The heat treatment process of Si Mn alloyed ductile iron is similar to that of other ductile iron, which can be generally divided into three stages: heating, quenching, tempering or isothermal. The heating process curve is shown in Figure 1.
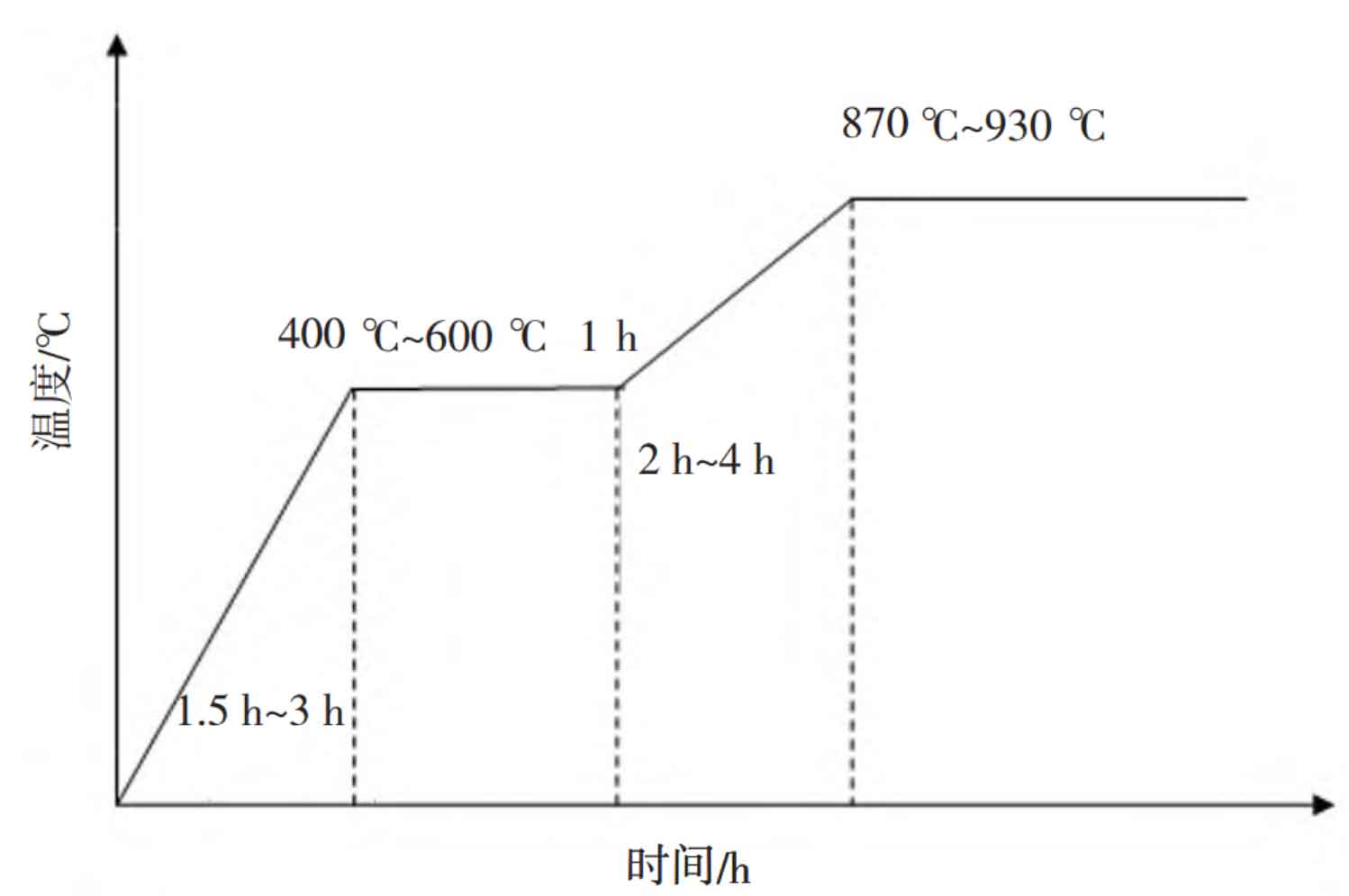
The heating at the low temperature stage shall be slow and sufficient. After reaching the austenitizing temperature, there shall be an appropriate holding time to create favorable conditions for the diffusion of carbon and related alloy elements. The change of metallographic structure after quenching shall be fine tuned by adjusting the austenitizing temperature and holding time to meet the requirements of different working conditions on the grinding ball performance.
The Si Mn alloyed ductile iron ball must pass through the pearlite transformation zone of C curve rapidly after being put into liquid. In the low temperature stage of the late quenching period, it needs to be cooled slowly to carry out martensitic transformation. The quenching process can be effectively controlled by strictly selecting the cooling medium, ensuring that the cooling characteristics meet the process requirements, and controlling the process parameters such as the ball inlet and outlet temperature and time. The internal stress of the quenched grinding ball is very large due to the structure transformation. At this time, the brittleness of the grinding ball is large, so it is required to enter the tempering stage in time for full tempering.
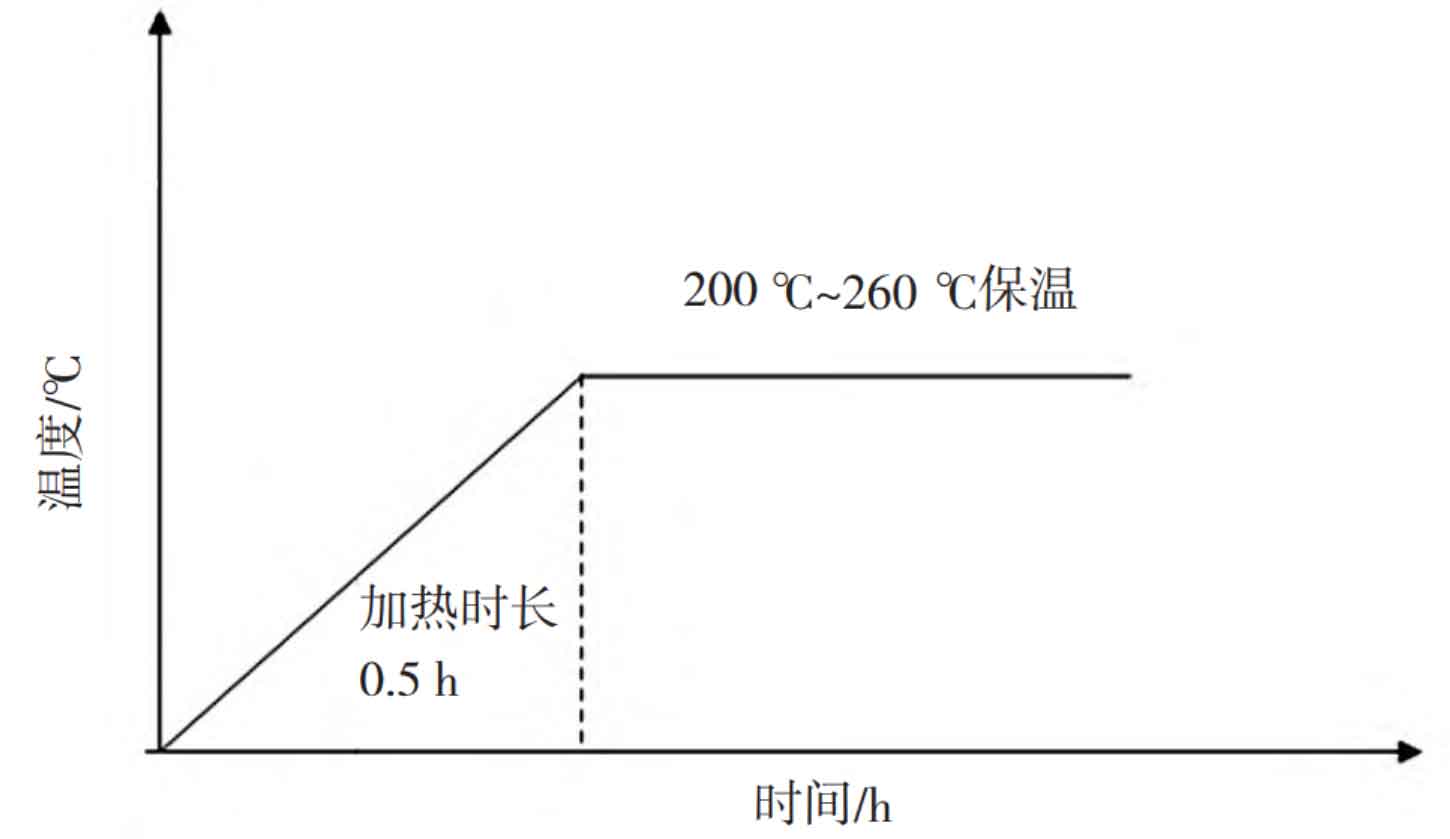
Tempering is very important to improve the toughness and stability of Si Mn alloyed ductile iron grinding balls. The tempering curve is shown in Figure 2.