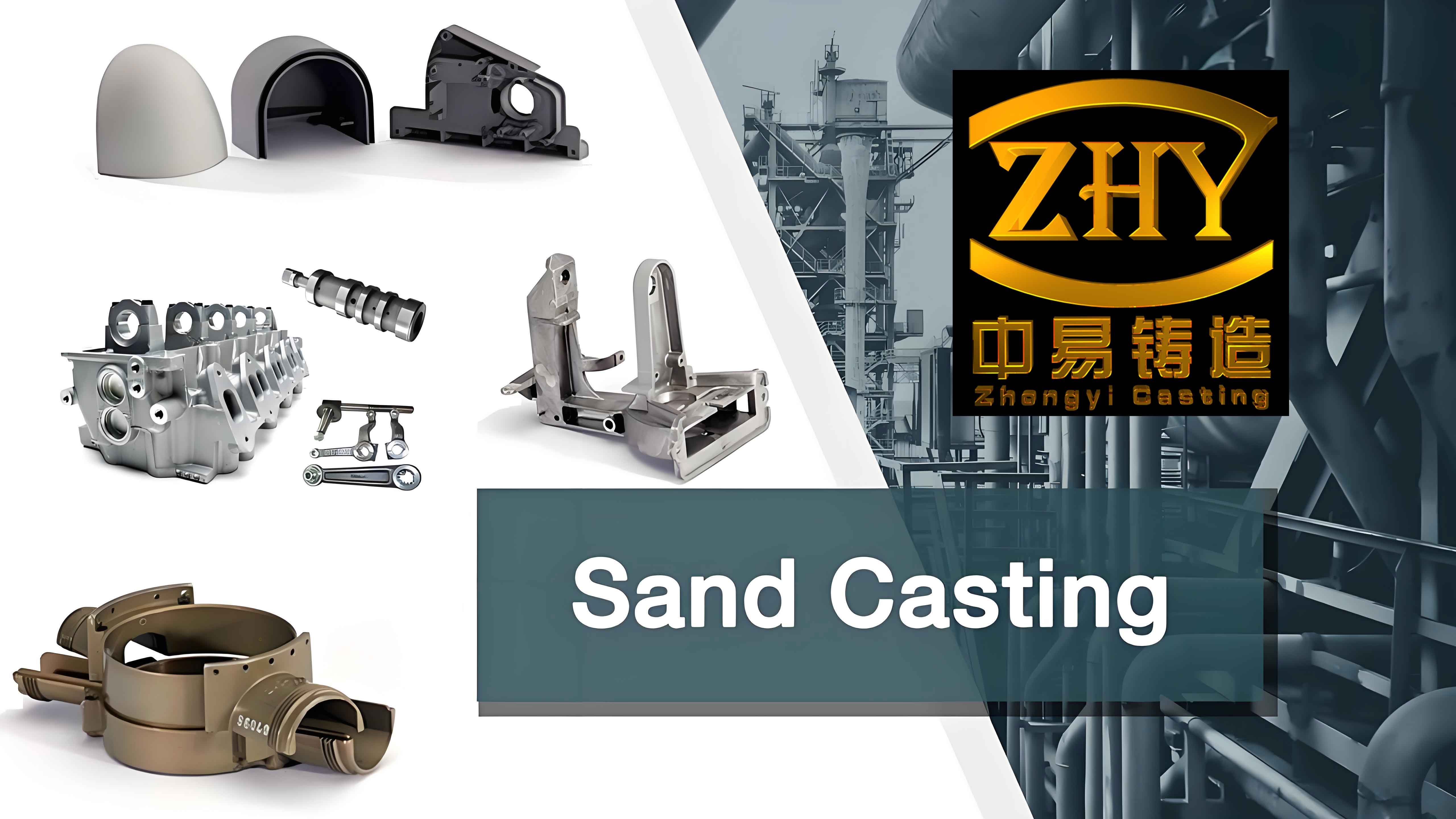
Heat treatment is crucial process in the manufacturing of sand casted parts. It involves the controlled heating and cooling of the casted components to alter their physical and mechanical properties without changing their shape. Heat treatment processes are essential for enhancing the strength, hardness, ductility, toughness, and overall performance of sand casted parts. This article explores the various heat treatment processes used in sand casting, their benefits, and their applications.
Importance of Heat Treatment in Sand Casting
Heat treatment processes play a vital role in improving the quality and performance of sand casted components. The key benefits include:
- Improved Mechanical Properties
- Heat treatment enhances the strength, hardness, and toughness of sand casted parts, making them more suitable for demanding applications.
- Refinement of Microstructure
- The process refines the grain structure of the metal, reducing internal stresses and improving overall material properties.
- Enhanced Wear Resistance
- Heat-treated components exhibit better wear resistance, increasing their lifespan and reducing maintenance costs.
- Stress Relief
- Heat treatment relieves internal stresses induced during the casting process, preventing deformation and potential failure.
Common Heat Treatment Processes in Sand Casting
1. Annealing
Annealing is a heat treatment process that involves heating the sand casted part to a specific temperature, holding it at that temperature for a certain period, and then slowly cooling it. This process softens the metal, improves its ductility, and relieves internal stresses.
Steps in Annealing:
- Heating
- The sand casted part is heated to a temperature above its recrystallization temperature.
- Holding
- The part is held at this temperature for a specific duration to allow for recrystallization and stress relief.
- Cooling
- The part is slowly cooled to room temperature to prevent the formation of new stresses.
Parameter | Details |
---|---|
Temperature Range | 550°C to 950°C (depends on material) |
Holding Time | 1 to 2 hours (depends on part size) |
Cooling Method | Slow cooling in a furnace |
2. Normalizing
Normalizing involves heating the sand casted part to a temperature above its critical point, followed by air cooling. This process refines the grain structure, enhances mechanical properties, and ensures uniformity in the material.
Steps in Normalizing:
- Heating
- The part is heated to a temperature above its critical point.
- Holding
- The part is held at this temperature for a specific duration to achieve uniform heating.
- Cooling
- The part is allowed to cool in air, resulting in a refined grain structure.
Parameter | Details |
---|---|
Temperature Range | 800°C to 950°C (depends on material) |
Holding Time | 30 minutes to 1 hour |
Cooling Method | Air cooling |
3. Quenching and Tempering
Quenching and tempering is a two-step heat treatment process that involves rapid cooling (quenching) followed by reheating to a lower temperature (tempering). This process increases the hardness and strength of the sand casted part while reducing brittleness.
Steps in Quenching and Tempering:
- Quenching
- The part is heated to a high temperature and then rapidly cooled in water, oil, or air.
- Tempering
- The quenched part is reheated to a lower temperature and held for a specific duration, then cooled again.
Parameter | Details |
---|---|
Quenching Temperature | 800°C to 900°C (depends on material) |
Quenching Medium | Water, oil, or air |
Tempering Temperature | 150°C to 700°C (depends on material) |
Holding Time (Tempering) | 1 to 2 hours |
4. Stress Relieving
Stress relieving involves heating the sand casted part to a temperature below its recrystallization temperature, holding it at that temperature, and then cooling it slowly. This process reduces residual stresses without significantly altering the mechanical properties.
Steps in Stress Relieving:
- Heating
- The part is heated to a temperature below its recrystallization point.
- Holding
- The part is held at this temperature to allow stress relief.
- Cooling
- The part is slowly cooled to room temperature.
Parameter | Details |
---|---|
Temperature Range | 400°C to 650°C (depends on material) |
Holding Time | 1 to 2 hours |
Cooling Method | Slow cooling in a furnace |
5. Solution Treatment
Solution treatment, also known as solution annealing, involves heating the sand casted part to a high temperature to dissolve soluble elements and then rapidly cooling it to retain the dissolved elements in solution. This process enhances the mechanical properties and corrosion resistance of the part.
Steps in Solution Treatment:
- Heating
- The part is heated to a high temperature to dissolve alloying elements.
- Holding
- The part is held at this temperature to ensure complete dissolution.
- Cooling
- The part is rapidly cooled to retain the dissolved elements in solution.
Parameter | Details |
---|---|
Temperature Range | 950°C to 1050°C (depends on material) |
Holding Time | 30 minutes to 1 hour |
Cooling Method | Rapid cooling (water or air quenching) |
6. Precipitation Hardening
Precipitation hardening, also known as age hardening, involves heating the sand casted part to a moderate temperature to precipitate secondary phases from the solid solution. This process enhances the hardness and strength of the part.
Steps in Precipitation Hardening:
- Solution Treatment
- The part undergoes solution treatment to dissolve alloying elements.
- Aging
- The solution-treated part is reheated to a lower temperature and held for a specific duration to precipitate secondary phases.
- Cooling
- The part is cooled to room temperature.
Parameter | Details |
---|---|
Aging Temperature | 150°C to 500°C (depends on material) |
Aging Time | 1 to 24 hours (depends on material) |
Cooling Method | Air cooling |
Applications of Heat Treatment in Sand Casting
Automotive Industry
Heat-treated sand casted parts are extensively used in the automotive industry for engine components, transmission parts, and suspension systems. The enhanced mechanical properties and wear resistance make them suitable for high-stress applications.
Aerospace Industry
In the aerospace industry, heat treatment of sand casted parts is crucial for producing components that can withstand extreme temperatures and stresses. This includes turbine blades, structural components, and landing gear parts.
Machinery and Equipment
Heat-treated sand casted parts are used in heavy machinery and equipment for components such as gears, shafts, and bearings. The improved strength and durability are essential for the reliable operation of these machines.
Construction Industry
The construction industry uses heat-treated sand casted parts for various structural components, including beams, columns, and connectors. The enhanced mechanical properties ensure the stability and safety of the structures.
Conclusion
Heat treatment processes are essential for improving the quality and performance of sand casted parts. By understanding and applying the appropriate heat treatment techniques, manufacturers can enhance the mechanical properties, wear resistance, and overall durability of the components. Whether it is annealing, normalizing, quenching and tempering, stress relieving, solution treatment, or precipitation hardening, each process plays a crucial role in refining the microstructure and reducing internal stresses. The application of these heat treatment processes ensures that sand casted parts meet the demanding requirements of various industries, including automotive, aerospace, machinery, and construction. By continually advancing heat treatment technologies, the sand casting industry can produce high-quality, reliable components that drive innovation and progress across multiple sectors.