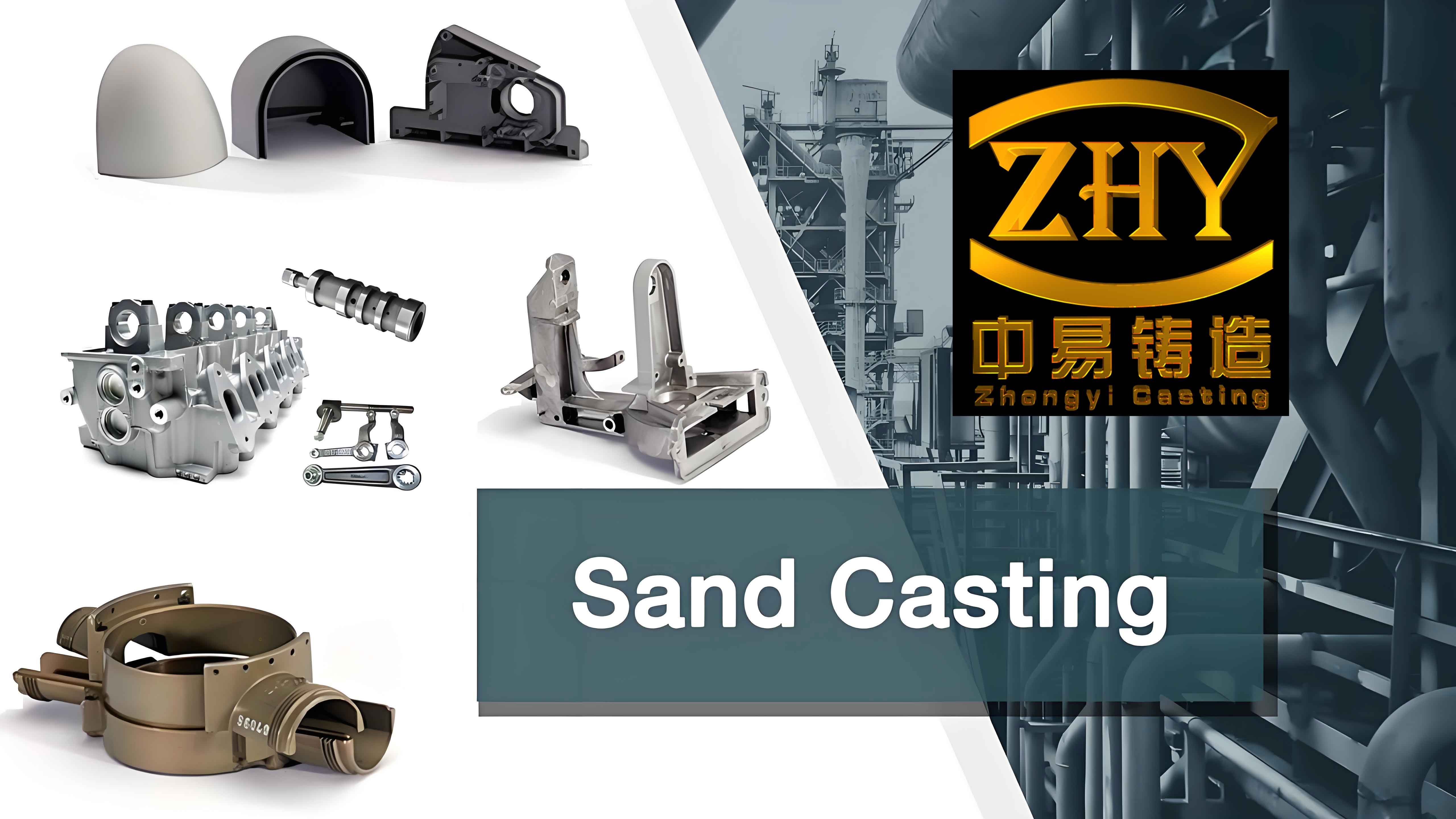
Sand casting manufacturing is versatile and cost-effective process used to produce complex metal parts. However, the costs associated with sand casting manufacturing can be significant due to the various stages involved, from design and mold preparation to casting and finishing. Implementing effective cost reduction strategies can enhance the overall efficiency and profitability of sand casting manufacturing operations. This article explores several cost reduction strategies that can be applied in sand casting manufacturing, highlighting their benefits and practical implementation.
Cost Reduction Strategies in Sand Casting Manufacturing
- Optimized Design and Engineering
- Design for Manufacturability (DFM): Adopting DFM principles ensures that the design of sand casting parts is optimized for the manufacturing process. This includes simplifying complex geometries, reducing the number of cores, and minimizing material usage without compromising the functionality of the parts.
- Computer-Aided Design (CAD): Utilizing CAD software allows for precise and efficient design iterations, reducing the need for costly and time-consuming physical prototypes.
- Material Efficiency
- Alloy Selection: Choosing cost-effective alloys that meet the required mechanical properties can significantly reduce material costs. Conducting thorough material analysis can identify the most suitable and economical alloys for specific sand casting parts.
- Scrap Reduction: Implementing stringent quality control measures and optimizing the casting process can minimize scrap rates. Reusing and recycling scrap material within the foundry can further reduce material costs.
- Improved Mold and Core Production
- High-Quality Sand: Using high-quality sand in the mold and core production can improve the surface finish and dimensional accuracy of the sand casting parts, reducing the need for extensive post-casting machining and finishing operations.
- Advanced Binder Systems: Utilizing advanced binder systems can enhance the strength and stability of the molds and cores, reducing the likelihood of defects and rework.
- Energy Efficiency
- Optimized Melting Practices: Implementing energy-efficient melting practices, such as optimizing furnace operation and using energy-efficient melting equipment, can significantly reduce energy consumption and costs.
- Heat Recovery Systems: Installing heat recovery systems can capture and reuse waste heat from the casting process, reducing overall energy consumption.
- Automation and Process Control
- Automated Sand Casting Manufacturing: Implementing automation in sand casting manufacturing, such as automated mold handling and pouring systems, can increase productivity, reduce labor costs, and improve consistency and quality.
- Real-Time Process Monitoring: Utilizing real-time process monitoring systems can detect and address issues promptly, minimizing downtime and reducing the costs associated with defects and rework.
Tables and Lists for Clarity
Table 1: Cost Reduction Strategies and Their Benefits
Strategy | Benefits |
---|---|
Design for Manufacturability | Simplifies production, reduces material usage, minimizes rework |
Computer-Aided Design | Efficient design iterations, reduces need for physical prototypes |
Alloy Selection | Identifies cost-effective materials, ensures required mechanical properties |
Scrap Reduction | Minimizes waste, reuses material, reduces material costs |
High-Quality Sand | Improves surface finish, reduces post-casting operations |
Advanced Binder Systems | Enhances mold and core stability, reduces defects and rework |
Optimized Melting Practices | Reduces energy consumption and costs |
Heat Recovery Systems | Captures and reuses waste heat, reduces overall energy consumption |
Automated Manufacturing | Increases productivity, reduces labor costs, improves quality |
Real-Time Process Monitoring | Detects issues promptly, minimizes downtime, reduces defect costs |
Table 2: Key Areas for Material Efficiency in Sand Casting Manufacturing
Area | Description |
---|---|
Alloy Selection | Choosing economical alloys with necessary properties |
Scrap Reduction | Minimizing waste and reusing material within the foundry |
Quality Control | Implementing stringent measures to reduce defects and scrap |
Process Optimization | Enhancing casting process to improve material utilization |
List: Steps for Implementing Cost Reduction Strategies in Sand Casting Manufacturing
- Design Optimization
- Apply Design for Manufacturability principles.
- Utilize CAD software for efficient design iterations.
- Material Efficiency
- Conduct material analysis to identify cost-effective alloys.
- Implement scrap reduction measures and recycle material within the foundry.
- Mold and Core Production
- Use high-quality sand for molds and cores.
- Adopt advanced binder systems to enhance mold and core stability.
- Energy Efficiency
- Optimize melting practices to reduce energy consumption.
- Install heat recovery systems to capture and reuse waste heat.
- Automation and Process Control
- Implement automation in sand casting manufacturing processes.
- Utilize real-time process monitoring to detect and address issues promptly.
Conclusion
Cost reduction in sand casting manufacturing is essential for enhancing the competitiveness and profitability of the foundry. By optimizing design and engineering processes, improving material efficiency, enhancing mold and core production, adopting energy-efficient practices, and leveraging automation and process control, manufacturers can achieve significant cost savings. These strategies not only reduce costs but also improve the overall quality and consistency of sand casting parts. Implementing these cost reduction strategies requires a combination of technological advancements, process improvements, and a commitment to continuous improvement in sand casting manufacturing operations.