Achieving dimensional stability in sand castings can be challenging due to the inherent properties of sand molds and the solidification process of the metal. However, heat treatment strategies can be employed to help minimize dimensional changes and improve stability. Here are some heat treatment techniques commonly used for achieving dimensional stability in sand castings:
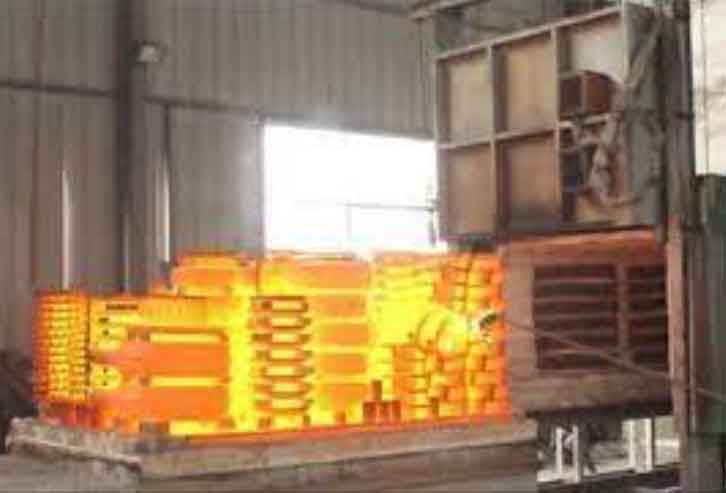
- Stress Relieving: Stress relieving involves heating the castings to a specific temperature below the critical transformation point of the metal and then slowly cooling it. This process helps to relieve internal stresses that may have built up during the casting process. Stress relieving can reduce the risk of distortion and improve dimensional stability.
- Annealing: Annealing is a heat treatment process that involves heating the casting to a specific temperature and holding it at that temperature for a certain duration, followed by controlled cooling. Annealing helps to eliminate internal stresses and refine the grain structure of the metal, improving dimensional stability and reducing the risk of cracking.
- Normalizing: Normalizing is a heat treatment process similar to annealing but involves cooling the casting in still air instead of controlled cooling. Normalizing is often performed on castings with non-uniform section thicknesses to achieve more uniform mechanical properties and dimensional stability throughout the casting.
- Precipitation Hardening: Precipitation hardening is a heat treatment technique used for certain alloys, such as aluminum and some stainless steels. It involves a combination of solution treatment (heating to a specific temperature) and aging (holding at an elevated temperature) to promote the formation of fine precipitates within the metal matrix. Precipitation hardening can enhance the strength and dimensional stability of the castings.
- Controlled Cooling Rates: The cooling rate during solidification and subsequent cooling can significantly affect the dimensional stability of castings. Gradual and controlled cooling rates can help minimize thermal gradients and reduce the risk of cracking or distortion. Different cooling techniques, such as furnace cooling or air cooling, may be employed depending on the specific casting requirements.
It’s important to note that the specific heat treatment strategy depends on the material being cast and the desired properties. It is recommended to consult with metallurgical experts or process engineers familiar with the specific casting material and requirements to determine the most appropriate heat treatment strategy for achieving dimensional stability in sand castings.