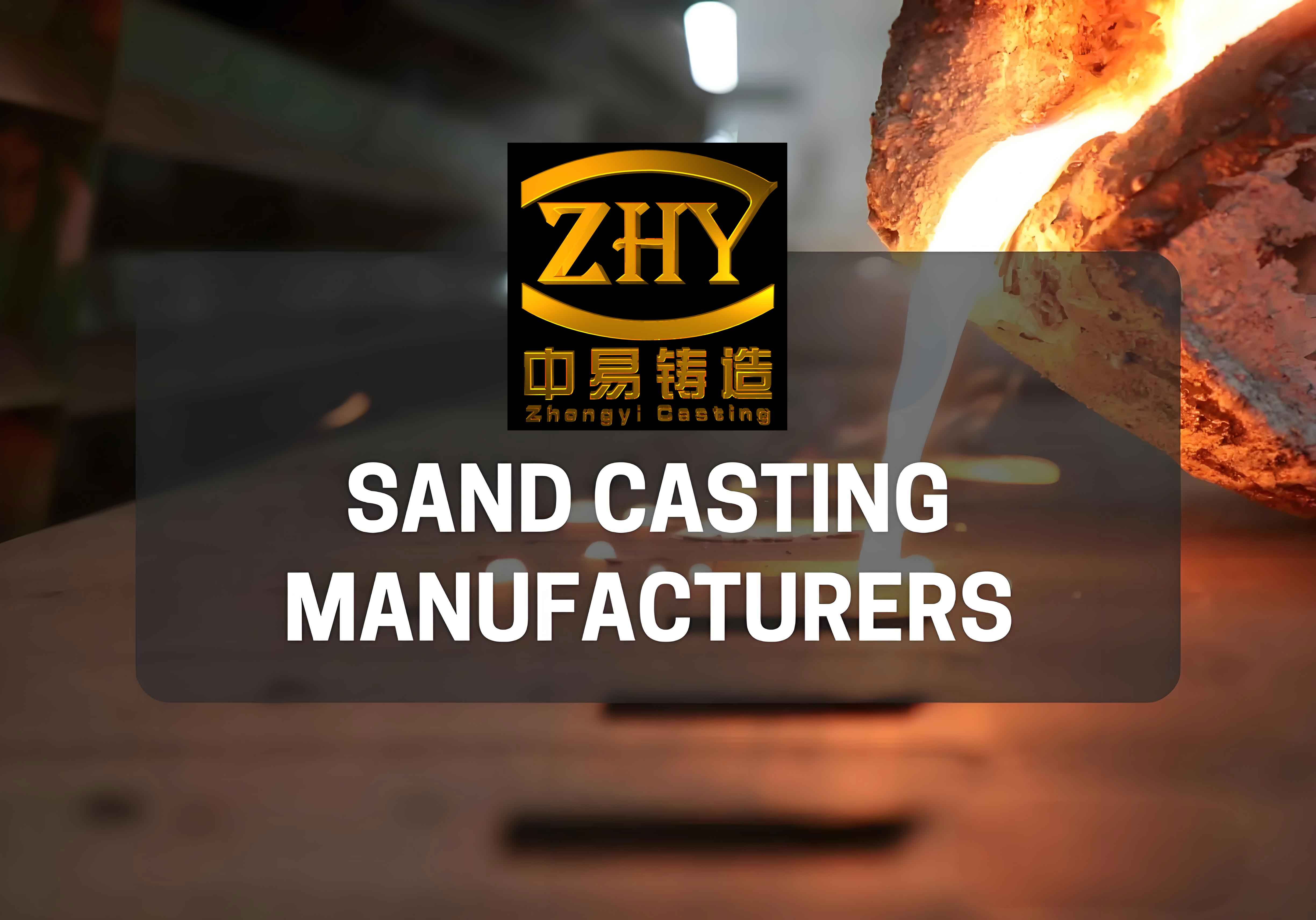
Sand Casting is fundamental and widely used method in the metal casting industry, known for its versatility and cost-effectiveness. However, ensuring precision and durability in Sand Casting Parts is crucial for meeting the stringent requirements of various industries, such as automotive, aerospace, and industrial machinery. Sand casting manufacturers employ a range of techniques and best practices to achieve high levels of precision and durability in their castings. This article explores these methods in detail.
Key Factors Influencing Precision and Durability
Precision and durability in Sand Casting Parts depend on several factors, including the quality of materials, mold design, process control, and finishing techniques. Sand casting manufacturers focus on optimizing each of these factors to produce high-quality castings.
Quality of Materials
The selection of high-quality materials is the foundation for producing precise and durable Sand Casting Parts. This includes choosing the right type of sand, binders, and metals.
Types of Sand and Binders
- Silica Sand: Commonly used due to its availability and cost-effectiveness.
- Zircon Sand: Preferred for its superior thermal stability and finer grain size, resulting in better surface finish and precision.
- Chromite Sand: Offers excellent thermal conductivity and high temperature resistance, suitable for complex castings.
Metal Selection
- Aluminum Alloys: Lightweight, corrosion-resistant, and ideal for automotive and aerospace applications.
- Iron and Steel Alloys: Known for their strength and durability, suitable for heavy-duty industrial components.
- Copper Alloys: Provide excellent thermal and electrical conductivity, used in electrical and plumbing applications.
Table 1: Comparison of Sand Types
Sand Type | Thermal Stability | Grain Size | Surface Finish Quality | Cost |
---|---|---|---|---|
Silica Sand | Moderate | Coarse | Moderate | Low |
Zircon Sand | High | Fine | High | High |
Chromite Sand | Very High | Medium | High | Moderate |
Optimizing Mold Design
Mold design plays a critical role in ensuring the precision and durability of Sand Casting Parts. Sand casting manufacturers use advanced techniques and software to design molds that minimize defects and ensure accurate dimensions.
Mold Design Considerations
- Gating System: A well-designed gating system ensures smooth metal flow, reducing turbulence and preventing defects.
- Vent Placement: Adequate venting allows gases to escape, preventing porosity and improving surface finish.
- Core Placement: Proper core placement ensures accurate internal geometries and reduces the risk of core shift.
List 1: Mold Design Best Practices
- Design efficient gating systems.
- Ensure adequate vent placement.
- Optimize core placement for accuracy.
Process Control
Controlling the casting process is essential for achieving high precision and durability. Sand casting manufacturers monitor and adjust various parameters to maintain consistency and quality.
Key Process Parameters
- Pouring Temperature: Maintaining the correct pouring temperature ensures proper metal flow and reduces the risk of cold shuts and misruns.
- Pouring Rate: Controlling the pouring rate minimizes turbulence and air entrapment, leading to better surface finish and fewer defects.
- Cooling Rate: Implementing controlled cooling prevents thermal stresses and enhances the mechanical properties of the casting.
Table 2: Key Process Parameters for Precision and Durability
Parameter | Impact on Precision | Impact on Durability |
---|---|---|
Pouring Temperature | Ensures proper metal flow | Reduces risk of defects |
Pouring Rate | Minimizes turbulence | Prevents air entrapment |
Cooling Rate | Prevents thermal stresses | Enhances mechanical properties |
Inspection and Quality Control
Rigorous inspection and quality control are vital for ensuring the precision and durability of Sand Casting Parts. Sand casting manufacturers employ various testing methods to detect defects and verify dimensional accuracy.
Inspection Techniques
- Visual Inspection: Checking the surface for visible defects such as cracks, porosity, and inclusions.
- Dimensional Inspection: Using tools like calipers and coordinate measuring machines (CMM) to verify dimensions.
- Non-Destructive Testing (NDT): Techniques such as X-ray, ultrasonic, and magnetic particle testing to detect internal defects without damaging the casting.
List 2: Common Inspection Techniques
- Visual inspection for surface defects.
- Dimensional inspection using CMM.
- Non-destructive testing (NDT) for internal defects.
Enhancing Durability Through Heat Treatment
Heat treatment processes are used to enhance the mechanical properties and durability of Sand Casting Parts. Sand casting manufacturers apply various heat treatment techniques based on the type of metal and the desired properties.
Heat Treatment Techniques
- Annealing: Reduces internal stresses and improves ductility.
- Quenching: Increases hardness and strength by rapidly cooling the casting in water or oil.
- Tempering: Reduces brittleness and enhances toughness by reheating the quenched casting to a specific temperature.
Table 3: Heat Treatment Techniques and Their Benefits
Technique | Process Description | Benefits |
---|---|---|
Annealing | Slow cooling after heating | Reduces internal stresses, improves ductility |
Quenching | Rapid cooling in water or oil | Increases hardness and strength |
Tempering | Reheating quenched casting | Reduces brittleness, enhances toughness |
Post-Processing and Finishing
Post-processing and finishing are crucial steps to improve the precision and durability of Sand Casting Parts. Sand casting manufacturers use various techniques to remove surface imperfections and enhance the overall quality of the castings.
Common Post-Processing Techniques
- Shot Blasting: Uses abrasive particles to clean the surface and remove any residual sand.
- Grinding and Polishing: Removes surface imperfections and achieves a smooth finish.
- Machining: Ensures precise dimensions and tight tolerances by removing excess material.
List 3: Post-Processing Techniques
- Shot blasting for surface cleaning.
- Grinding and polishing for smooth finish.
- Machining for precise dimensions.
Case Study: Improving Precision and Durability in Automotive Sand Casting Parts
An automotive parts manufacturer faced challenges in achieving the required precision and durability for their Sand Casting Parts. The following table outlines the steps taken to address these challenges and the results achieved.
Table 4: Case Study – Steps to Improve Precision and Durability
Step | Action Taken | Result |
---|---|---|
Material Selection | Switched to high-quality zircon sand and aluminum alloy | Improved surface finish and mechanical properties |
Mold Design Optimization | Redesigned gating and venting systems | Reduced defects and improved dimensional accuracy |
Process Control | Maintained optimal pouring temperature and rate | Minimized defects and enhanced durability |
Heat Treatment | Applied quenching and tempering processes | Increased strength and toughness |
Post-Processing | Implemented shot blasting and machining | Achieved smooth finish and precise dimensions |
Conclusion
Ensuring precision and durability in Sand Casting Parts is a multifaceted process that requires attention to material quality, mold design, process control, and finishing techniques. Sand casting manufacturers employ a range of best practices and advanced techniques to produce high-quality castings that meet the demanding requirements of various industries. Through continuous improvement and rigorous quality control, manufacturers can achieve the desired balance of precision and durability in their Sand Casting Parts, ensuring better performance and customer satisfaction.