Using ProCAST through The computer numerical simulation software is used to simulate the gating system of the axle housing. The rationality of the three pouring schemes is verified by observing the filling process and temperature field of the gating system, as well as the distribution of shrinkage porosity and shrinkage cavity of liquid metal. The optimal gating system scheme is determined. The feeding capacity of the axle housing is improved by adding risers and the local solidification is realized by cold iron For the theoretical basis.
Through the comparative analysis of three pouring schemes, the simulation results of three gating systems are compared. To sum up, the improved and optimized three semi closed gating system is regarded as the best casting process of axle housing. The 3D diagram of optimized gating system is shown in the figure.
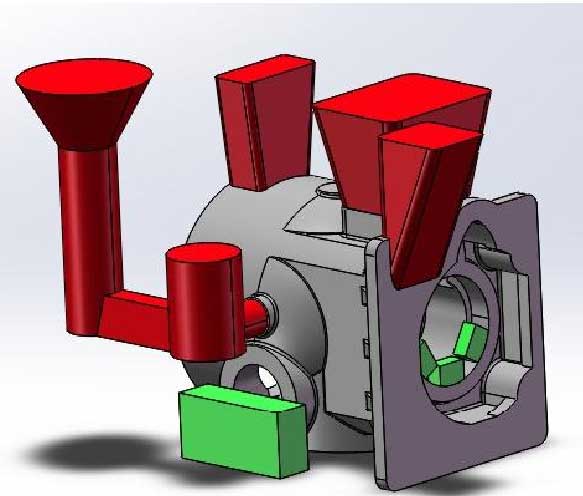
As shown in the figure, the red part is the gating system and the green part is the chill. The tractor split axle housing is made of cast steel zg40mn, the pouring temperature is 1580 ℃ and the pouring time is 10 seconds. One box is one piece, and the gating system is designed as semi closed gating system. The ratio of runner cross-section area: ∑ a inside: ∑ a horizontal: ∑ a straight = 1:0.8:1.2; the gating system has 1 sprue, 1 cross sprue and 1 internal sprue, and the sectional area of ingate is 22.5 The cross-sectional area of the runner is 18 cm2, and the size is shown in Fig. 3-9. The cross-sectional area of the sprue is 27 cm2. The open riser is located on the upper surface of the axle housing, the inner cold iron is placed in the inner cavity of the axle housing, and the outer cold iron is placed at the larger wall thickness.