Spheroidal Graphite Cast Iron is prized for its excellent mechanical properties, including high tensile strength, ductility, and toughness. These properties can be further enhanced through various heat treatment processes. Heat treatment is a controlled process used to alter the microstructure of Spheroidal Graphite Cast Iron to improve its mechanical properties, making it suitable for a wider range of applications. This article explores the different heat treatment processes for Spheroidal Graphite Cast Iron and their impact on its properties.
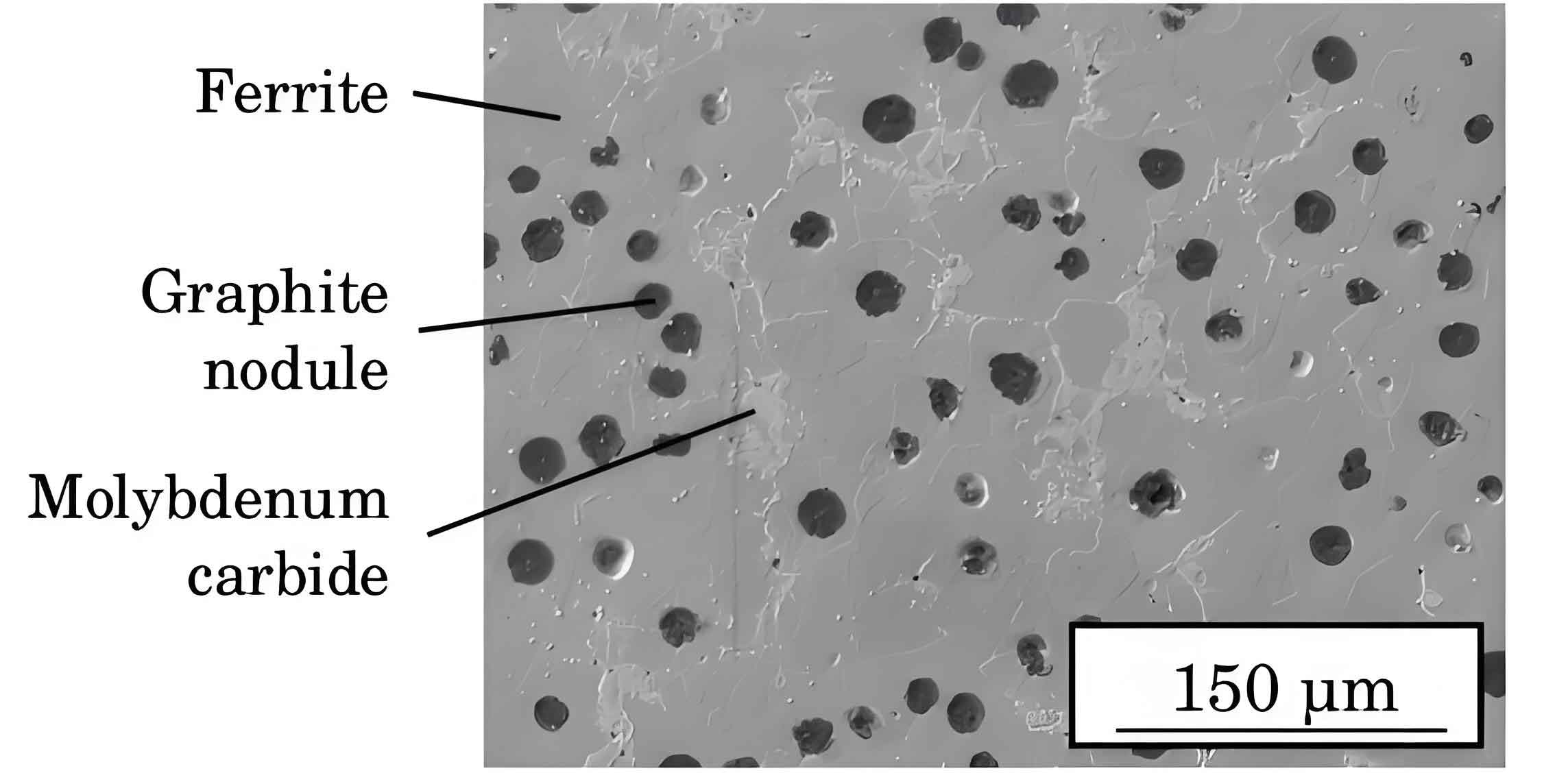
Overview of Heat Treatment
Heat treatment involves heating and cooling metals in a controlled manner to achieve desired mechanical properties and microstructures. For Spheroidal Graphite Cast Iron, heat treatment processes can significantly influence the distribution and morphology of graphite nodules and the matrix structure, thereby enhancing its mechanical performance.
Key Objectives of Heat Treatment for Spheroidal Graphite Cast Iron
- Improve Strength: Increase tensile and yield strength.
- Enhance Ductility: Improve the ability to deform without cracking.
- Increase Toughness: Enhance resistance to impact and fracture.
- Improve Wear Resistance: Enhance surface hardness and wear resistance.
- Refine Microstructure: Achieve a more uniform and desirable microstructure.
Table 1: Objectives of Heat Treatment for Spheroidal Graphite Cast Iron
Objective | Description |
---|---|
Improve Strength | Increase tensile and yield strength |
Enhance Ductility | Improve the ability to deform without cracking |
Increase Toughness | Enhance resistance to impact and fracture |
Improve Wear Resistance | Enhance surface hardness and wear resistance |
Refine Microstructure | Achieve a more uniform and desirable microstructure |
Common Heat Treatment Processes for Spheroidal Graphite Cast Iron
1. Annealing
Annealing is a heat treatment process used to soften Spheroidal Graphite Cast Iron, improve ductility, and relieve internal stresses. It involves heating the iron to a specific temperature, holding it for a period, and then cooling it slowly.
Process Description
- Heating: The iron is heated to a temperature range of 850-950°C.
- Holding: The temperature is maintained to allow for complete transformation of the matrix.
- Cooling: Slow cooling in the furnace to ensure uniformity and prevent the formation of internal stresses.
Benefits
- Reduced Hardness: Makes the iron easier to machine.
- Improved Ductility: Enhances the ability to deform without cracking.
- Stress Relief: Reduces residual stresses from casting.
List 1: Benefits of Annealing
- Reduced hardness.
- Improved ductility.
- Stress relief.
2. Normalizing
Normalizing is used to refine the grain structure of Spheroidal Graphite Cast Iron and improve its mechanical properties. The process involves heating the iron to a temperature above its transformation range and then air cooling.
Process Description
- Heating: The iron is heated to a temperature of 850-950°C.
- Holding: Held at this temperature to ensure complete transformation.
- Cooling: Air cooling to achieve a fine-grained pearlitic matrix.
Benefits
- Refined Grain Structure: Enhances mechanical properties and uniformity.
- Increased Strength: Improves tensile and yield strength.
- Enhanced Toughness: Better resistance to impact and fracture.
Table 2: Benefits of Normalizing
Benefit | Description |
---|---|
Refined Grain Structure | Enhances mechanical properties and uniformity |
Increased Strength | Improves tensile and yield strength |
Enhanced Toughness | Better resistance to impact and fracture |
3. Austempering
Austempering is an advanced heat treatment process that produces a bainitic microstructure, enhancing the strength, toughness, and wear resistance of Spheroidal Graphite Cast Iron. It involves heating, quenching in a salt bath, and holding at a specific temperature before cooling.
Process Description
- Heating: The iron is heated to 830-950°C.
- Quenching: Quenched in a salt bath at 250-400°C.
- Holding: Held at this temperature to achieve the desired bainitic microstructure.
- Cooling: Air cooled to room temperature.
Benefits
- Improved Strength and Toughness: The bainitic structure provides a balance of strength and toughness.
- Enhanced Wear Resistance: Better performance in wear-intensive applications.
- Reduced Distortion: Uniform microstructure reduces the risk of distortion during cooling.
List 2: Benefits of Austempering
- Improved strength and toughness.
- Enhanced wear resistance.
- Reduced distortion.
4. Quenching and Tempering
Quenching and tempering is a two-step heat treatment process that increases the hardness and strength of Spheroidal Graphite Cast Iron. The process involves rapid cooling (quenching) followed by reheating to a lower temperature (tempering).
Process Description
- Quenching: The iron is heated to 850-950°C and then rapidly cooled in water or oil.
- Tempering: Reheated to 250-700°C to achieve the desired balance of hardness and toughness.
Benefits
- Increased Hardness: Improves wear resistance.
- Controlled Toughness: Balances hardness with toughness to prevent brittleness.
- Versatility: Can be adjusted to achieve specific mechanical properties.
Table 3: Benefits of Quenching and Tempering
Benefit | Description |
---|---|
Increased Hardness | Improves wear resistance |
Controlled Toughness | Balances hardness with toughness to prevent brittleness |
Versatility | Can be adjusted to achieve specific properties |
5. Surface Hardening
Surface hardening processes, such as induction hardening and case hardening, are used to increase the surface hardness of Spheroidal Graphite Cast Iron while maintaining a tough and ductile core.
Process Description
- Induction Hardening: The surface is heated rapidly by induction coils and then quenched.
- Case Hardening: The surface is enriched with carbon or nitrogen and then heat treated.
Benefits
- Enhanced Surface Hardness: Improves wear resistance on the surface.
- Maintained Core Toughness: Ensures the core remains tough and ductile.
- Improved Fatigue Resistance: Surface hardness increases resistance to fatigue.
List 3: Benefits of Surface Hardening
- Enhanced surface hardness.
- Maintained core toughness.
- Improved fatigue resistance.
Comparison of Heat Treatment Processes
Different heat treatment processes offer various benefits for Spheroidal Graphite Cast Iron. Choosing the appropriate process depends on the desired mechanical properties and application requirements.
Table 4: Comparison of Heat Treatment Processes
Process | Benefits | Typical Applications |
---|---|---|
Annealing | Reduced hardness, improved ductility, stress relief | Machining, stress-relieved components |
Normalizing | Refined grain structure, increased strength, enhanced toughness | Structural components, automotive parts |
Austempering | Improved strength and toughness, enhanced wear resistance, reduced distortion | Gears, heavy machinery, automotive components |
Quenching and Tempering | Increased hardness, controlled toughness, versatility | Wear-resistant parts, tools, dies |
Surface Hardening | Enhanced surface hardness, maintained core toughness, improved fatigue resistance | Shafts, gears, high-wear surfaces |
Conclusion
Heat treatment processes play a crucial role in enhancing the mechanical properties and performance of Spheroidal Graphite Cast Iron. By carefully selecting and applying processes such as annealing, normalizing, austempering, quenching and tempering, and surface hardening, manufacturers can optimize the material for a wide range of applications. These processes not only improve strength, ductility, and toughness but also enhance wear resistance and fatigue resistance, making Spheroidal Graphite Cast Iron an even more versatile and valuable material. As technology advances and new heat treatment techniques are developed, the potential for further improvements in the properties and applications of Spheroidal Graphite Cast Iron continues to grow.