After the casting spheroidization problem appeared, our company’s technical, quality, physical and chemical department and other departments jointly analyzed, according to the actual production, the rectification measures were determined.
1) Standardize the operation procedures and control the pouring time.
2) Adjust the blowing in sequence, the first furnace smelting gray iron, using ductile iron ladle pouring (to extend the ladle baking time).
3) The structure of spheroidizing ladle is unreasonable, the ratio of height to diameter is controlled and the original spheroidized ladle is reused.
4) Control the sulfur content of the molten iron and the usage of the recycle material.
5) There are excessive anti spheroidizing elements in molten iron, so trace elements such as lead, titanium and tin are controlled.
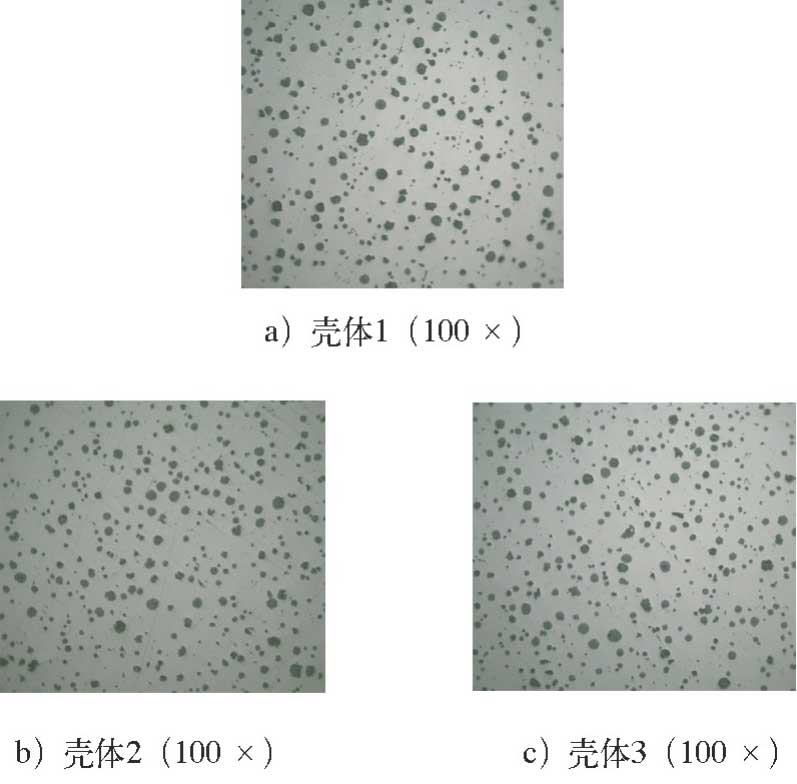
After adopting the above rectification measures, the metallographic spheroidization rate of test block and body is about 80%, which is still unqualified. At the same time, we have detected that the WS in molten iron is 0.025% – 0.026%, which is less than or equal to 0.020% specified by our factory. In order to produce high quality nodular cast iron, the sulfur content of the original molten iron is generally controlled within 0.020% in foreign countries. In winter, the content of total acid and free sulfuric acid in the curing agent for resin sand molding is higher than that in other seasons, that is, the sulfur content is higher, so the sulfur content in the recycled material will be higher if it penetrates into the surface of runner and casting. Sulfur is an anti spheroidizing element. It has a strong affinity with magnesium and reacts to form MGS, which consumes the effective magnesium content, resulting in insufficient free magnesium content in molten iron, which leads to poor spheroidization. At this time, more spheroidizing agents are needed to ensure the spheroidizing effect. Therefore, we increased the amount of spheroidizing agent from 1% to 1.1%. Through the production tracking test, the spheroidizing rate of the attached casting test block and the main body reached more than 90% (see Figure), and the poor spheroidizing phenomenon was eliminated.