Resin sand casting is a casting process that unleashes the potential for precision and high-quality in metal component production. It offers several advantages that contribute to its ability to achieve precise and reliable results:
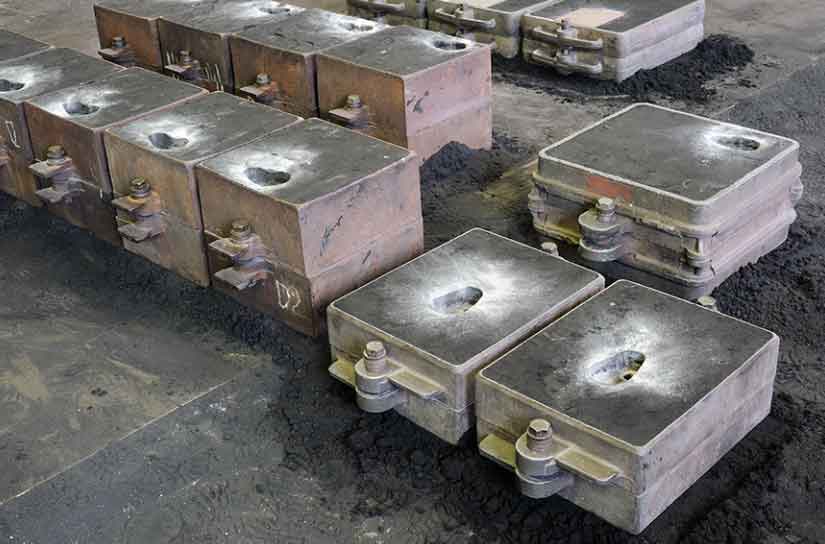
- Dimensional Accuracy: Resin sand casting uses high-quality patterns and molds, which ensures excellent dimensional accuracy in the final castings. This accuracy allows for parts to fit precisely and function as intended in the assembly.
- Tight Tolerances: The process is capable of achieving tight tolerances, which means that the cast components can be produced with minimal deviation from the desired specifications. This is crucial for industries where precise fit and alignment are essential.
- Smooth Surface Finish: Resin sand casting produces parts with a smooth surface finish, reducing the need for additional machining or finishing processes. This not only saves time and resources but also ensures the components’ aesthetic appeal.
- Design Flexibility: The versatility of resin sand casting allows for the production of complex and intricate geometries. This design flexibility empowers engineers to create innovative and sophisticated parts that may not be achievable with other casting methods.
- Consistency and Repeatability: Resin sand casting enables the production of multiple identical components with consistent quality. Once the molds are prepared, the process can be replicated many times, ensuring repeatability and batch-to-batch consistency.
- Reduced Material Waste: Resin sand casting minimizes material waste compared to other casting methods, making it a more sustainable and cost-effective option.
- Rapid Prototyping and Iterations: Resin sand casting is suitable for rapid prototyping, allowing designers to quickly create functional prototypes and iterate designs as needed. This iterative process helps refine the final product and reduces development time.
- Wide Range of Materials: Resin sand casting supports various metals, such as iron, steel, aluminum, and bronze, offering flexibility in material selection to meet specific application requirements.
- Advanced Simulation and Modeling: Modern technology enables simulations and modeling to optimize the casting process and predict potential defects. This helps in identifying potential issues early on, leading to improved part quality.
- Quality Control and Testing: Advanced quality control techniques, such as non-destructive testing and inspection methods, are employed to ensure the integrity and reliability of the cast components.
- Automation and Robotics: Resin sand casting can be integrated with automation and robotics, leading to increased efficiency, reduced human errors, and improved safety.
Overall, resin sand casting provides the precision and quality required for critical applications in industries such as automotive, aerospace, machinery, and more. With its design flexibility, tight tolerances, and consistency, it continues to be a favored choice for achieving high-quality metal components in modern manufacturing.