Heat treatment techniques play a crucial role in unlocking the potential of castings, enabling the production of superior and high-performance components. By carefully controlling the heating and cooling processes, heat treatment can enhance the mechanical properties, improve the microstructure, and increase the overall strength and durability of castings. Here are some key heat treatment techniques commonly used in the casting industry:
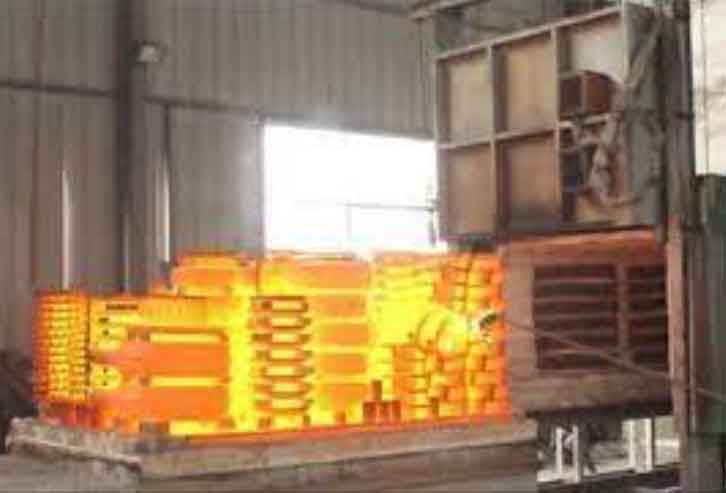
- Annealing: Annealing involves heating the casting to a specific temperature and holding it there for a certain period, followed by slow cooling. This process helps relieve internal stresses, improve ductility, and refine the grain structure of the material. Annealing is often used after casting to minimize distortion and improve machinability.
- Normalizing: Normalizing is similar to annealing but involves air cooling instead of slow cooling. It is commonly used to refine the grain structure and produce a more uniform hardness throughout the casting. Normalizing can also enhance the mechanical properties, such as tensile strength and toughness.
- Quenching: Quenching is a rapid cooling process that involves immersing the casting in a quenching medium, such as water, oil, or polymer. This rapid cooling produces a hardened microstructure, increasing the material’s hardness and strength. However, quenching can also introduce internal stresses and make the casting more brittle. To reduce brittleness, a subsequent tempering process is often performed.
- Tempering: Tempering is a heat treatment process that follows quenching. It involves reheating the casting to a specific temperature below its critical point and holding it there for a certain period, followed by air cooling. Tempering reduces the brittleness caused by quenching and increases the toughness and ductility of the material. The exact temperature and duration of tempering depend on the desired properties of the casting.
- Stress Relieving: Stress relieving is a heat treatment process used to reduce residual stresses in castings. It involves heating the casting to a specific temperature below its transformation range and maintaining that temperature for a sufficient time, followed by slow cooling. Stress relieving helps improve dimensional stability, reduce the risk of cracking, and enhance the overall stability of the casting.
- Solution Heat Treatment: Solution heat treatment is often applied to alloys, such as aluminum or magnesium castings. It involves heating the casting to a specific temperature to dissolve the alloying elements uniformly throughout the material, followed by rapid cooling. This process helps achieve the desired mechanical properties, such as improved strength and corrosion resistance.
- Aging: Aging is a heat treatment process that follows solution heat treatment. It involves reheating the casting to a specific temperature and holding it there for an extended period. Aging allows the alloying elements to precipitate, resulting in the formation of fine particles within the microstructure. This process further improves the strength and hardness of the casting.
It’s important to note that the specific heat treatment technique and parameters used depend on various factors, including the type of casting material, desired properties, component geometry, and application requirements. Proper process control and monitoring are essential to ensure consistent and optimal results.
In summary, heat treatment techniques offer significant benefits in the casting industry by enhancing the mechanical properties, refining microstructures, and improving the overall performance of castings. By harnessing these techniques effectively, manufacturers can unlock the full potential of castings and produce superior components with enhanced strength, durability, and reliability.