Titanium alloys have high chemical activity in the molten state, and react with almost all oxide refractories. Therefore, in the process test, zirconia with high chemical stability is selected as the surface material of investment casting shell, zirconium diacetate binder is selected as the binder, bauxite and silica sol slurry are used as the backing material, and mullite sand is used for shell coating.
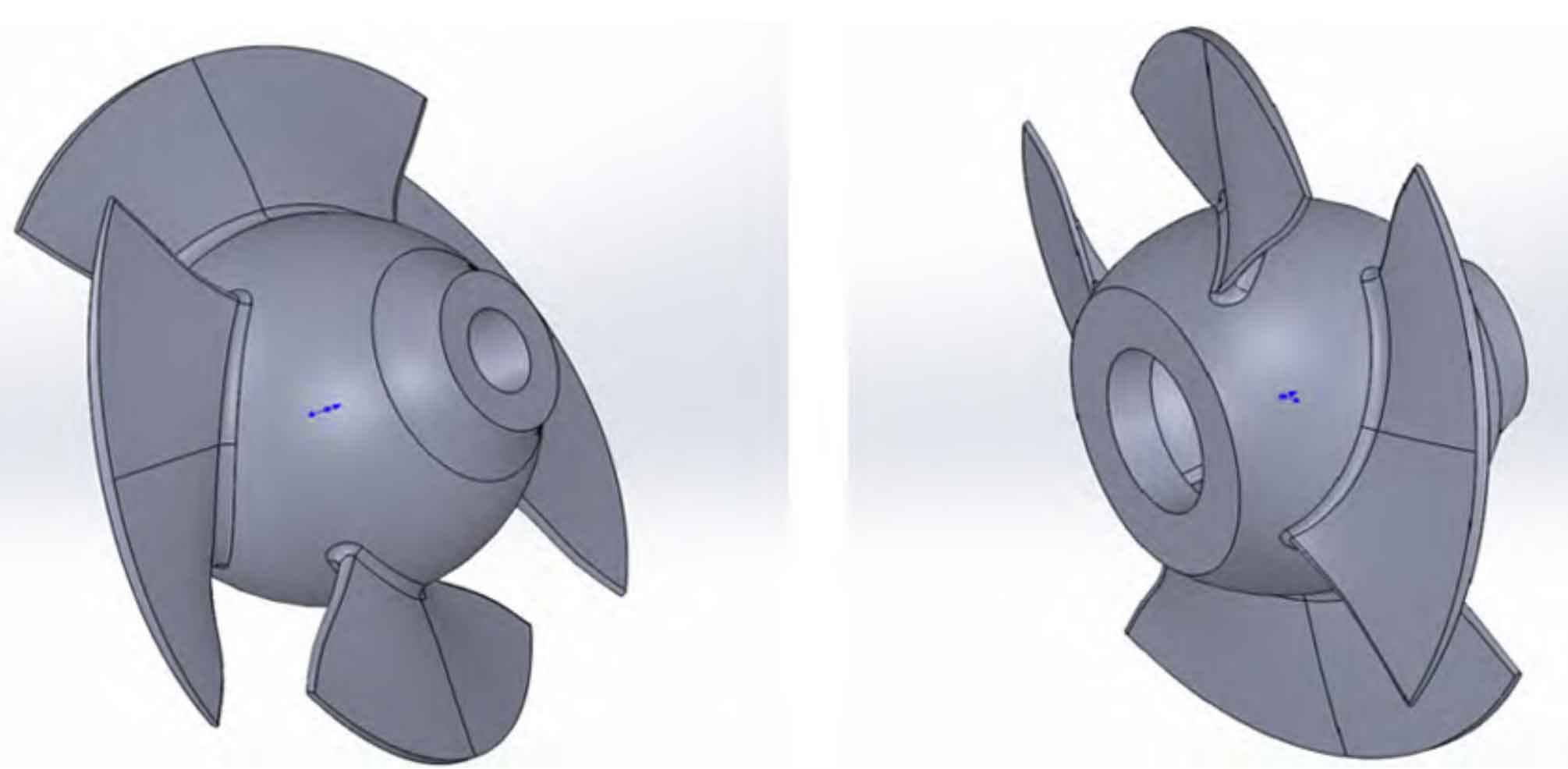
The mold shell is dewaxed with hot water after drying, and then roasted in a box-type resistance furnace. The roasting temperature is 900~950 ℃, and the temperature is kept for 2~2.5h under the condition of reducing atmosphere, so that the binder can be fully carbonized, and the residual slurry can be removed, so that the mold shell has good strength and permeability. After baking, the shell shall be inspected and trimmed.
The refined shell is degassed in the vacuum degassing furnace, with heating temperature of 950~1000 ℃ and vacuum degree ≤ 5 × 10-2 Pa, holding time 2~2.5 h, further remove the residual gas and volatile matter in the mold shell. After vacuum degassing, it can be put into the vacuum consumable electrode arc shell furnace for pouring.