In view of the reasons for the formation of pores in the cylinder head inner cavity, the sand casting process was improved:
① The melt composite treatment process is adopted. At the same time of argon rotary injection, the refining and modification primary treatment agent is added. After the refining, the temperature of molten aluminum is rapidly reduced to 690 ℃, and the anti-gravity sand casting is completed within 20 minutes to reduce the hydrogen content of the melt;
② The exhaust channel is designed inside the sand core, and the negative pressure pumping scheme is adopted, so that the gas formed after the sand core is heated and decomposed is basically discharged, so as to prevent the formation of a large area of gas film or the formation of subcutaneous pores inside the alloy;
③ The sand core coating is optimized to reduce the gas evolution of the coating and speed up the cooling rate;
④ Adjust the pouring process parameters, reduce the pouring temperature and filling speed, increase the crusting time, lower the crusting and crystallization pressure, improve the strength of sand casting solidification crusting, and prevent gas intrusion.
See Fig. 1 for the fluorescent test results of sand castings after process improvement. It can be seen from the comparison that the surface pores of the air channel wall of sand mold castings have been significantly improved, indicating that the above process improvement has achieved good results.
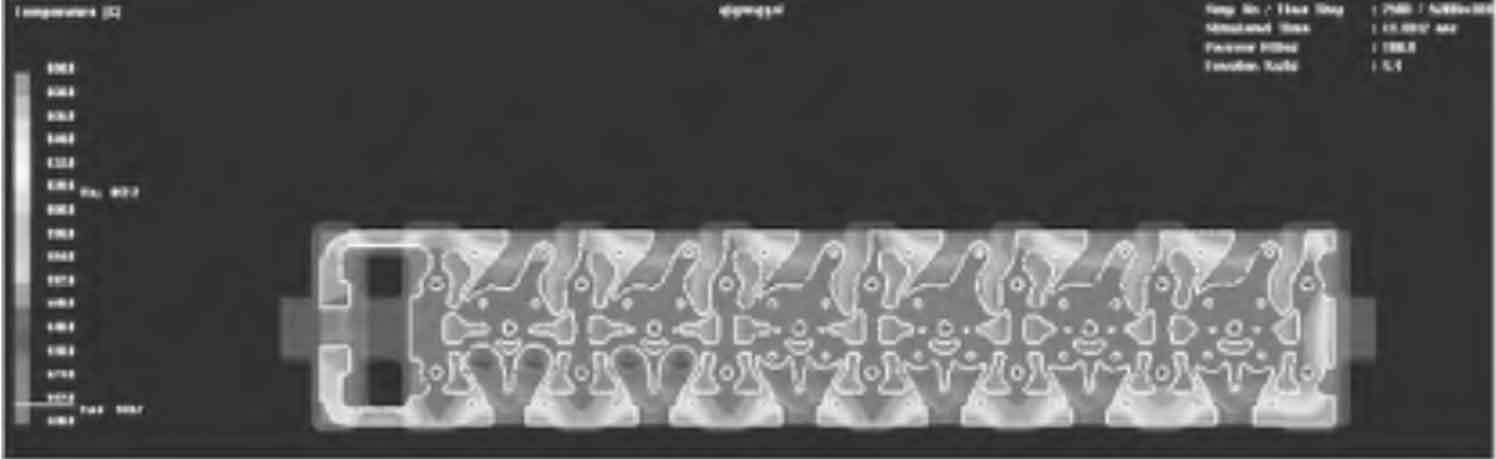
Based on the simulation results in Figure 2, it can be seen that there is no obvious difference between the solidification temperature and solidification speed of each cylinder. Under the new process conditions, the three kinds of sand core forming conditions without coating, graphite coating and alcohol-based zircon powder coating are compared. The fluorescence results in Figure 1 show that there are fewer subcutaneous pores in the inner cavity without coating. Take samples from the same area of each cylinder for low magnification test (Fig. 3), in which the pinhole grade of 2 # test block (non coated airway wall test block) is grade 1, the pinhole grade of 3 # test block (coated with graphite coating) and 4 # test block (alcohol-based zircon powder coating) are grade 2, 3 # test block has no subcutaneous pores, and 4 # test block has a subcutaneous pores. The above phenomenon shows that the coating layer on the surface of sand core has certain influence on the formation of inner cavity pores. The reason is that the coating layer on the surface of the sand core will hinder heat transfer, and the coating itself also has gas generation.
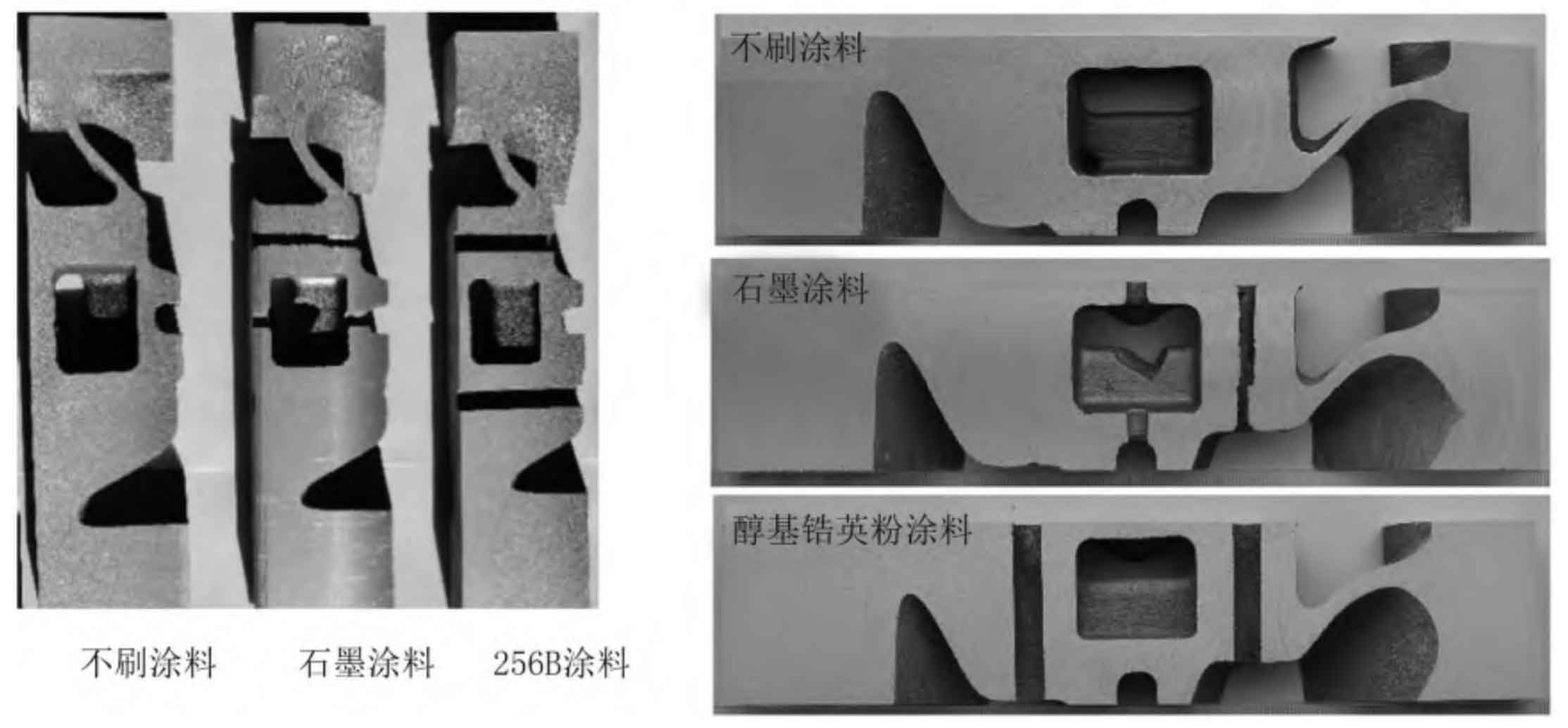
(b) Different coatings are applied to obtain the low power test results of samples