The numerical model of axle housing is established by Creo software and saved in. STP format. The STP file is imported by visual mesh module in VE environment of ESI. Then, the imported problem surface is checked, and the software automatically checks whether there is missing surface in 3D model and whether there is out of tolerance gap between faces due to modeling error.
Mesh generation is the key factor to determine the success of numerical simulation. Only correct and reasonable mesh generation can establish effective finite element model. In order to ensure the quality of mesh generation, the volume mesh is divided after the surface mesh is divided correctly.
The economy of mesh generation should be fully considered when meshing. The quantity and quality of meshes determine the accuracy and scale of finite element calculation. Too few meshes will make the calculation accuracy too low to meet the requirements of simulation analysis. However, too much grid number will greatly increase the calculation scale, thus increasing the calculation time cost, which is not conducive to fast calculation and analysis 。
Therefore, different mesh numbers should be used in different parts, and the number of grids must be increased in the stress concentration and hot spot area to reflect the simulation effect more truly. In addition, the thin wall should be locally refined to ensure three or more grids at the minimum wall thickness.
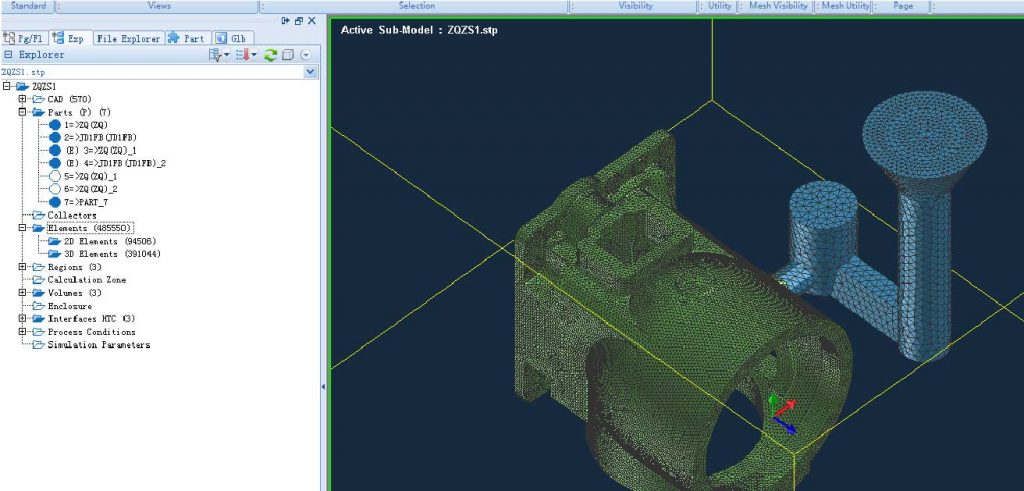
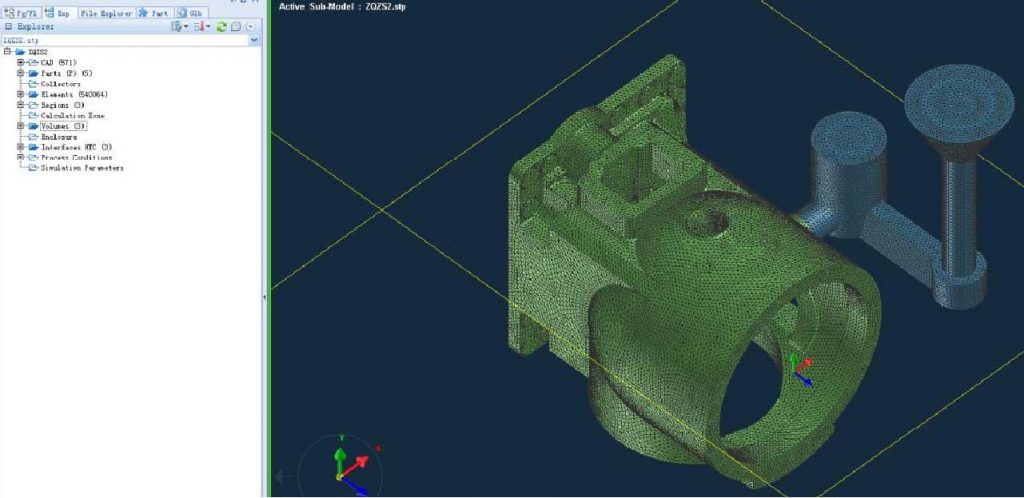
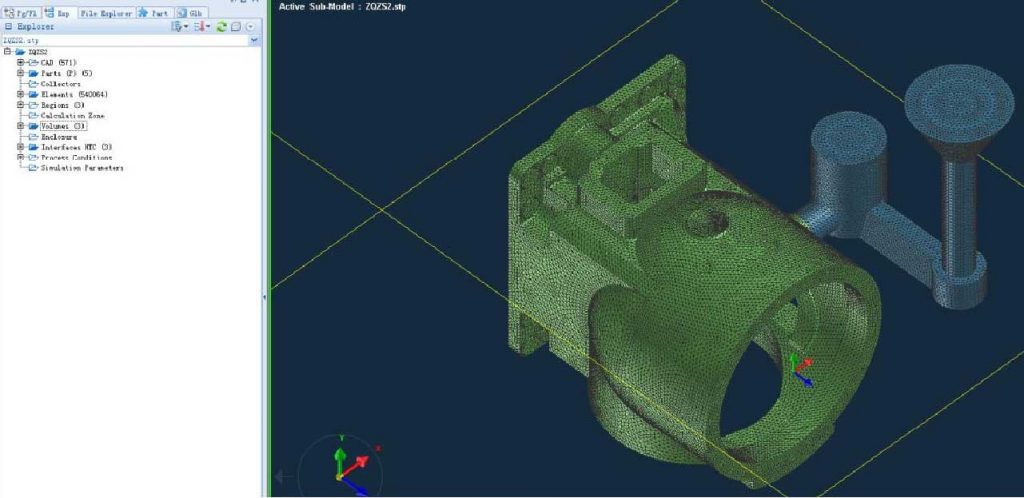
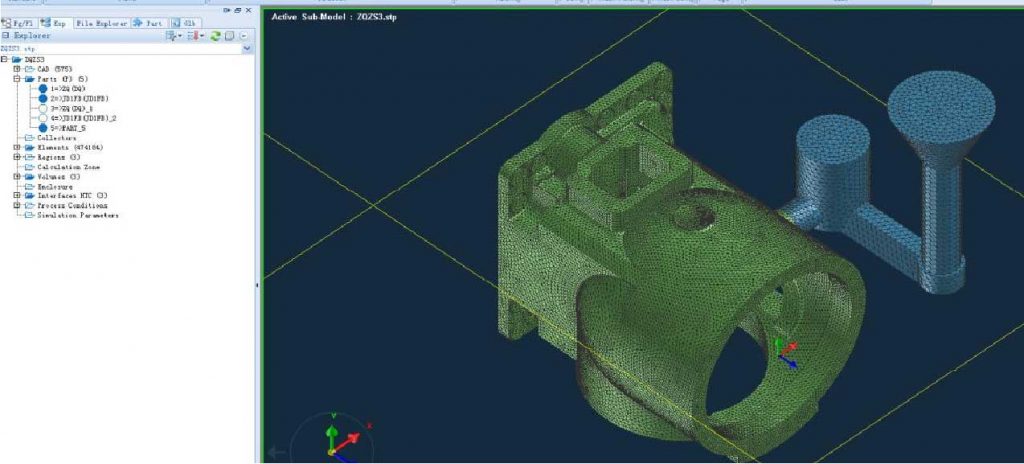
As shown in Fig. 1, Fig. 2 and Fig. 3, the mesh generation diagrams of closed, open and semi closed schemes are shown in turn. In this model, mesh is divided by ProCAST software mesh. In the process of mesh generation, in order to ensure that CAE simulation can not be distorted, it is very important to select the unit length of mesh. If the unit length of mesh is too large, the number of meshes is small, the simulation is not accurate, the unit length of mesh is too small and the number of meshes is too large, which increases the amount of calculation and calculation time. In this simulation, the unit length of the grid of the bridge shell is 6 mm, the length of the grid element of the runner is 15 mm, and the virtual sand box is used. After the unit length is selected, mesh face mesh is divided, checked and repaired. After the face mesh is qualified, the volume mesh and check volume mesh are generated.