In the production process of nodular cast iron, a certain amount of additives should be added to the molten iron to complete desulfurization, spheroidization and inoculation treatment. Spheroidizing is an important step in the production and research of ductile iron. Over the years, many kinds of spheroidizing methods have been successfully developed at home and abroad, mainly including inserting method, punching method, subcontracting method, in mold method, covering method, wire feeding method, etc. At present, there are still some new spheroidization methods in the research. Some people have made a special summary of the spheroidization methods, but there are still some shortcomings, such as the lack of comparison, the lack of clear objectives for selection or further research. On the basis of previous studies, this paper makes a systematic summary of two more efficient methods.
Balling treatment of cored wire feeding
The additives added in spheroidization are generally characterized by small density, low melting point, low boiling point and easy oxidation. Therefore, cored wire technology has a broad application prospect in the production of nodular cast iron. At present, the application of cored wire technology in nodular iron production mainly focuses on desulfurization, spheroidization and inoculation. The magnesium treatment device for cored wire has been used in production, but the experimental research is still in progress. The main advantages of cored wire spheroidizing process compared with the existing spheroidizing process are shown in Table 2. At the same time, the spheroidizing process of cored wire is affected by many factors, such as the structure and diameter of cored wire, the type and thickness of cladding material, the type and content of spheroidizing agent, the process parameters of wire feeding, the temperature of molten iron, etc., so the process is relatively complex.
Spheroidizing treatment by spheroidizing in mold
In 1968, the structure of in mold spheroidizing process [19,20] was successfully studied in the UK as shown in Figure 12, and a patent was issued in 1972. Up to now, it has been used more and more in developed countries. In this method, the nodularizer of low magnesium alloy is placed in the reaction chamber of the pouring system, and the nodular cast iron is obtained after the reaction with the molten iron. Because the nodular agent also contains silicon, calcium, strontium and other components which play the role of inoculation. Therefore, spheroidization and inoculation can be carried out at the same time. The advantages of intratype spheroidization can be summarized as follows:
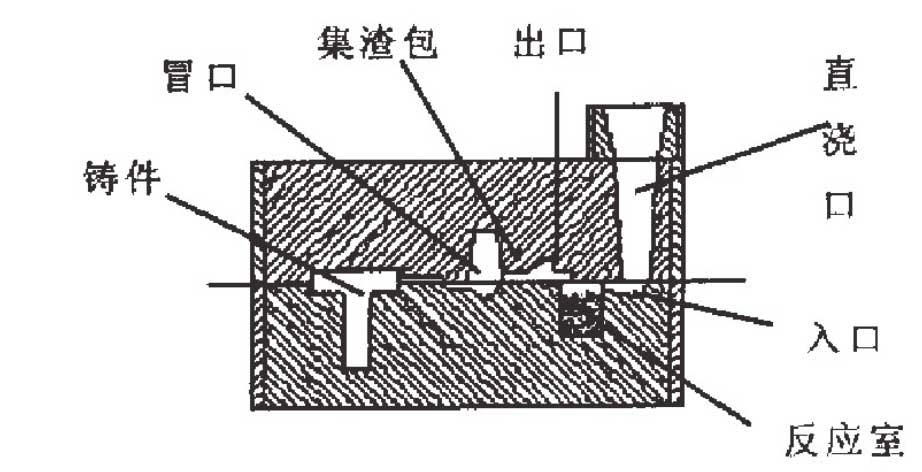
(1) High spheroidizing grade, low alloy content and recovery of magnesium over 80%;
(2) The temperature drop of molten iron is less and the effect of energy saving is good;
(3) The inoculation effect is good, the final Si content is low, and the recycle material can be widely used;
(4) The spheroidization treatment is simple and does not produce pollution;
(5) It is easy to determine the parameters, standardize the production process, simplify the spheroidization process, and has stable quality, which is suitable for assembly line application.
As the length of reaction chamber and sprue is increased, the utilization rate of molding plate is reduced and the production rate is reduced. At the same time, the requirements of temperature, chemical composition, alloy size, reaction chamber design are very strict, and the detection of nodularity rate after furnace is also a problem to be solved.
At present, the foundry technology in developed countries can be summed up as four important goals: protecting the environment, improving the quality and reliability of castings, reducing the production cost and shortening the delivery time. As an important part of the casting technology, the research on the casting technology of nodular cast iron should be on the “highway” as soon as possible, and its development trend should be prospected. Our research on the casting technology of nodular cast iron, especially on the thick wall parts, should be developed rapidly in the future [21].
(1) Vigorously develop new spheroidization and inoculation technology. The driving force of the production of high strength and high toughness ductile iron lies in the continuous progress and improvement of spheroidization and inoculation technology. The development of inoculation technology is often expected to develop new inoculants. However, in recent years, the improvement of inoculation methods, especially late inoculation, has attracted people’s attention. Therefore, in the future, with the development of inoculants, it is possible that the research on inoculation technology will turn to the development of new inoculation methods.
(2) The research on new materials and new process of nodular cast iron should take automobile industry, aerospace industry and nuclear energy industry as the main goal, with the characteristics of strengthening and toughening, lightweight, precision and high efficiency.
(3) The casting process of nodular cast iron is a complex irreversible process. In actual production, there are often many uncontrollable factors or immature processes that lead to the castings being scrapped or failing to reach the predetermined process objectives. Basic theoretical research on major technical equipment and casting technology is carried out, and numerical simulation, physical simulation and expert system are developed [22], The casting technology of nodular cast iron has changed from “experience” to “quantitative”.
(4) We should develop green intensive casting, strengthen the treatment of environmental pollution in the casting process, and strengthen the regeneration and reuse of casting materials.
(5) Realize online and intelligent. It can detect and control the casting process or equipment on-line, reflect the site status timely and accurately, and control the relevant production equipment in real time, so as to keep the casting process or equipment in the best condition. Each monitoring system can cooperate with each other and become an organic whole. The monitoring system can automatically send out accurate and reasonable instructions to control related objects according to the actual situation on site.