When examining the casting process of cylinder head, it is necessary to avoid unreasonable structure affecting mold parting or casting process design.
1. Realize mold opening
The product structure of cylinder head shall avoid sharp corners in die design or large height difference and weak shape in parting. For example, as shown in Figure 1, for the inclined column structure inside the water chamber of a cylinder head, the inclination of the inclined column is large when making the water jacket core, and sharp corners will be formed during the parting of the sand core mold. The shape can be corrected at both ends of the inclined column to facilitate the parting, and also increase the matching area between the molds after parting.
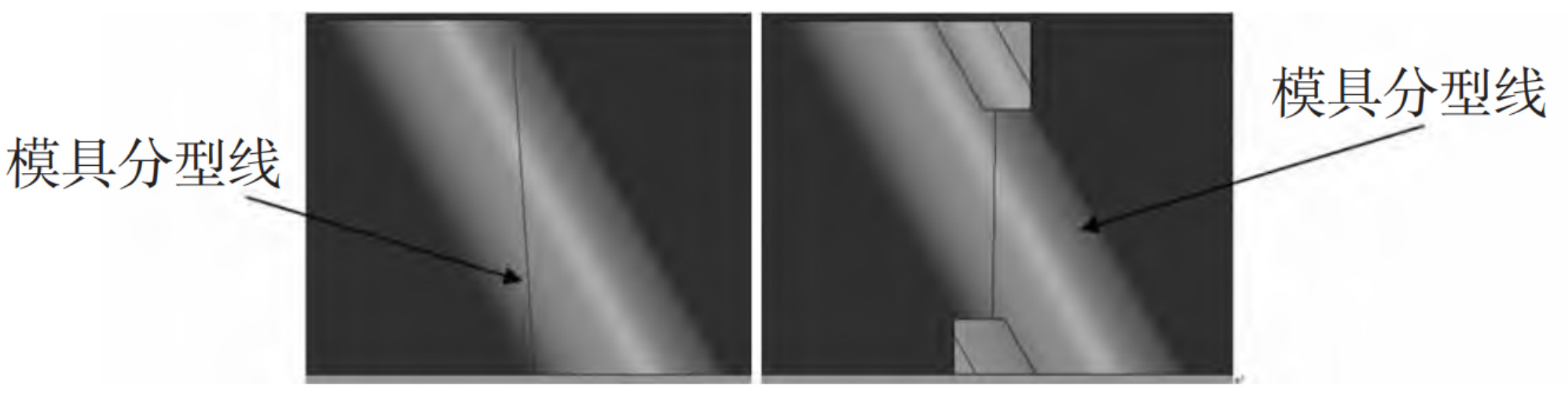
2. Core assembly process can be realized
The cylinder head product structure should avoid interference during sand core assembly. For example, in Figure 2, the inner cavity design of a cylinder head has interference between the air duct core and the water jacket core assembly, so the shape of the water jacket or air duct should be modified to avoid interference, so as to ensure that the assembly core does not interfere.
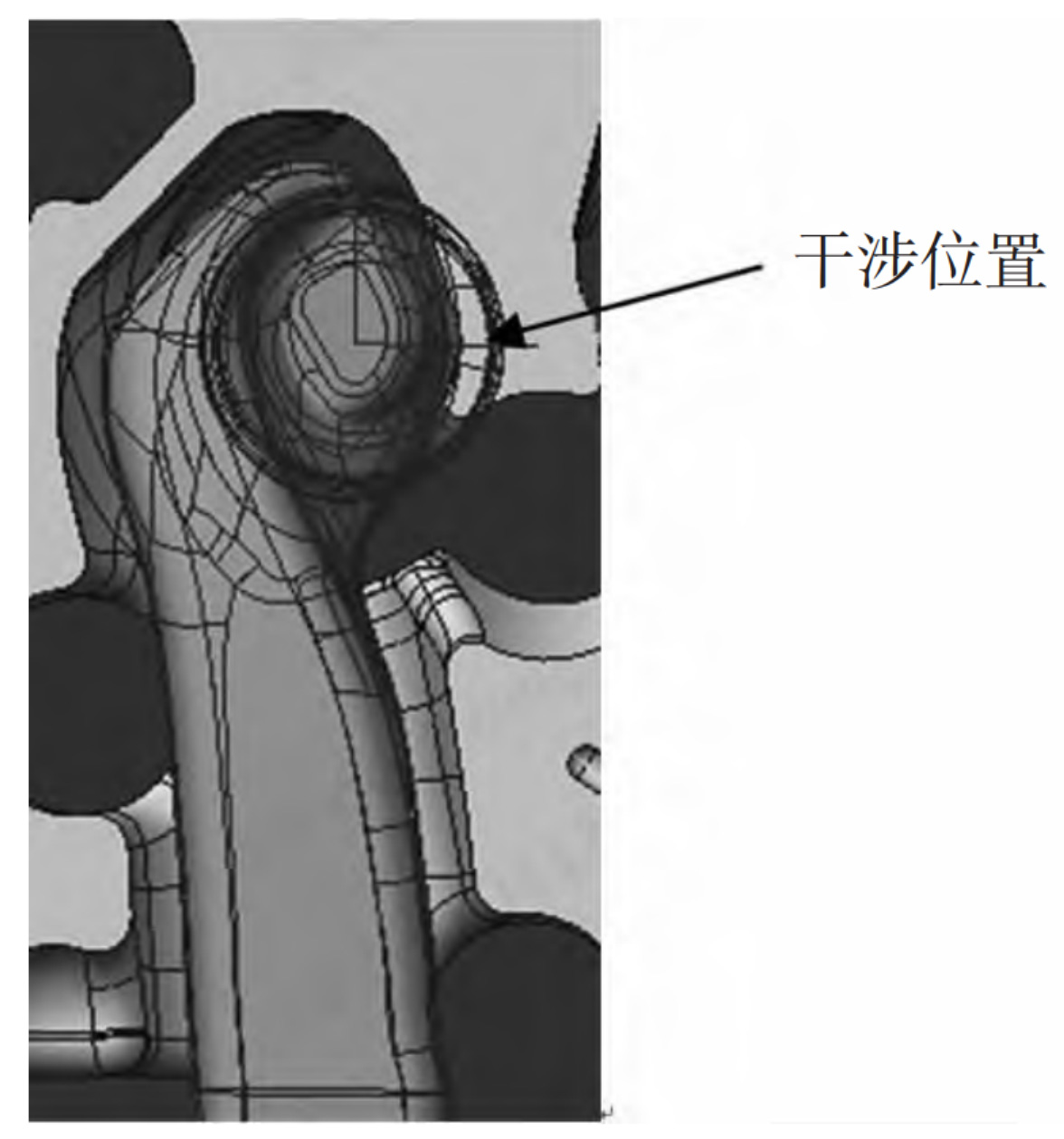
3. Other common influencing factors
In addition to the above factors, the product structure also has many common factors that affect the casting process. For example, the wall thickness of the cylinder head shall be as uniform as possible; Core assembly shall avoid unstable and unsupported center of gravity of sand core; The water jacket core and other structures that are difficult to clean shall be avoided; Ensure enough process holes are used for sand removal, positioning, support and exhaust.