Through the research of the above process plan, the design and manufacture of sand casting process for the crank of the pumping unit have been completed. The physical and chemical properties of sand mold castings produced for the first time meet the material standards. Through dimensional inspection, magnetic particle flaw detection and sectional anatomy inspection, as well as subsequent finishing and loading verification, they all meet the product use requirements. It is proved that the design of sand casting process scheme is successful and provides valuable experience for the production of similar products.
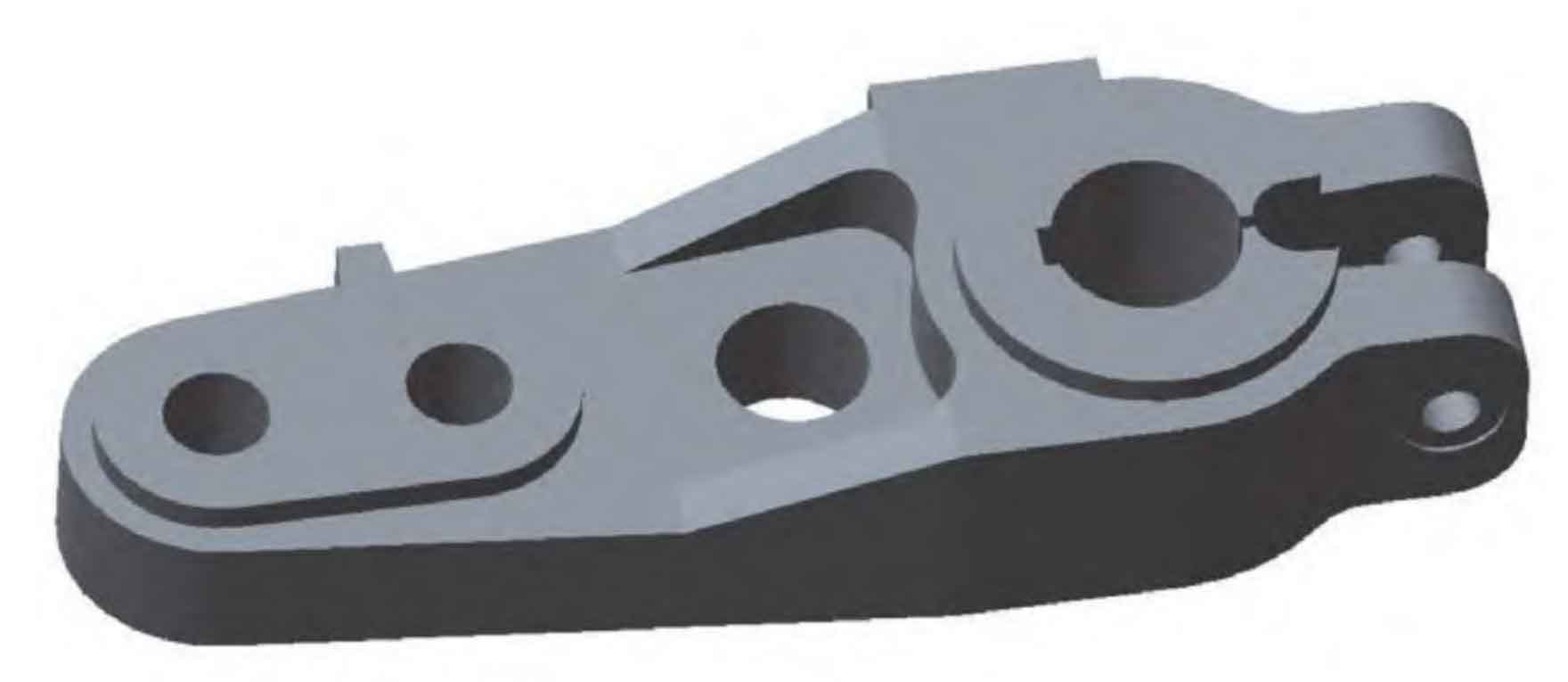
(1) The liquid steel of thick-walled plate-like parts enters from the relatively thin wall near the feeding riser to avoid the formation of excessive contact hot spots, which can reduce the tendency of the casting to form shrinkage cavities and porosity defects, and improve the process yield of sand castings.
(2) The entry of the inner runner along the shape direction of the sand casting is better than the entry of the vertical wall thickness direction, which can realize the smooth pouring of the liquid metal and effectively avoid the air entrapment of the liquid metal and the erosion of the mold wall resulting in the sand casting defects such as air holes and sand sticking.
(3) The design of sand mold casting process feeding system for thick-walled plate-shaped parts can cooperate with the use of chilled iron, chromite ore and other chilling materials to artificially interfere with the solidification speed of molten metal, create conditions for achieving sequential solidification towards the riser, and improve the feeding efficiency of the riser.
(4) The combination of mold filling simulation and solidification simulation defect prediction improves the success rate of process design.