Casting hot spot refers to the local area of final solidification formed by the internal solidification speed being slower than that around the casting during solidification. The main hot spot analysis of inlet cylinder casting is shown in Fig. 1.
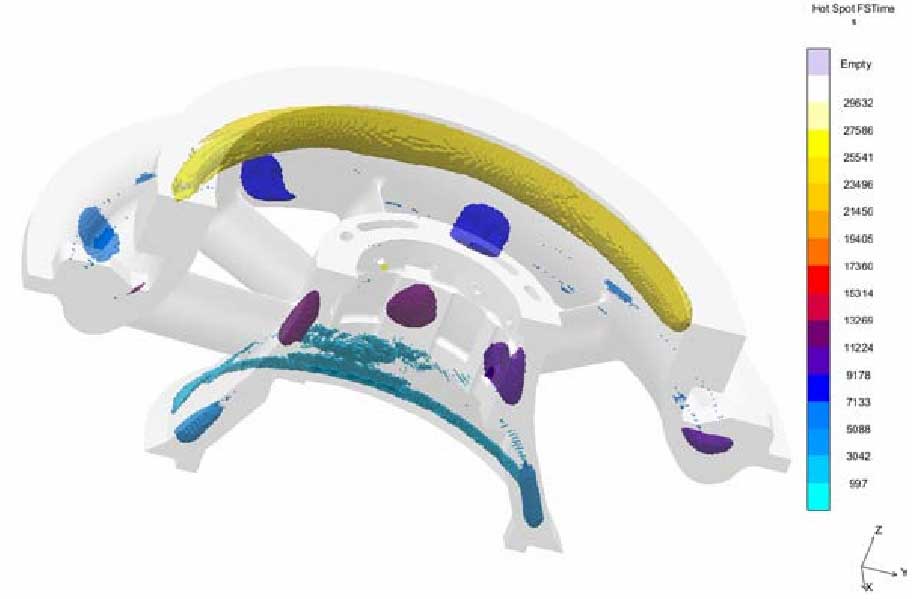
The typical locations of hot spot are as follows: the part with large wall thickness, the cross position of wall thickness, the corner position of casting, the contact position between riser and casting body, etc. Quality problems such as shrinkage cavity, shrinkage porosity, crack, deformation and thermal stress concentration are easy to occur in the hot spot distribution area. These problems are fatal defects for engineering equipment parts, and even lead to direct scrap of castings. According to the hot spot criterion analysis of hot spot simulation results, the hot spot distribution of intake cylinder casting is complex and irregular due to its special structure, and it is segmented and isolated in the height direction of casting position.
In order to understand its solidification characteristics, magam simulation was carried out on the solidification time of intake cylinder casting, and the corresponding analysis was carried out with hot spot distribution. The simulation results are shown in Fig. 2. From the analysis of simulation results, the solidification time of the thick part of the upper part of the casting is more than 16000 s, while most parts are only about 4000 s. The solidification time of each part of the casting is very different. In the simulated fstime criterion analysis, the position with longer time corresponds to the location of hot spot distribution.
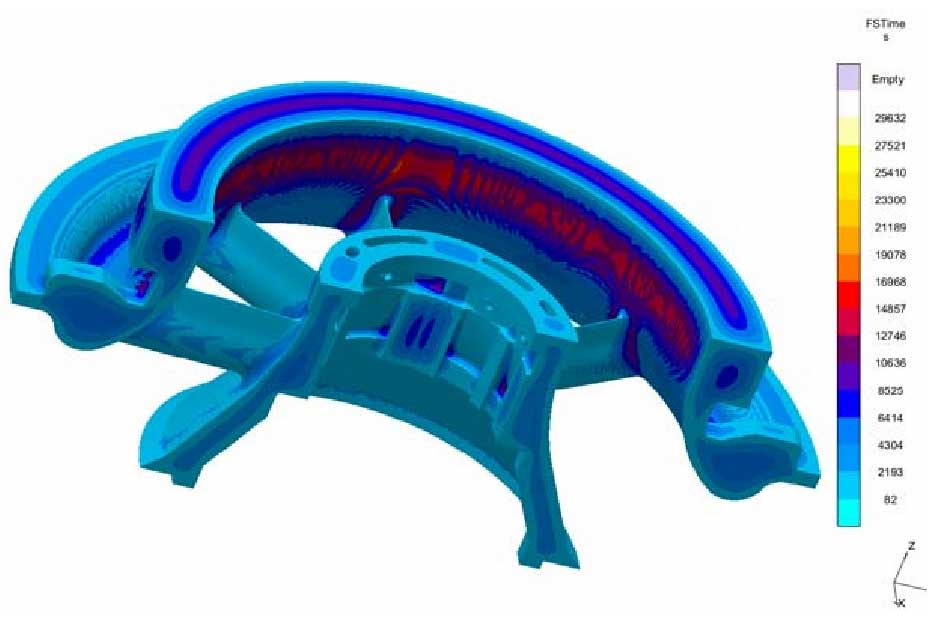
To sum up, there are several segmented isolated hot spots scattered in the pouring height direction of the intake cylinder casting. Through the sectional analysis of its structure and solidification conditions, the segmented solidification and feeding conditions can meet the quality requirements of casting body compactness. Only by ensuring that the castings meet the balanced solidification conditions on the whole and the relative sequential solidification conditions at the local positions, can the casting defects at the hot spot position be solved and prevented through the special process measures combining the two.