Grey cast iron is widely used in a variety of industries due to its unique properties, including excellent castability, high wear resistance, good machinability, and superior vibration damping capacity. Given its widespread usage, understanding the casting processes involved in creating components from grey cast iron is crucial. This article provides a comprehensive overview of those processes.
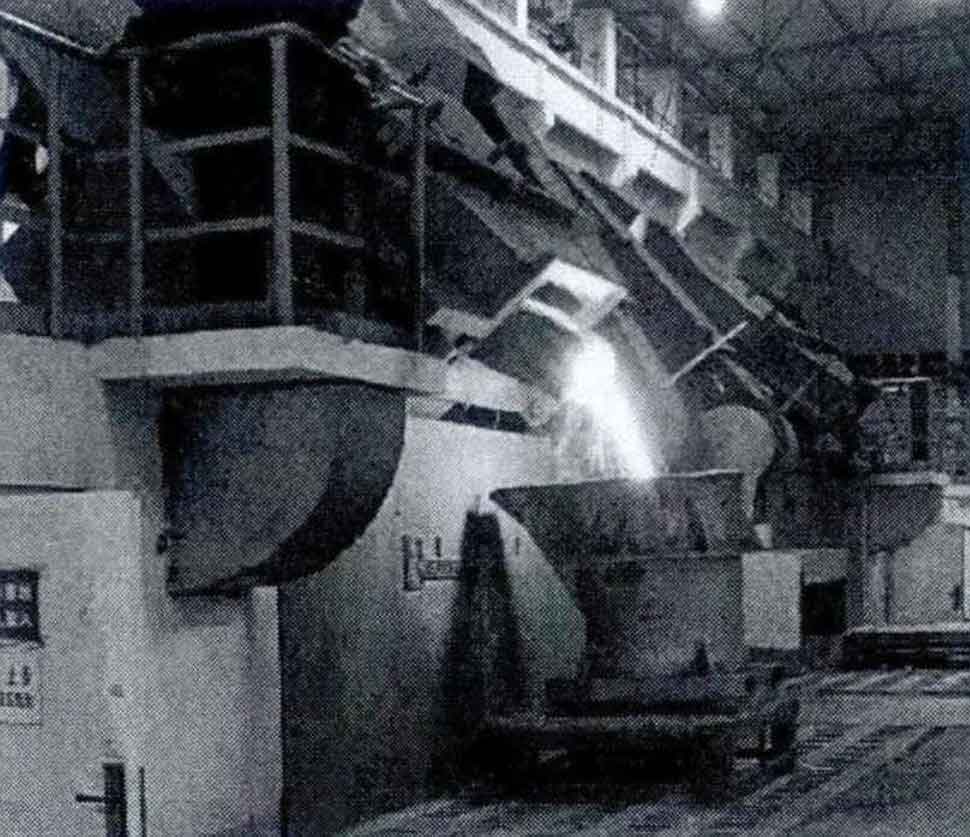
Sand Casting
Sand casting is the most common method used to cast grey iron. This process involves creating a mold from a mixture of sand, clay, and water, which is then packed around a pattern made to the shape of the desired component. Once the pattern is removed, molten grey iron is poured into the mold. After the iron cools and solidifies, the sand mold is broken away to reveal the cast part.
Sand casting is an inexpensive and versatile process, suitable for both small and large components. However, the surface finish and dimensional accuracy of sand-cast parts are generally not as high as those produced by other casting methods.
Die Casting
Die casting is another method used for grey iron, although it’s more common for non-ferrous metals. In this process, molten grey iron is forced into a reusable metal mold under high pressure. This allows for excellent detail and dimensional accuracy, and a good surface finish. However, die casting is generally more expensive than sand casting, primarily due to the high cost of the dies.
Shell Mold Casting
Shell mold casting is a variant of sand casting that offers improved dimensional accuracy and surface finish. In this process, a sand-resin mixture is pre-heated and formed around a pattern. The heated sand-resin mixture hardens to form a shell, which is then separated from the pattern and joined with another shell to form the mold. Molten iron is poured into the mold, and after solidification, the shell mold is broken to release the cast part.
Lost Foam Casting
Lost foam casting, also known as evaporative pattern casting, involves creating a foam pattern which is then coated with refractory material. This coated pattern is placed in a flask and surrounded by unbounded sand. When the molten iron is poured into the flask, the foam pattern evaporates, leaving the cast part. This method can produce parts with complex shapes and excellent dimensional accuracy without the need for cores or parting lines.
Centrifugal Casting
Centrifugal casting is used to produce cylindrical parts such as pipes. In this process, molten grey iron is poured into a rotating mold. The centrifugal force pushes the molten iron against the mold wall, where it solidifies. The rotational motion helps to produce a casting with a uniform thickness and density.
In conclusion, various casting processes can be used for grey cast iron, each offering unique advantages and being suitable for different applications. The choice of process depends on factors such as the complexity of the part, dimensional accuracy requirements, production volume, and cost considerations.