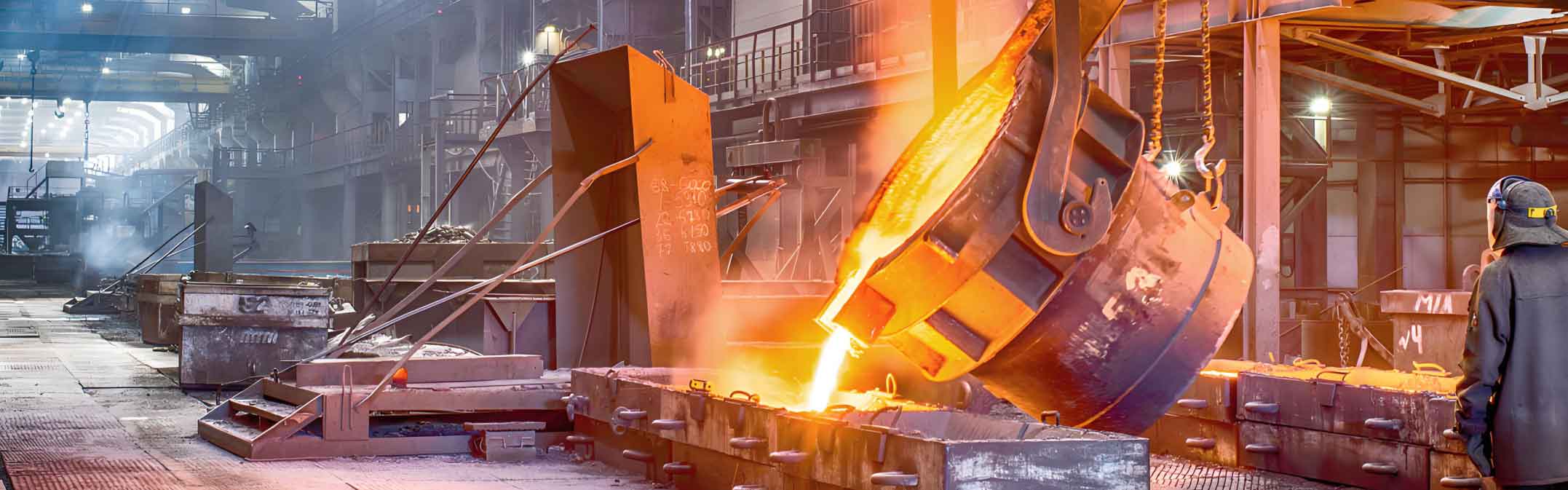
Introduction
Sand casting is a versatile and widely used manufacturing process that involves creating a mold from a sand-based mixture, into which molten metal is poured to form the desired shape. The process has been used for centuries, but recent advancements in material science have led to the development of high-performance alloys that offer superior properties and performance. This article explores these material innovations, their applications, and the benefits they bring to sand casting.
Overview of Sand Casting
The sand casting process consists of several steps:
- Pattern Making: Creating a pattern that resembles the final product.
- Mold Making: Placing the pattern in a flask and packing it with sand to form a mold.
- Core Making: Producing cores for hollow sections within the casting.
- Pouring: Pouring molten metal into the mold cavity.
- Cooling and Shakeout: Allowing the metal to solidify before breaking the mold to retrieve the casting.
- Finishing: Cleaning and finishing the casting to achieve the desired specifications.
High-Performance Alloys: An Overview
High-performance alloys are specially formulated to provide superior mechanical properties, corrosion resistance, and thermal stability compared to traditional metals. These alloys are often used in demanding applications where conventional materials would fail. Key high-performance alloys used in sand casting include:
- Nickel-Based Alloys
- Cobalt-Based Alloys
- Titanium Alloys
- Superalloys
Nickel-Based Alloys
Nickel-based alloys are known for their excellent corrosion resistance, high-temperature strength, and good mechanical properties. Common nickel-based alloys used in sand casting include:
- Inconel: Known for its high strength and resistance to oxidation and corrosion at high temperatures.
- Hastelloy: Offers excellent resistance to a wide range of chemical environments.
- Monel: Combines high strength and excellent corrosion resistance, especially in marine environments.
Applications of Nickel-Based Alloys
- Aerospace Components: Turbine blades, exhaust systems, and heat exchangers.
- Chemical Processing Equipment: Pumps, valves, and reactors.
- Marine Engineering: Propeller shafts, pump impellers, and fasteners.
Properties of Nickel-Based Alloys
Alloy | Tensile Strength (MPa) | Corrosion Resistance | High-Temperature Stability | Common Applications |
---|---|---|---|---|
Inconel | 750-1100 | Excellent | Excellent | Aerospace, Chemical Processing |
Hastelloy | 690-850 | Excellent | Good | Chemical Processing |
Monel | 550-800 | Excellent | Moderate | Marine, Chemical Processing |
Cobalt-Based Alloys
Cobalt-based alloys are valued for their high wear resistance, hardness, and ability to retain strength at elevated temperatures. Common cobalt-based alloys used in sand casting include:
- Stellite: Known for its excellent wear resistance and hardness.
- Ultimet: Combines excellent corrosion resistance with good mechanical properties.
Applications of Cobalt-Based Alloys
- Cutting Tools: Drill bits, saw blades, and machining tools.
- Aerospace Components: Turbine vanes and combustion chamber liners.
- Medical Devices: Prosthetic joints and dental implants.
Properties of Cobalt-Based Alloys
Alloy | Hardness (HRC) | Wear Resistance | High-Temperature Stability | Common Applications |
---|---|---|---|---|
Stellite | 40-60 | Excellent | Excellent | Cutting Tools, Aerospace |
Ultimet | 35-45 | Good | Good | Chemical Processing |
Titanium Alloys
Titanium alloys are known for their high strength-to-weight ratio, excellent corrosion resistance, and biocompatibility. Common titanium alloys used in sand casting include:
- Ti-6Al-4V: The most widely used titanium alloy, known for its excellent mechanical properties and corrosion resistance.
- Ti-5Al-2.5Sn: Offers good high-temperature stability and strength.
Applications of Titanium Alloys
- Aerospace Components: Airframe components, engine parts, and fasteners.
- Medical Devices: Implants, prosthetics, and surgical instruments.
- Automotive Components: High-performance automotive parts.
Properties of Titanium Alloys
Alloy | Tensile Strength (MPa) | Corrosion Resistance | High-Temperature Stability | Common Applications |
---|---|---|---|---|
Ti-6Al-4V | 900-1100 | Excellent | Good | Aerospace, Medical |
Ti-5Al-2.5Sn | 750-850 | Good | Excellent | Aerospace |
Superalloys
Superalloys are a class of high-performance alloys that exhibit excellent mechanical strength, resistance to thermal creep deformation, good surface stability, and resistance to corrosion or oxidation. Common superalloys used in sand casting include:
- Inconel 718: Known for its high strength and resistance to oxidation and corrosion at high temperatures.
- Rene 41: Offers excellent high-temperature strength and oxidation resistance.
Applications of Superalloys
- Aerospace Components: Turbine blades, exhaust systems, and combustion chambers.
- Power Generation: Turbine blades, vanes, and combustors.
- Oil and Gas: Downhole equipment and valves.
Properties of Superalloys
Alloy | Tensile Strength (MPa) | Corrosion Resistance | High-Temperature Stability | Common Applications |
---|---|---|---|---|
Inconel 718 | 1200-1500 | Excellent | Excellent | Aerospace, Power Generation |
Rene 41 | 1150-1350 | Excellent | Excellent | Aerospace, Oil and Gas |
Benefits of High-Performance Alloys in Sand Casting
Advantages:
- Enhanced Mechanical Properties: High strength, hardness, and toughness.
- Corrosion Resistance: Improved resistance to environmental degradation.
- High-Temperature Stability: Ability to retain properties at elevated temperatures.
- Wear Resistance: Superior resistance to wear and abrasion.
Disadvantages:
- Cost: High-performance alloys can be expensive compared to conventional materials.
- Machinability: Some high-performance alloys are challenging to machine and process.
- Availability: Limited availability of certain high-performance alloys can be a constraint.
Innovations in Sand Casting Techniques for High-Performance Alloys
1. Advanced Mold Materials
Using advanced mold materials can improve the quality of castings and reduce defects. Examples include:
- Ceramic Molds: Provide excellent surface finish and dimensional accuracy.
- Graphite Molds: Offer good thermal conductivity and high-temperature stability.
2. Enhanced Cooling Techniques
Implementing enhanced cooling techniques can improve the solidification process and reduce defects. Techniques include:
- Chill Blocks: Using chill blocks to control cooling rates and improve grain structure.
- Controlled Atmosphere Cooling: Using inert gases to control cooling rates and reduce oxidation.
3. Process Automation
Automating various aspects of the sand casting process can enhance efficiency and reduce labor costs. Examples include:
- Automated Pouring Systems: For precise control over the pouring process.
- Robotic Handling: For consistent and repeatable handling of molds and castings.
Case Studies
Case Study 1: Aerospace Turbine Blades
An aerospace manufacturer used nickel-based superalloys to produce turbine blades through sand casting. By implementing advanced mold materials and controlled atmosphere cooling, they achieved a 25% reduction in defects and improved the overall quality of the blades.
Case Study 2: Medical Implants
A medical device company utilized titanium alloys for casting orthopedic implants. Through process automation and the use of ceramic molds, they improved the precision and surface finish of the implants, leading to higher patient satisfaction and reduced production costs.
Comparison of High-Performance Alloys
Alloy | Cost | Mechanical Properties | Corrosion Resistance | High-Temperature Stability | Applications |
---|---|---|---|---|---|
Nickel-Based | High | Excellent | Excellent | Excellent | Aerospace, Chemical |
Cobalt-Based | High | Excellent | Good | Excellent | Cutting Tools, Medical |
Titanium | Very High | Excellent | Excellent | Good | Aerospace, Medical |
Superalloys | Very High | Excellent | Excellent | Excellent | Aerospace, Power Generation |
Future Trends
The future of high-performance alloys in sand casting will likely involve the development of new alloy compositions and improved casting techniques. Key trends include:
- Additive Manufacturing: Combining sand casting with additive manufacturing to create complex geometries and reduce material waste.
- Nano-Engineered Alloys: Developing nano-engineered alloys with enhanced properties for specific applications.
- Sustainability: Focusing on eco-friendly materials and processes to reduce environmental impact.
Conclusion
High-performance alloys in sand casting offer significant advantages in terms of mechanical properties, corrosion resistance, and high-temperature stability. By exploring material innovations and implementing advanced casting techniques, manufacturers can produce high-quality components for demanding applications. While there are challenges associated with cost and machinability, the benefits of using high-performance alloys far outweigh these drawbacks. The future of sand casting will likely see continued advancements in alloy development and casting technologies, leading to even greater performance and efficiency.