The impeller is the core component of the fan. It is assembled on the cylinder block to do work through continuous rotation, which requires the impeller to meet the characteristics of high strength and high temperature resistance in terms of material. Because it is a power component, it needs to do dynamic balance test, and in terms of structure, it requires the symmetrical wall thickness of the impeller casting to be uniform. The impeller is a thick and large ductile iron casting. The main wall thickness of the impeller casting is 25 mm, and the wall thickness of the two ends and the central rib plate is 80 mm. The wall thickness of the impeller casting is uneven, and the distribution of the hot spot is relatively complex. In addition, the entire outer contour of the impeller casting needs to be processed completely, and no casting defects are allowed, making it a difficult point in the casting process.
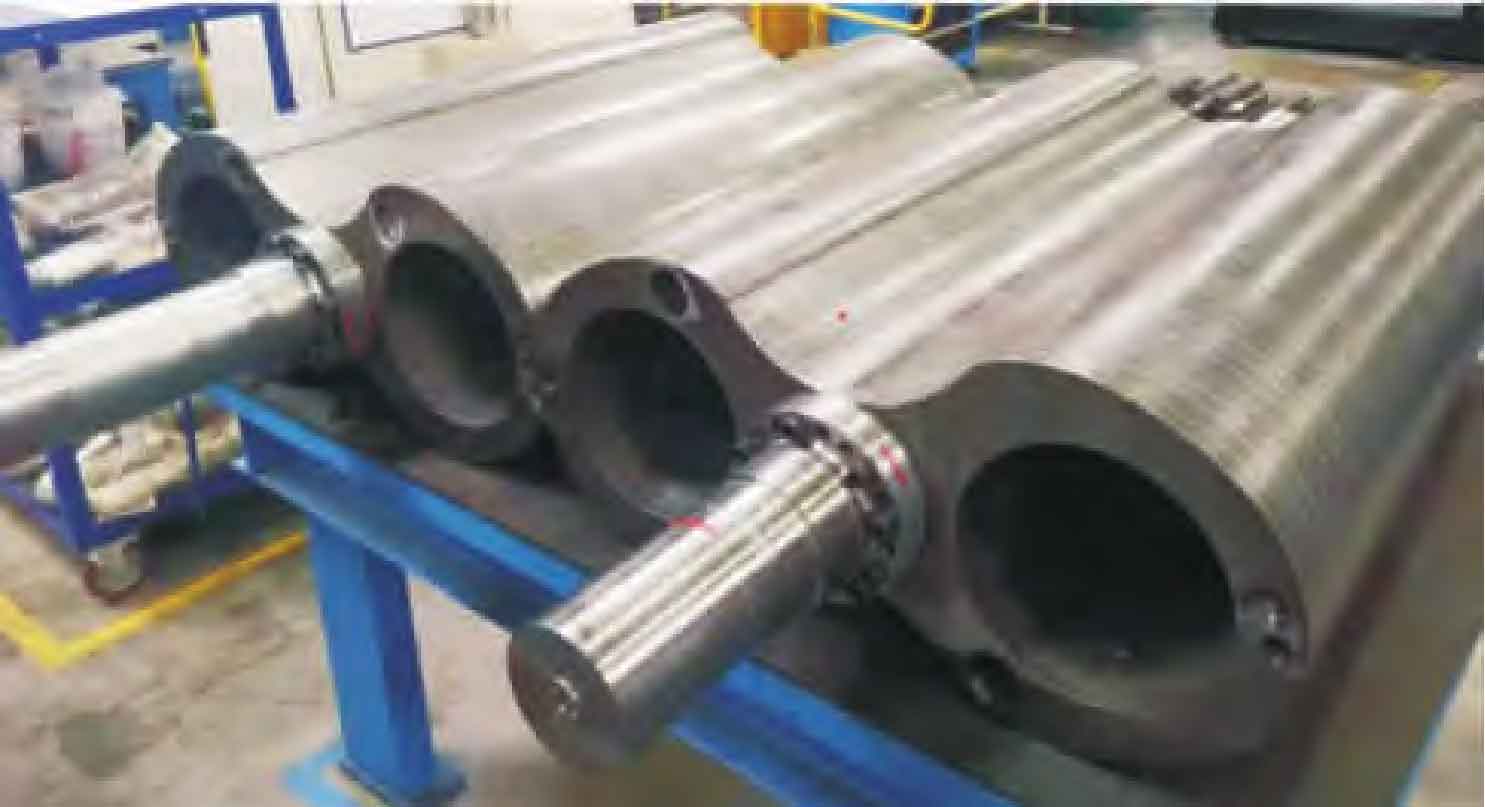
At present, domestic and foreign casting production enterprises generally adopt the horizontal and vertical casting process plan for production. This plan has stable mold filling, good exhaust and slag removal effect of impeller castings, good feeding effect of high pressure of impeller castings, and at the same time, there is top riser feeding during solidification shrinkage. The quality stability of impeller castings is high, but the production efficiency is low, the risk of fire escape of impeller castings is high, and the production cost is high. With the increasing demand for impellers, it is urgent to produce impellers with low cost and high efficiency.
(1) The optimization of the bottom pouring horizontal casting process plan of chill and riser can largely solve the problems of shrinkage porosity, slag defects, and fire escape of impeller castings.
(2) Solidification simulation can verify the shrinkage and porosity of impeller castings in theory, and reduce the waste loss in the actual production process.
(3) The single riser process plan cannot completely solve the problem of impeller shrinkage and porosity, so it is necessary to combine the cold iron process plan.
(4) To solve the problem of impeller inclusion, it is necessary to control the purity of molten iron and the cleanliness of the cavity from many aspects.
The innovative horizontal casting scheme has greatly solved the problems of high production cost, low production efficiency and fire escape of impeller castings, but it is necessary to overcome the problems of shrinkage and slag inclusion of impeller castings in the horizontal casting process scheme. In impeller casting, the large plane facing up is not conducive to impurity removal, so when selecting the casting process plan, the large plane facing up is usually avoided.
By adjusting the pouring plan, observing the influence of different processes on the casting defects of the impeller, and breaking through the traditional process plan, starting from the source of the inclusions, by controlling the purity of the molten iron and the cleanliness of the mold cavity, the generation of the inclusions can be reduced as much as possible to achieve the goal of solving the large plane inclusions.