1.Horizontal and vertical pouring process plan
The horizontal and vertical pouring process scheme is shown in Figure 1 (a). The scheme adopts the bottom pouring system, the inner runner is circular, and the water enters through the skin seam of the core head. The advantages are that the impeller casting is filled smoothly, the exhaust and slag removal effects are good, the high pressure feeding effect of the impeller casting head is good, and the top riser feeding is available during the solidification shrinkage, and the quality stability of the impeller casting is high. At present, most foundries use this process scheme for impeller production.
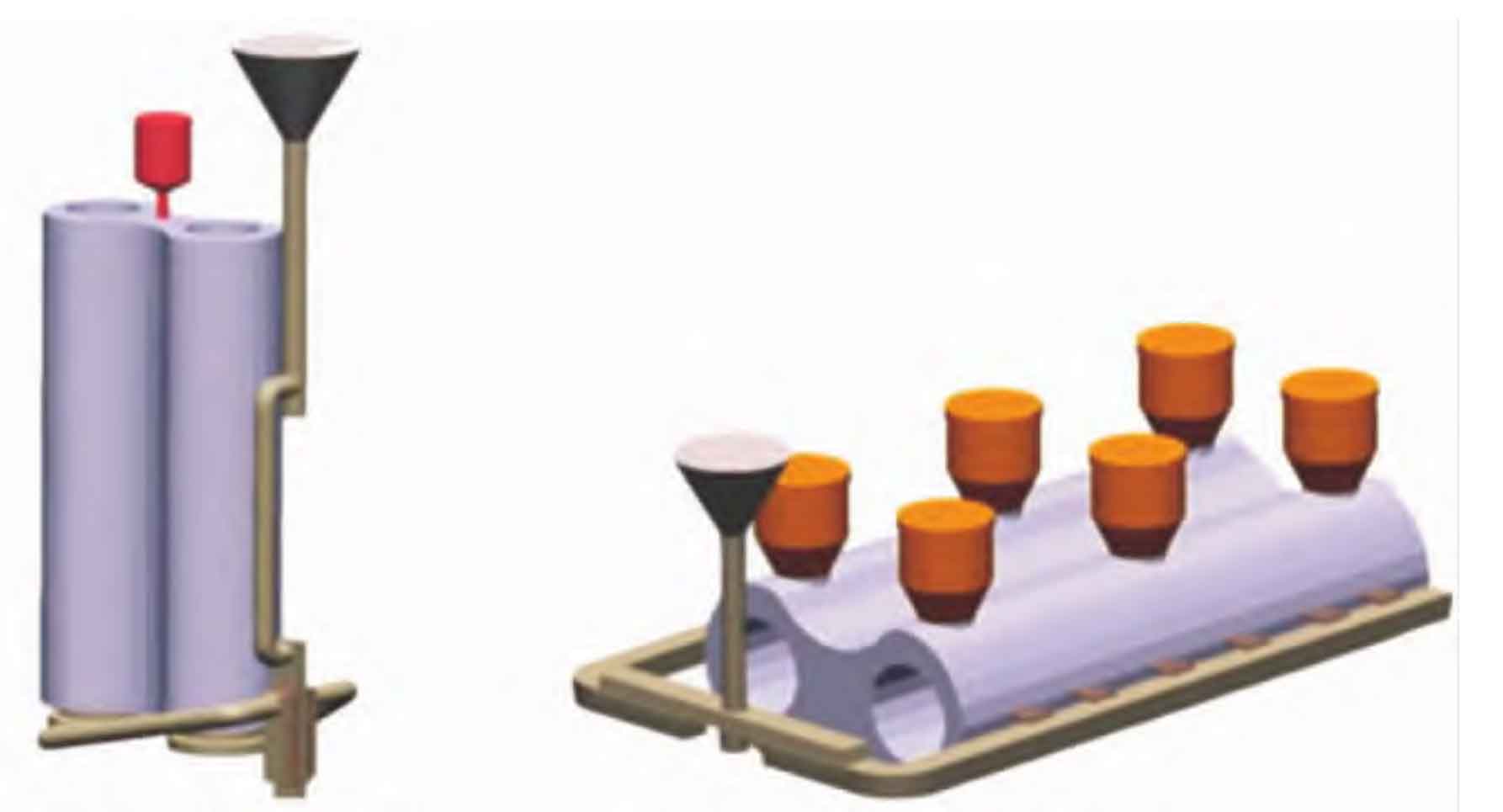
Although the process plan is conducive to ensuring product quality, it is difficult to close the box in actual production, which is easy to cause the problem of wrong box. It needs to put in a special sand box at one time, and the production cost is high; At the same time, due to the high static head of the vertical casting process, the expansion force of the impeller casting in the process of graphitization expansion is large, which often causes the problem of fire escape during the casting.
2.Horizontal casting process plan
The horizontal casting process plan is shown in Figure 1 (b). This plan is a mid-pouring pouring system. The inner runner enters water from multiple points on the parting surface. This plan is convenient for box closing operation, low probability of fire escape during casting pouring, and no need to put in a special sand box. It has the advantages of low production cost and high production efficiency. Although the horizontal casting process is convenient for production, it is easy to cause slag inclusion on the top surface of the casting when the large plane of the casting is upward. Although the riser can play the role of feeding in the process plan, due to the uneven wall thickness of the casting structure and other characteristics, the problem of shrinkage porosity can not be completely solved by the riser alone at local locations.
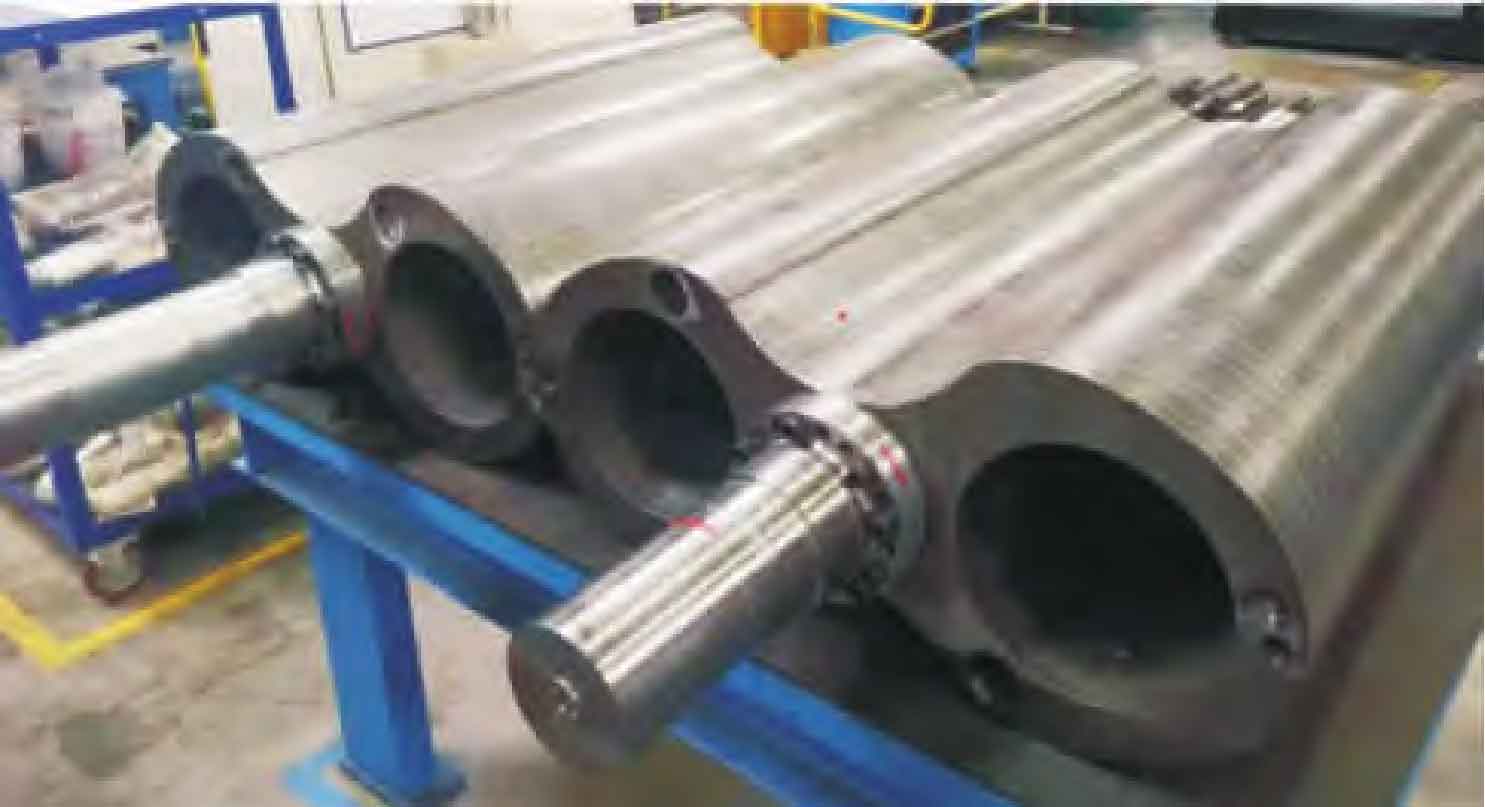
The optimized process validation was adopted, and a total of 3 batches of “1+2+4” experiments were carried out. MT and UT flaw detection were carried out on the test pieces, which met the customer’s technical requirements. The casting appearance after the processing of the test piece has no casting defects, and the delivery of the sample piece has been successfully completed. At present, the process has been tested for batch production, and the finished castings are as shown in Figure 2.