The advantages and disadvantages of bottom pouring and horizontal pouring are comprehensively analyzed, and the casting process is improved by combining the advantages of the two molding processes, that is, a transverse runner is added at the edge of the mold cavity, and the mold is inclined downward, as shown in the figure.
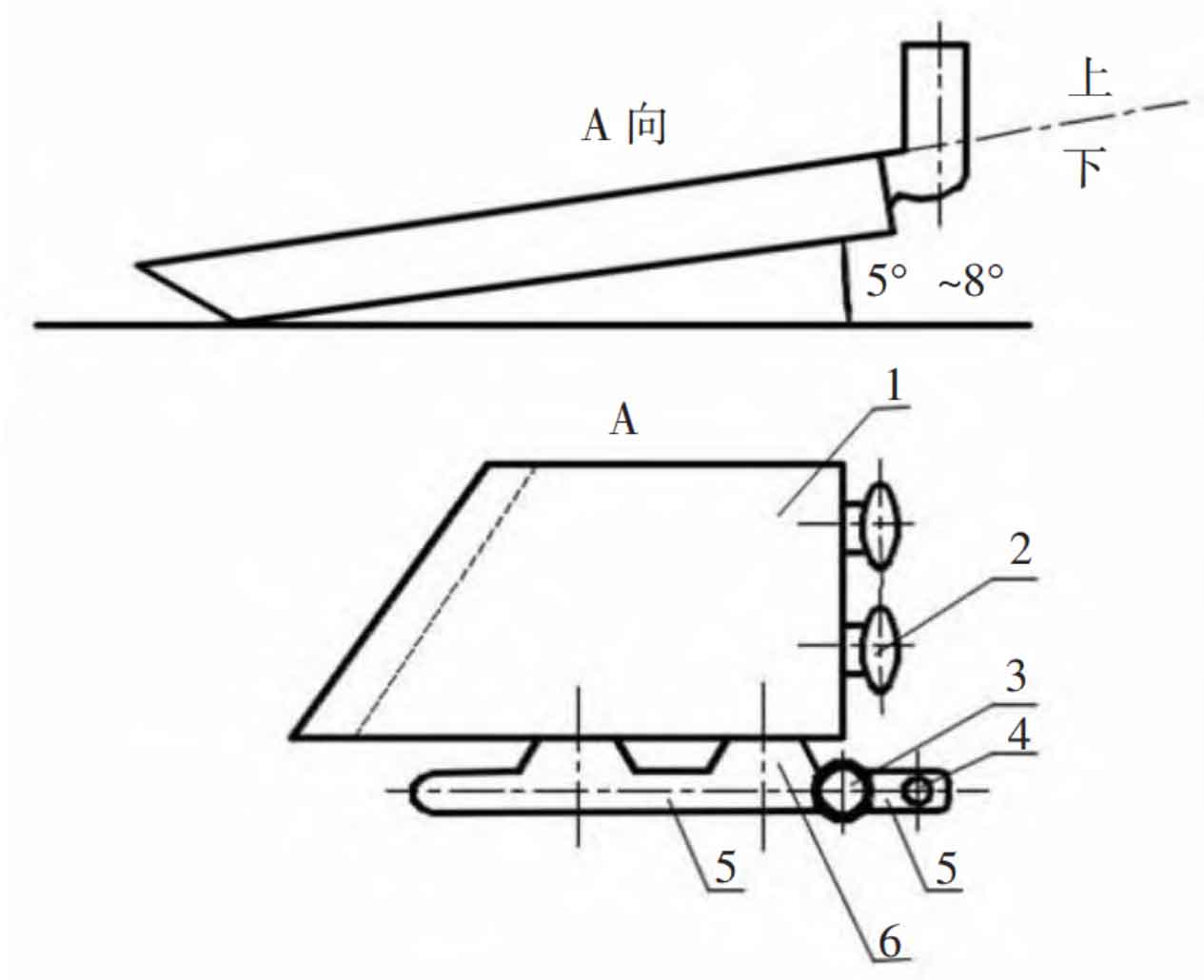
The pouring process of inclined top pouring, water inlet from the bottom, and stepped inner runner is adopted. The feeding (overflow) and exhaust riser are set at the top to control the pouring temperature and pouring speed. This process has the following advantages:
1) Inclined pouring from the top, high pressure, fast flow rate, convenient for rapid filling of molten steel.
2) The use of stepped internal gates, with 2 to 3 internal gates, can disperse the heat at the internal gates, make the steel enter the mold horizontally and stably (prevent air entrapment), and also reduce the concentrated heat dissipation of molten steel entering the upper part of the mold cavity.
3) The feeding (overflow) riser is set at the upper part. The high temperature molten steel flows through the feeding riser from the sprue at a short distance, with less heat dissipation, high temperature and long feeding time. In addition, the relatively low temperature molten steel and slag in the upper part of the mold can be discharged from the overflow riser, which can prevent the occurrence of cold shut and slag inclusion defects in the steel castings.
4) The exhaust riser is set at the upper part, which is convenient for the gas to be discharged from the bottom to the top. The exhaust riser is close to the vertical gate, and the ladle itself plays the role of ignition and air entrainment.
5) The pouring speed of steel castings shall be fast first and then slow. “Fast first” is conducive to the rapid filling of molten steel into the mold cavity, and “Slow later” can make the liquid steel in the mold cavity gradually change from dynamic pressure to static pressure, which is conducive to filling and shrinkage. It is also very important to control the best timing of stock closing (also known as flow closing and deceleration). The experience is to observe the change of the flame at the exhaust riser. When the flame becomes weak from strong to weak, it indicates that the cavity is about to fill. At this time, the stock closing is fast and the flow is slowly to full.