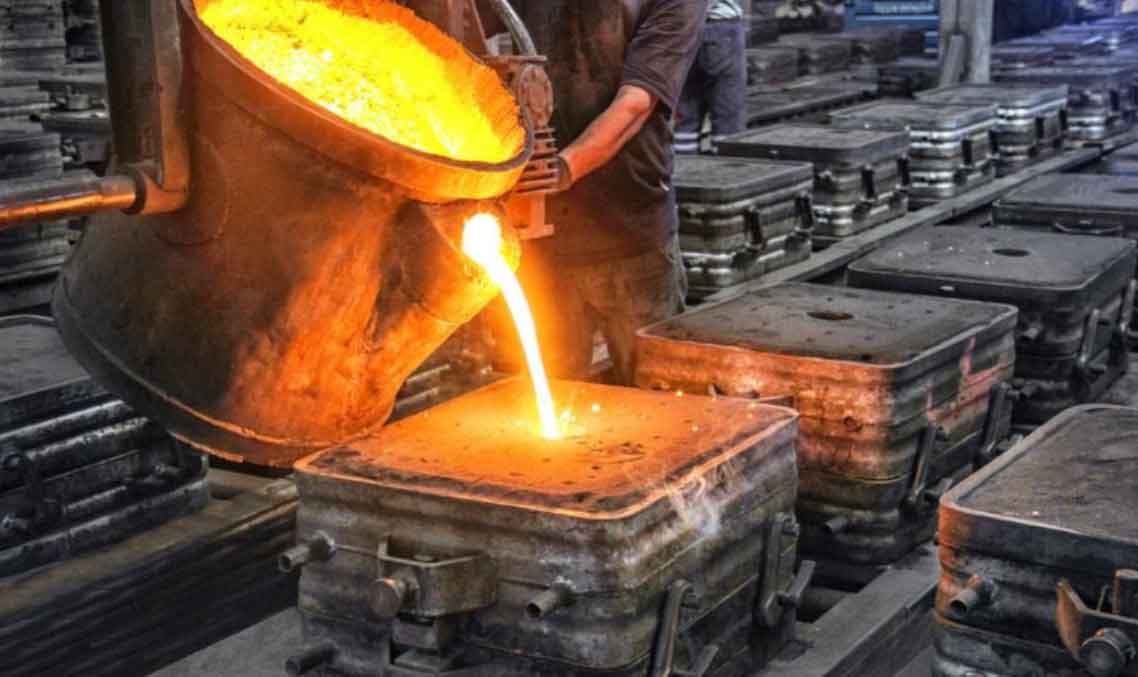
Sand casting manufacturers have been increasingly embracing eco-friendly solutions to reduce their environmental impact and promote sustainable practices. These solutions focus on resource conservation, waste reduction, energy efficiency, and the use of greener materials. Here are some ways in which sand casting manufacturers adopt eco-friendly solutions:
1. Recycling and Reclamation of Sand:
Sand casting manufacturers implement sand reclamation systems to recycle and reuse sand from the casting process. This reduces the need for new sand and minimizes the environmental impact of sand mining. Reclaimed sand is rejuvenated, ensuring its quality is suitable for future casting use.
2. Water-Based Resins:
Some manufacturers have shifted from using solvent-based resins to water-based resins for making sand molds. Water-based resins release fewer harmful emissions during the casting process, contributing to better air quality and a safer working environment.
3. Sustainable Energy Sources:
Manufacturers are exploring the use of renewable energy sources, such as solar and wind power, to reduce the carbon footprint of their operations. Utilizing sustainable energy helps decrease greenhouse gas emissions associated with the casting process.
4. Waste Reduction and Recycling:
Efforts are made to minimize waste generation during the casting process. Waste materials, such as gating systems and excess metal, are recycled and repurposed to reduce the amount of material sent to landfills.
5. Green Sand Additives:
Environmentally friendly sand additives, such as organic or bio-based binders, are being adopted as alternatives to traditional binders. These additives have a lower environmental impact and can be more easily removed during sand reclamation.
6. Energy-Efficient Melting Techniques:
Some manufacturers employ energy-efficient melting techniques, like induction melting or electric arc melting, to reduce energy consumption and greenhouse gas emissions during metal melting.
7. Casting Simulation for Efficiency:
By using advanced casting simulation software, manufacturers can optimize the casting process to minimize material waste and reduce the number of trial castings. This results in more efficient resource utilization.
8. Lean Manufacturing Practices:
Implementing lean manufacturing principles helps reduce inefficiencies and waste in the production process. By streamlining operations and minimizing non-value-added activities, manufacturers can achieve eco-friendly outcomes.
9. Environmental Certifications:
Sand casting manufacturers may seek environmental certifications, such as ISO 14001, to demonstrate their commitment to sustainable practices and compliance with environmental regulations.
10. Education and Training:
Training and educating employees about eco-friendly practices and the importance of sustainability foster a culture of environmental responsibility within the company.
Embracing eco-friendly solutions in sand casting not only benefits the environment but also enhances the reputation of manufacturers as responsible and sustainable partners. By adopting these practices, sand casting manufacturers can contribute to a greener and more sustainable future for the metal casting industry.