Before designing the mold process, the natural properties of the parts should be analyzed, including weight, volume, surface area, number and location of hot spots. The number and location of hot spots are the key factors affecting the solidification sequence of castings. The location of hot spots can be regarded as the final solidification area of castings, that is, the high incidence area of shrinkage porosity defects. According to different positions, hot spot can be divided into open hot spot and isolated hot spot. Open hot spot is hot spot on parting surface of casting, which can be fed by arranging risers. Isolated hot spot is isolated area far away from parting surface of casting and adjacent with smaller characteristic wall thickness, which is difficult to pass through Feeding through the gating system is often the final location of shrinkage porosity.
In order to quantify the size of hot spot area, the concept of modulus is introduced. The casting being cooled transfers heat content to its surrounding environment through its surface, which means that the more heat content, the slower the cooling rate. The volume of the casting can better reflect the heat content, and the surface area of the casting can better reflect the heat dissipation rate.
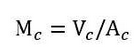
It can reflect the cooling speed of casting. A casting can be divided into several simple shapes, so that the module of the casting can be easily calculated by combining the modules of several simple shapes. Generally, the modulus at the largest hot spot of the casting can be regarded as the module of the whole casting.
The relationship between cooling time and casting modulus can be expressed as the following equation:
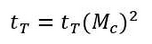
T γ is the cooling time, usually in time, up to a certain cooling temperature T, usually in ℃. K γ is a dimensionless constant, which depends on pouring temperature, cooling temperature, mold material, composition and unit. MC is the modulus of the casting, usually in cm.
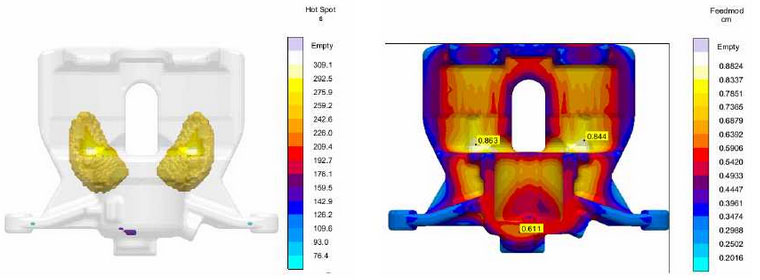