The wax pattern is made by 3D printing, and its linear shrinkage ratio is 1.0%~2.0%. Due to the long distance between the far end of the blade and the shrinkage center of the impeller investment casting, the solidification shrinkage ratio of the far end and the near end is different. Therefore, during wax mold manufacturing, the scale shall be designed according to the structure of the impeller investment casting in sections, that is, the scale ratio of the near end of the blade shall be set at 1.0%, and the scale ratio from the near end to the far end shall be gradually set at 1.0%~2.0%, to ensure that the actual shrinkage size of the model matches the process design size.
The linear shrinkage ratio of titanium alloy is 0.5%~0.8%. Due to the different structural characteristics and wall thickness dimensions of different parts of the impeller investment casting, the shrinkage and deformation degree of each area is also different. The shrinkage of the thick area is relatively large, the shrinkage of the small thin wall area is relatively small, the shrinkage of the area with small radius from the center is relatively large, and the shrinkage of the far end of the blade is relatively small; For the wall thickness transition zone or abrupt change zone, the section size changes greatly. During the solidification process, there is an uneven distribution of cooling speed in this region, resulting in large differences in expansion deformation at different locations in the region.
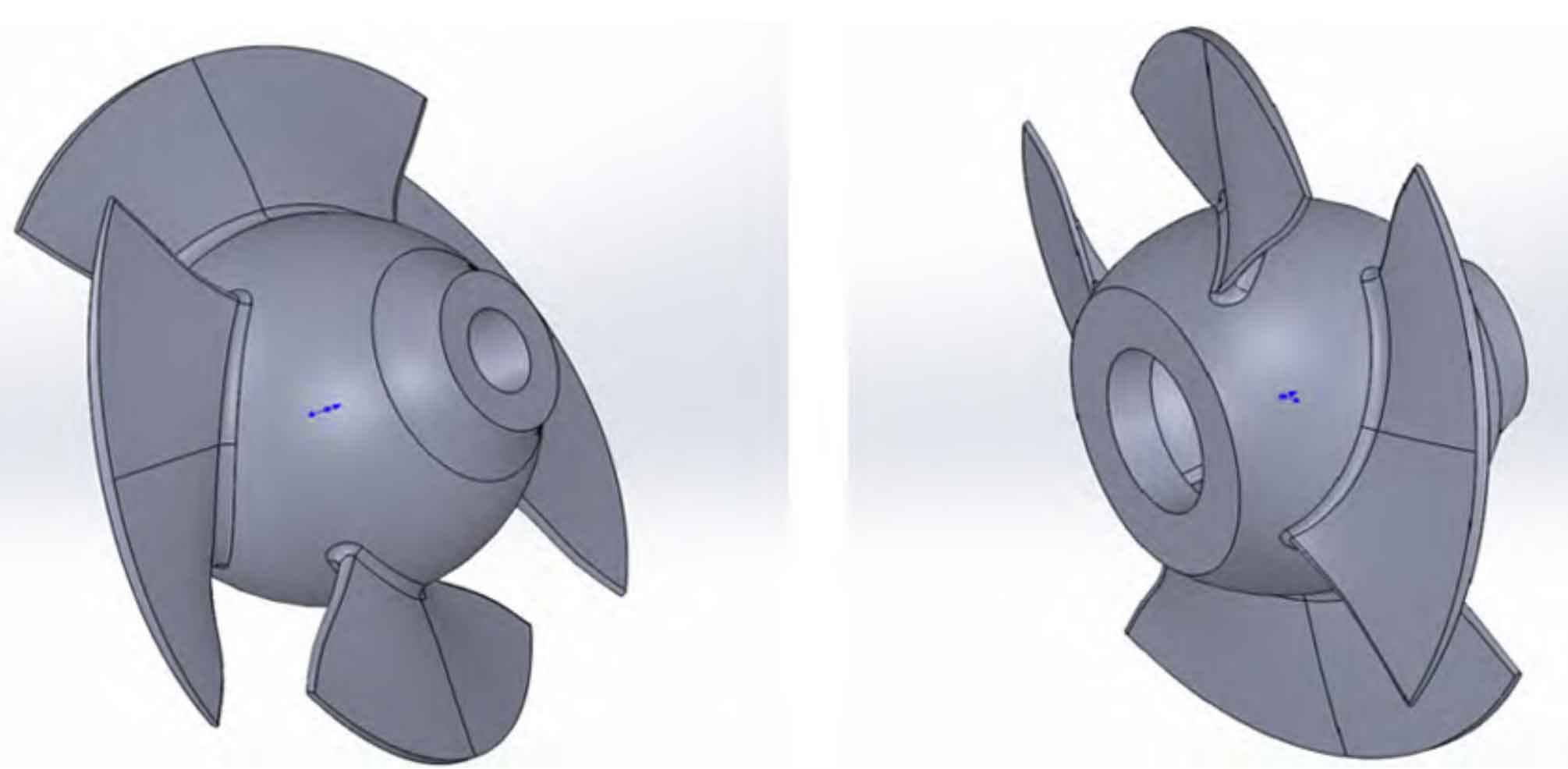
Therefore, during wax mold manufacturing, the reverse deformation process correction amount must be set according to the impeller investment casting structure in different areas, and the deformation amount consistent with the impeller investment casting deformation amount but in the opposite direction must be reserved to offset the shrinkage deformation of the impeller investment casting. That is, the correction amount at the near end of the blade is set at 0.8%, from the near end to the far end is gradually set at 0.8%~0.5%, and some thick areas are set at 1.0%. Ensure that the actual manufacturing size of the shell matches the molding size of the impeller investment casting. The wax pattern process design is shown in the figure.