Gate valve bodies, like any other manufactured component, can occasionally have defects that may impact their performance or functionality. Here are some common defects in gate valve bodies, along with their causes, identification methods, and possible solutions:
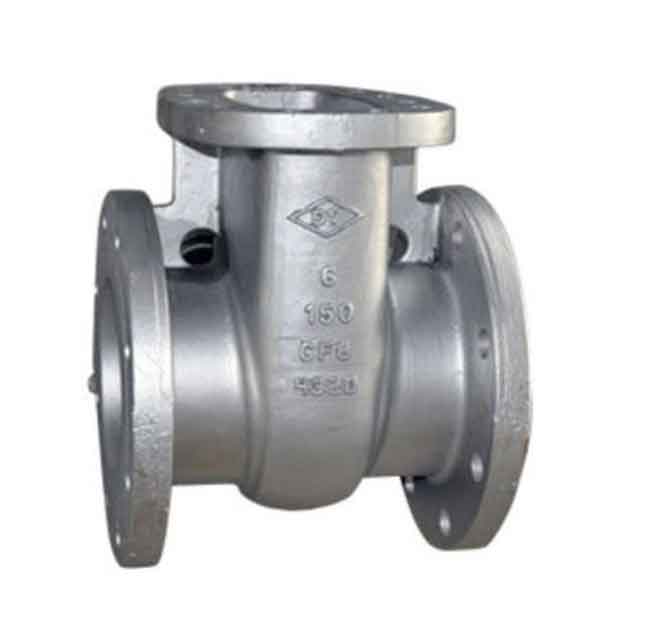
- Porosity:
- Cause: Porosity refers to the presence of voids or gas pockets within the gate valve body, which can occur during the casting process due to inadequate mold filling or gas entrapment.
- Identification: Porosity is often identified through visual inspection, where small holes or gaps are visible on the surface of the valve body.
- Solution: Increasing the mold filling rate, optimizing gating system design, and ensuring proper venting during casting can help minimize porosity. If porosity is detected, it may require repair through methods such as welding, grinding, or using appropriate sealants.
- Inclusions:
- Cause: Inclusions are foreign materials (e.g., sand, slag, or non-metallic particles) that are trapped within the gate valve body during the casting process or introduced during material preparation.
- Identification: Inclusions can be identified through visual inspection or non-destructive testing methods such as ultrasonic testing or X-ray inspection.
- Solution: Implementing stringent quality control measures during material preparation and casting can help minimize the occurrence of inclusions. If detected, removal or repair may be necessary depending on the severity.
- Surface Imperfections:
- Cause: Surface imperfections can arise due to factors like improper gating design, mold misalignment, or inadequate surface finish.
- Identification: Surface imperfections such as cracks, scratches, or rough surfaces can be visually inspected.
- Solution: Implementing proper gating design, ensuring proper mold alignment, and employing appropriate finishing techniques like grinding, polishing, or shot blasting can help address surface imperfections.
- Dimensional Deviations:
- Cause: Dimensional deviations can result from factors like improper mold shrinkage allowance, inaccurate machining, or distortion during heat treatment.
- Identification: Dimensional deviations are typically identified through dimensional inspection using measurement tools such as calipers, micrometers, or CMM (Coordinate Measuring Machine).
- Solution: Ensuring accurate mold shrinkage allowance, implementing precise machining processes, and controlling heat treatment parameters can help minimize dimensional deviations. If deviations are significant, rework or replacement of the gate valve body may be necessary.
- Cracks or Fractures:
- Cause: Cracks or fractures can occur due to various factors such as excessive internal stress, improper cooling during casting, or mechanical damage during handling or installation.
- Identification: Visual inspection or non-destructive testing methods like dye penetrant testing or magnetic particle inspection can detect cracks or fractures.
- Solution: Implementing proper cooling procedures during casting, avoiding excessive stress during manufacturing and handling, and adhering to proper installation guidelines can help prevent cracks or fractures. If cracks are identified, the valve body may need repair or replacement.
It’s important to note that defect prevention is crucial in ensuring the quality of gate valve bodies. Employing robust quality control measures throughout the manufacturing process, adhering to industry standards, and continuously improving manufacturing techniques can help minimize defects and ensure reliable gate valve bodies.