In the situation of fierce market competition, under the premise of ensuring product quality, energy saving and consumption reduction is an important means for enterprises to improve economic benefits. No matter whether quenching + high temperature tempering or energy-saving waste heat quenching + high temperature tempering are used, the microstructure defects of parts are inevitable due to improper process or operation during the heat treatment of quenched and tempered steel. The microstructure defect of steel after heat treatment refers to the microstructure defect that can only be identified by metallographic microscope. The common structural defects of heat treatment include deformation, network carbide, poor spheroidization, overheating and overburning, oxidation and decarburization of steel surface, incomplete quenching and quenching cracks. The existence of these structural defects will have an adverse impact on the mechanical properties and process properties of the steel, and even make the parts invalid and scrapped in the service process.
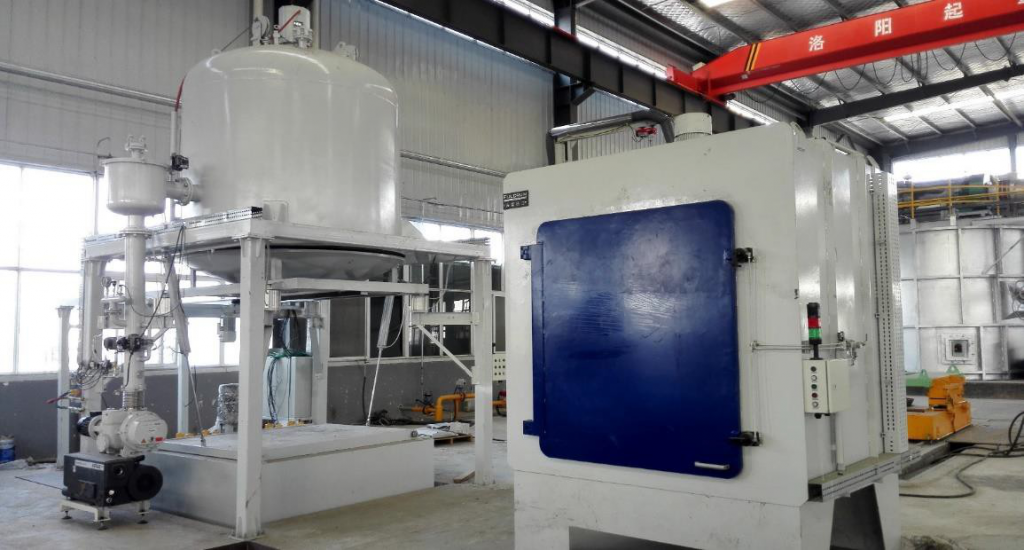
It can be seen that the quenching and tempering treatment of automobile connecting rod of quenched and tempered steel has shortcomings. It not only consumes a lot of materials and human resources and brings pollution, but also inevitably causes deformation and even cracking of the workpiece. Improper quenching and tempering will also cause early failure of the parts in the use process, and quenching deformation increases the difficulty of correction and the manufacturing cost.
The automobile connecting rod is called the safety part in the engine. Its main function is to drive the crankshaft to run at high speed and transmit output power. Because it bears heavy load, impact and vibration in harsh environment, it must have certain reliability and safety, as well as high strength, high wear resistance and fatigue resistance. Therefore, the product design and manufacturing process are highly valued.
Due to the unstable heat treatment process of quenched and tempered steel automobile connecting rod, the qualified rate of inspection after heat treatment is only 60-80%. However, when the automobile connecting rod of microalloyed non quenched and tempered steel is in the air cooling state after forging, a large number of fine V and Ti carbonitrides are dispersed in the ferrite matrix and pearlite matrix of the non quenched and tempered steel. Through precipitation strengthening and fine grain strengthening, microalloyed non quenched and tempered steel automobile connecting rod has better strength and toughness. The strength is higher than that of the quenched and tempered steel automobile connecting rod, but the toughness is slightly poor. The fatigue property of the quenched and tempered steel automobile connecting rod is the same as that of the quenched and tempered steel automobile connecting rod. Due to the cancellation of quenching and tempering process, compared with quenched and tempered steel automobile connecting rod, it has the advantages of energy saving, material saving, cost reduction, product performance improvement and green environmental protection. Its application scope is expanding day by day. It has become the development trend of forgings and heat-treated parts in the automobile industry, and is expanding its application in other fields.