite structure, certain treatments can still be applied:
- Annealing:
- Annealing involves heating the grey cast iron to a specific temperature and holding it there for a certain period before slowly cooling it. This process reduces internal stresses, improves machinability, and refines the graphite structure. Full annealing promotes softness and ease of machining.
- Normalizing:
- Normalizing is a similar process to annealing but involves air cooling instead of slow furnace cooling. It helps achieve a more uniform microstructure and reduce brittleness.
- Stress Relieving:
- Stress relieving involves heating the grey cast iron to a moderate temperature to relieve internal stresses caused by casting or machining. It helps improve dimensional stability and reduce distortion.
- Quenching and Tempering:
- While traditional quenching and tempering processes are not commonly used for grey cast iron due to its graphite content, some specialized types of cast iron can undergo these processes to achieve certain properties.
- Surface Hardening:
- Certain surface hardening techniques, such as flame hardening or induction hardening, can be used to selectively improve wear resistance on specific areas of the grey cast iron component.
- Precipitation Hardening:
- Some alloyed forms of grey cast iron can undergo precipitation hardening, where the alloying elements are in solution and then age to form harder phases.
It’s important to note that the heat treatment of grey cast iron is limited due to its graphite structure, which remains largely unaffected by heat treatment. The primary purpose of heat treatment for grey cast iron is to relieve internal stresses, improve machinability, and enhance certain mechanical properties to a limited extent. The specific heat treatment method chosen will depend on the type of grey cast iron, the desired properties, and the intended application of the component.
Chapter 7: The Advantages and Disadvantages of Grey Iron Castings in Different Applications
Grey iron castings offer a range of advantages and disadvantages that make them suitable for specific applications. Here’s a breakdown of these pros and cons in various application areas:
Advantages of Grey Iron Castings:
- Automotive Industry:
- Advantages: Good damping properties reduce noise and vibration, excellent machinability for precision components like engine blocks, good thermal conductivity for efficient heat dissipation.
- Disadvantages: Lower tensile strength compared to other materials, brittleness.
- Machinery and Equipment:
- Advantages: Excellent wear resistance, good machinability for gears and machine bases, cost-effectiveness.
- Disadvantages: Limited tensile strength, can be brittle under impact loads.
- Pipes and Fittings:
- Advantages: Corrosion resistance, easy machining for threads and connections, relatively low cost.
- Disadvantages: Brittle under impact, limited tensile strength.
- Construction:
- Advantages: High compressive strength, good damping properties, durability for manhole covers and grates.
- Disadvantages: Brittle under impact, limited tensile strength.
- Agricultural Equipment:
- Advantages: Good wear resistance for plow components, cost-effectiveness.
- Disadvantages: Limited tensile strength, brittleness.
- Railway Industry:
- Advantages: Wear resistance for rail joints and couplings, good machinability.
- Disadvantages: Brittle under impact, limited tensile strength.
- Energy Generation:
- Advantages: High thermal conductivity, good wear resistance for wind turbine components.
- Disadvantages: Limited tensile strength, brittleness.
Disadvantages of Grey Iron Castings:
- Limited Tensile Strength: Grey iron castings have lower tensile strength compared to other materials, making them less suitable for applications subjected to high tensile loads.
- Brittleness: Grey iron is relatively brittle, making it susceptible to fracture under impact loads.
- Poor Ductility and Toughness: Grey iron lacks the ductility and toughness required for applications involving severe dynamic loads.
- Weight: Grey iron can be relatively heavy, which might not be desirable in weight-sensitive applications.
- Limited Weldability: Grey iron’s low weldability can restrict its use in applications requiring welding or repair.
- Surface Finish and Machining: While grey iron has good machinability, its graphite structure can affect surface finishes, requiring additional machining or finishing operations.
- Corrosion Resistance: While grey iron is corrosion-resistant to a certain extent, it may not be suitable for highly corrosive environments without protective coatings.
- Size and Complexity Constraints: Grey iron castings might have limitations in terms of size and complexity due to the casting process and brittleness.
Grey iron castings excel in applications where wear resistance, vibration damping, and cost-effectiveness are important. However, their limitations in terms of tensile strength, toughness, and impact resistance must be carefully considered when selecting them for specific applications. Proper design and engineering are crucial to harness the advantages of grey iron while mitigating its disadvantages.
Chapter 8: The Casting Process of Gray Cast Iron
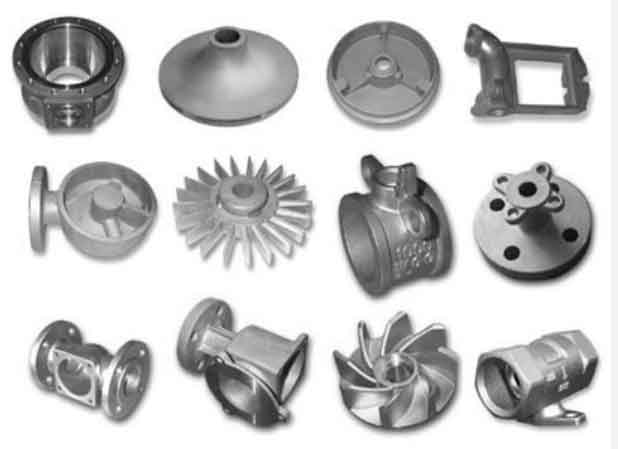
The casting process of gray cast iron involves several key steps that contribute to the overall quality of the castings. Let’s explore each step in detail:
1. Model Preparation:
- Model preparation involves creating a pattern or model of the desired part. This pattern is used to create the mold cavity into which molten metal will be poured. The pattern can be made from various materials, such as wood, plastic, or metal.
- Importance for Quality: The accuracy and quality of the pattern directly influence the final dimensions and shape of the casting. Any defects or inaccuracies in the pattern can lead to corresponding flaws in the cast part.
2. Sand Casting:
- Sand casting is the process of creating a mold cavity by packing sand around the pattern. Once the sand mold is prepared, molten gray cast iron is poured into the mold.
- Importance for Quality: Proper molding techniques, such as compacting the sand evenly and ensuring adequate venting, are essential for achieving uniform casting quality. Inadequate packing or venting can lead to defects like porosity, uneven cooling, or mold erosion.
3. Cold Iron Liquid Treatment:
- Cold iron is a piece of metal inserted into the mold before pouring to aid in solidification and control the cooling rate of the molten metal. It helps promote uniform cooling and minimize the formation of undesirable microstructures.
- Importance for Quality: Cold iron placement and design play a critical role in controlling the solidification process and reducing the likelihood of defects like shrinkage or excessive carbide formation.
4. Pouring and Solidification:
- During pouring, molten gray cast iron is introduced into the mold cavity. As the metal cools, it solidifies and takes on the shape of the mold.
- Importance for Quality: Proper pouring techniques, such as controlling the pouring rate and minimizing turbulence, are crucial to prevent defects like air entrapment, shrinkage, or non-uniform cooling.
5. Cooling and Solidification:
- After pouring, the casting cools and solidifies. The cooling rate affects the microstructure and mechanical properties of the cast iron.
- Importance for Quality: Proper cooling rates and control of cooling gradients are important to achieve the desired microstructure, which impacts the casting’s mechanical properties, including hardness and strength.
6. Quality Control and Inspection:
- Once the casting has solidified and cooled, it is removed from the mold and subjected to quality control and inspection processes. This may involve visual inspection, dimensional measurement, non-destructive testing, and other assessments to ensure the casting meets specified requirements.
- Importance for Quality: Thorough quality control helps identify and rectify defects or deviations from specifications, ensuring that only high-quality castings move forward in the manufacturing process.
Impact on Casting Quality:
The various steps in the gray cast iron casting process collectively influence the quality of the final product. Inadequate pattern design or molding techniques can result in defects like surface imperfections, porosity, or dimensional inaccuracies. Improper pouring and cooling can lead to issues such as uneven microstructure, brittleness, or casting shrinkage. Cold iron placement and treatment contribute to achieving the desired microstructure and mechanical properties.
Overall, meticulous attention to each step in the casting process is essential to produce gray cast iron castings of consistent quality, meeting the intended design and performance requirements.
Chapter 9: The Quality Control Methods for Gray Cast Iron Castings
Quality control is a crucial aspect of gray cast iron casting production to ensure that the final products meet the required specifications and standards. Various methods and techniques are employed to assess different aspects of the castings. Here are some common quality control methods used for gray cast iron castings:
1. Metallographic Analysis: Metallographic analysis involves examining the microstructure of the cast iron under a microscope. It helps determine the grain size, graphite morphology, presence of phases, and overall material quality.
- Purpose: Assessing microstructure for proper graphite distribution, identifying potential defects like carbide formation, and verifying material properties.
2. Dimensional Measurement: Dimensional measurement ensures that the castings’ dimensions, tolerances, and geometric features meet the specified requirements.
- Techniques: Coordinate measuring machines (CMM), calipers, micrometers, laser scanning, optical comparators, etc.
- Purpose: Verifying casting dimensions, hole sizes, angles, and other geometric characteristics.
3. Non-Destructive Testing (NDT): NDT methods detect defects without causing damage to the casting. Common NDT techniques include:
- Visual Inspection: Examination of the casting’s surface for defects like cracks, porosity, and surface finish.
- Radiographic Testing (RT): X-rays or gamma rays are used to detect internal defects like voids, inclusions, and cracks.
- Ultrasonic Testing (UT): Ultrasonic waves are used to detect internal defects and measure wall thickness.
- Magnetic Particle Testing (MT): Magnetic fields and particles are used to detect surface and near-surface defects.
- Dye Penetrant Testing (PT): Dye penetrant is applied to surface defects, and excess dye is removed to reveal defects.
4. Mechanical Testing: Mechanical testing assesses the mechanical properties of the castings, including tensile strength, hardness, impact resistance, and more.
- Techniques: Tensile testing, hardness testing (Brinell, Rockwell), Charpy impact testing, etc.
- Purpose: Evaluating the casting’s ability to withstand mechanical loads and stresses.
5. Chemical Analysis: Chemical analysis determines the composition of the cast iron to ensure it meets the required specifications.
- Techniques: Spectrometry (e.g., optical emission spectroscopy, X-ray fluorescence).
- Purpose: Verifying the presence and proportions of alloying elements and ensuring compliance with material standards.
6. Pressure Testing: Pressure testing involves subjecting the casting to pressurized fluid to detect leaks, cracks, or weak points in the structure.
- Purpose: Ensuring that the casting can withstand pressure and fluid containment.
7. Hardness Profiling: Hardness profiling involves measuring hardness at various points on the casting’s surface to identify potential variations or anomalies.
- Purpose: Detecting localized variations in material properties that could affect performance.
8. Visual and Surface Inspection: Visual and surface inspections are conducted to identify surface defects, such as cracks, porosity, inclusions, and other imperfections.
- Purpose: Ensuring the casting’s surface quality and appearance meet specifications.
Effective quality control involves a combination of these methods at various stages of production to identify and address any defects or deviations from requirements. By implementing comprehensive quality control measures, manufacturers can ensure that their gray cast iron castings meet the highest standards of quality and performance.
Chapter 10: Possible Environmental Impacts During the Casting Process of Gray Cast Iron
The casting process of gray cast iron, like any manufacturing process, can have environmental impacts. These impacts can include energy consumption, greenhouse gas emissions, waste generation, and resource depletion. Implementing measures to improve sustainability can help mitigate these impacts. Here’s how:
1. Energy Consumption:
- Impact: Casting processes require energy for melting, molding, and other operations, contributing to carbon emissions.
- Sustainability Measures:
- Use energy-efficient equipment and technologies.
- Optimize process parameters to minimize energy use.
- Consider renewable energy sources for power generation.
2. Greenhouse Gas Emissions:
- Impact: Energy consumption in casting can lead to greenhouse gas emissions, contributing to climate change.
- Sustainability Measures:
- Implement carbon reduction strategies, such as using cleaner fuels.
- Capture and utilize waste heat from furnaces for other processes.
- Adopt low-carbon or carbon-neutral energy sources.
3. Waste Generation:
- Impact: Casting generates waste materials such as used sand, cores, and excess metal.
- Sustainability Measures:
- Implement waste reduction and recycling programs.
- Reuse sand and materials where possible.
- Explore opportunities for waste-to-energy conversion.
4. Water Usage:
- Impact: Water is used for cooling, cleaning, and other processes, contributing to water consumption and potential pollution.
- Sustainability Measures:
- Implement closed-loop cooling systems to reduce water consumption.
- Treat and recycle water used in the process.
- Minimize the use of water-based cleaning agents.
5. Air Quality:
- Impact: Furnace emissions can contribute to air pollution, releasing particulates and pollutants.
- Sustainability Measures:
- Use pollution control technologies, such as scrubbers, to reduce emissions.
- Optimize combustion processes to minimize emissions.
- Monitor air quality regularly and implement corrective actions.
6. Resource Depletion:
- Impact: Casting requires raw materials, such as iron ore and other alloys, contributing to resource depletion.
- Sustainability Measures:
- Use recycled materials to reduce demand for virgin resources.
- Explore alternative materials with lower environmental impacts.
- Implement efficient material use and minimize waste.
7. Noise and Vibrations:
- Impact: Casting processes can generate noise and vibrations, affecting local communities and ecosystems.
- Sustainability Measures:
- Implement noise reduction measures, such as acoustic enclosures.
- Regularly monitor noise levels and take corrective actions.
8. Ecosystem Impact:
- Impact: Mining for raw materials and waste disposal can impact local ecosystems.
- Sustainability Measures:
- Practice responsible mining and resource extraction.
- Implement land restoration and reclamation plans.
- Minimize waste generation and ensure proper waste disposal.
By adopting sustainable practices and technologies, gray cast iron manufacturers can minimize their environmental footprint and contribute to a more eco-friendly casting process. Implementing these measures not only reduces environmental impacts but can also lead to cost savings, improved reputation, and enhanced regulatory compliance.