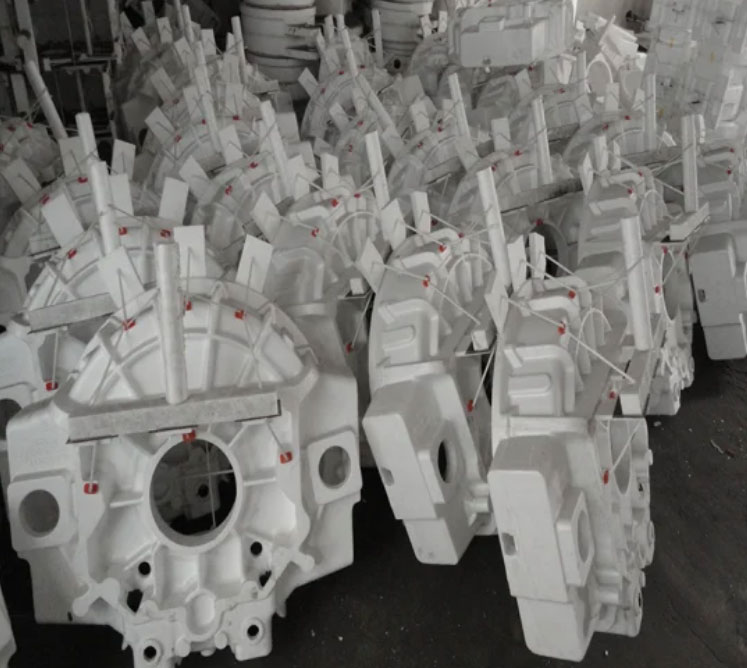
Lost foam casting (LFC) is a complex process, and like any manufacturing method, it can encounter certain issues that may affect casting quality and production efficiency. Troubleshooting these common issues is crucial to maintaining a successful lost foam casting operation. Here are some common problems encountered in LFC and their potential solutions:
1. Pattern Distortion or Collapse:
Issue: The foam pattern may distort or collapse during handling or assembly, leading to inaccuracies in the final casting.
Potential Solutions:
- Use higher density or more rigid foam materials to improve pattern stability.
- Implement proper handling and storage practices to prevent physical damage to the foam patterns.
- Optimize the assembly process to ensure proper alignment and support of the foam patterns within the mold.
2. Mold Fill Issues:
Issue: Inadequate filling of the mold with molten metal can lead to incomplete castings or defects.
Potential Solutions:
- Improve gating and risering design to ensure proper metal flow into the mold cavity.
- Adjust pouring parameters, such as pouring rate and temperature, to optimize mold fill.
- Use computational fluid dynamics (CFD) simulations to identify and rectify flow-related issues.
3. Mold Erosion or Breakdown:
Issue: The refractory coating on the foam pattern may erode or break down prematurely, affecting surface finish and casting integrity.
Potential Solutions:
- Optimize the refractory coating mixture to enhance its adhesion and resistance to erosion.
- Ensure proper drying and curing of the refractory coating before casting.
- Consider using a backup coating or secondary coating layer to enhance durability.
4. Inadequate Casting Cooling:
Issue: Inefficient cooling of the casting may lead to shrinkage defects or internal stresses.
Potential Solutions:
- Optimize the design of internal cooling passages within the casting to ensure uniform cooling.
- Consider using metal chills or inserts to enhance cooling rates in critical areas.
- Control the cooling rate by adjusting the mold temperature or utilizing insulating materials.
5. Surface Defects:
Issue: Surface defects, such as pinholes, gas porosity, or sand inclusions, can mar the final casting’s appearance and affect mechanical properties.
Potential Solutions:
- Ensure proper venting and degassing to minimize gas-related defects.
- Improve the refractory coating quality to reduce the risk of surface defects.
- Maintain cleanliness in the foundry environment to prevent sand or other contaminants from entering the mold cavity.
6. Dimensional Inaccuracy:
Issue: Deviations from the desired dimensions can occur due to pattern deformation, mold expansion, or metal solidification.
Potential Solutions:
- Use high-precision foam patterns and molds to ensure accurate dimensions.
- Incorporate allowances for pattern and mold expansion in the design phase.
- Control the solidification rate of the metal to minimize dimensional changes.
7. Foam Pattern Vaporization Issues:
Issue: Incomplete or uneven vaporization of the foam pattern may lead to casting defects or internal voids.
Potential Solutions:
- Optimize the foam pattern density and structure to ensure uniform vaporization.
- Ensure proper and consistent burnout of the foam pattern during casting.
- Monitor the vaporization process to identify any issues and adjust parameters as needed.
8. Sand Compaction and Mold Strength:
Issue: Inadequate sand compaction or weak molds can result in mold collapse during casting.
Potential Solutions:
- Control sand compaction through proper vibration techniques or use of compaction machines.
- Improve mold rigidity by using stronger binders or reinforcements.
- Ensure proper drying and curing of the sand mold to achieve the desired strength.
Successful lost foam casting requires careful attention to the entire process, from pattern production to metal pouring. Troubleshooting common issues involves a combination of material selection, process optimization, and advanced simulations to identify and rectify potential problems. Regular quality control measures, continuous process improvement, and adherence to best practices play a vital role in ensuring consistent and high-quality castings in the lost foam casting process.