After the process design of nodular cast iron, ProCAST was used for process simulation, and the results showed that there was shrinkage hole at the center of the tooth, and the scope of shrinkage defect was larger than the standard requirements. The simulation results are shown in Figure 1. After many process simulations, it is found that setting a riser on the upper part of the tooth has an obvious feeding effect on the tooth, and the location of the shrinkage hole moves from the bottom of the tooth to the middle and upper part, and the size decreases. The analysis shows that the process can be further improved by setting risers and using cold iron at the lower part of the teeth.
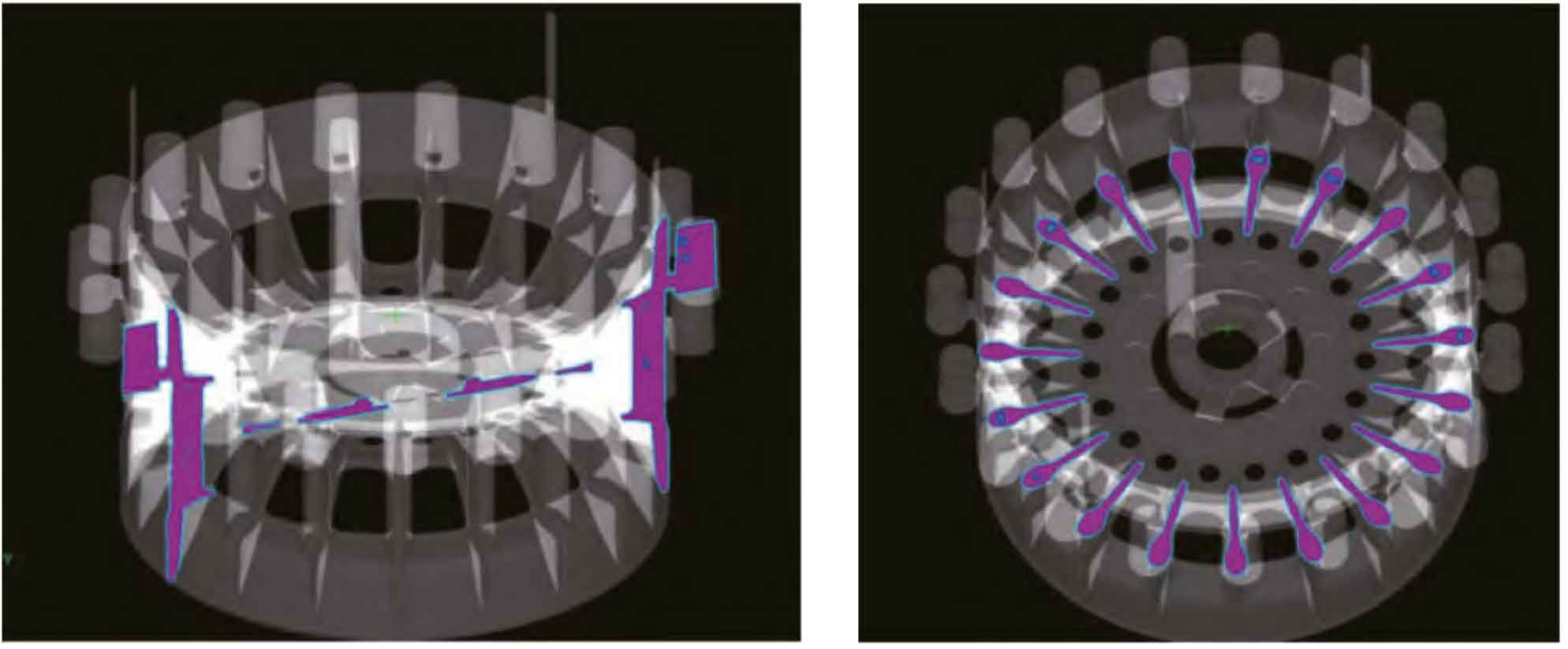
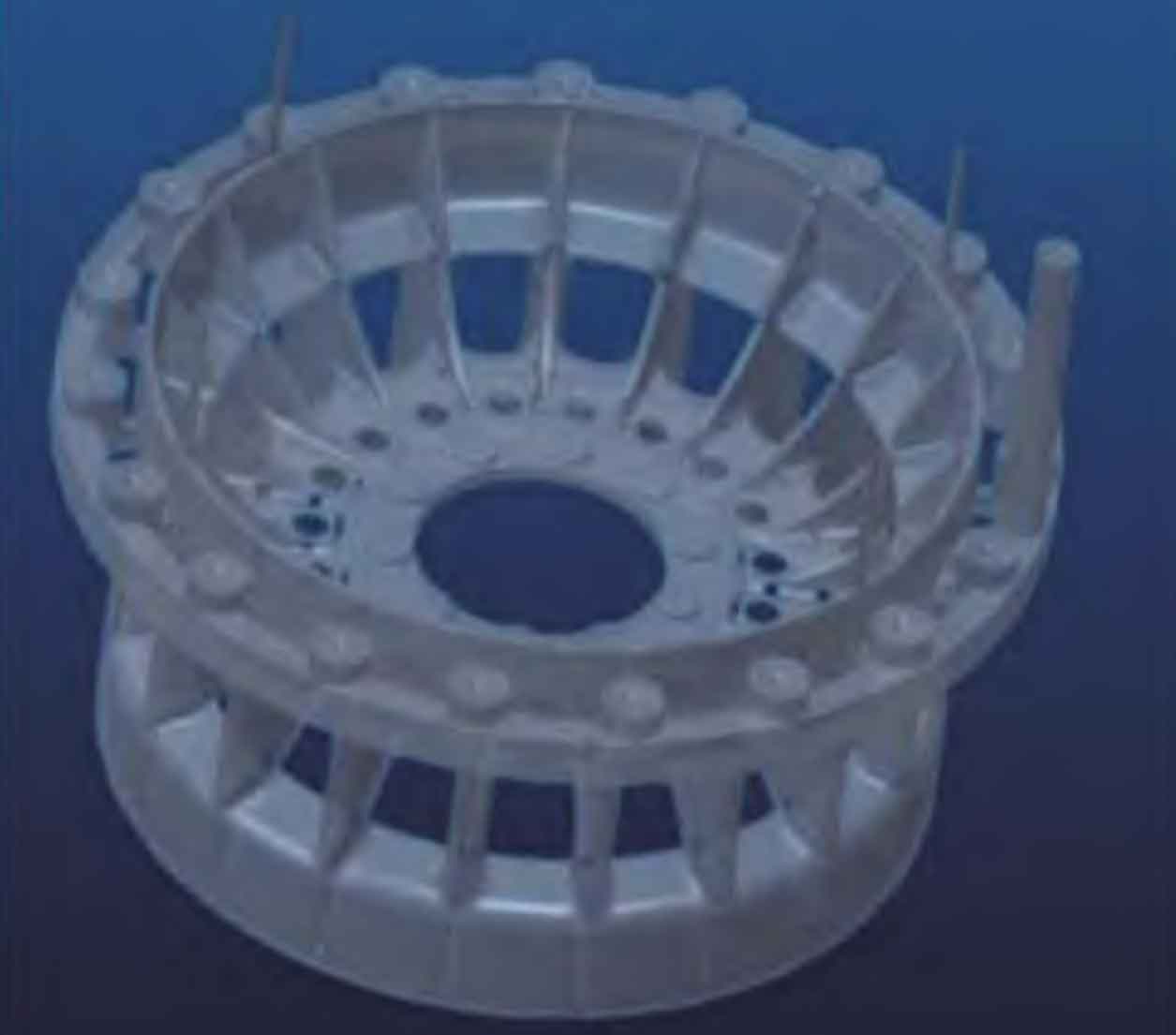
Based on the simulation results of ProCAST process and the analysis of the causes of shrinkage, it is decided to design a riser at the upper part of each independent tooth, place a chill at the lower part of the tooth, the riser plays a role of feeding, and the chill is quenched to reduce the hot spot of the tooth. The riser size is calculated as:
Mass of individual teeth of driving wheel: Gc=4.44 kg, volume Vc=6.03 cm3,
Heat dissipation surface area Ac=5.58 cm2.
Modulus of nodular cast iron: Mc=Vc/Ac=1.08 cm, with controlled pressure riser design.
Quality perimeter quotient: Qm=Gc/Mc3=3.52 kg/cm3.
Riser body modulus: MR=f1f2f3Mc=1.17 cm, where f1=1.19, f2=0.76, f3=1.2, which can be found according to Mc and Qm.
Riser neck modulus: MN=fpf4MR=0.68 cm, where fp=0.65, f4=0.9.
When the diameter of the riser neck is 5.2 cm and the modulus of the riser body is MR=1.17 cm, the ear riser cylindrical non-nest standard structure is selected according to the process plan, and K (solidification coefficient)=H/D=1.8, and the riser is ϕ 80 mm × 120 mm standard riser.
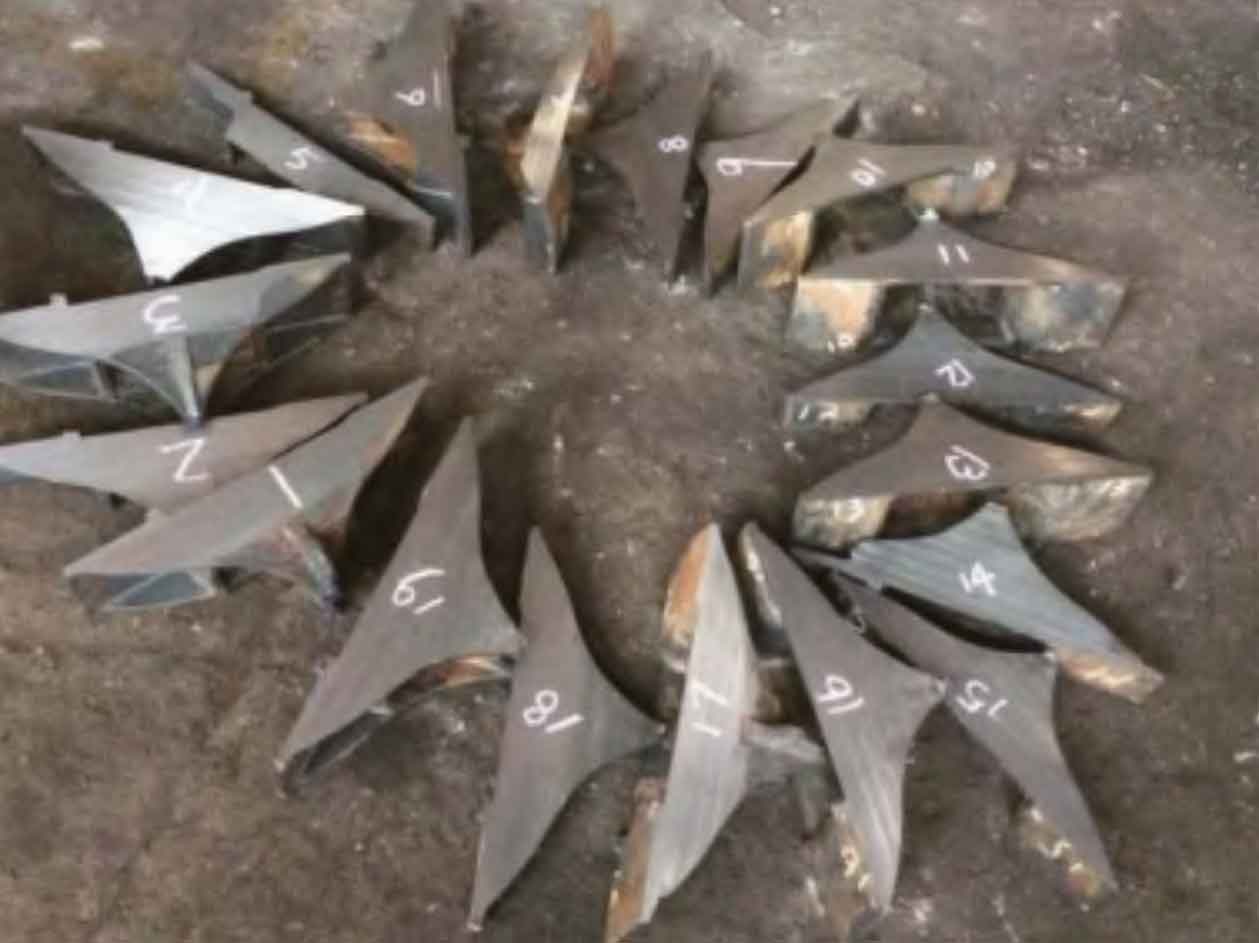
The process of nodular cast iron requires that the sand core of the hot core box should use common coated sand, change the position of the gating system, and connect 19 transverse gates ϕ 80 mm × 120 mm concealed riser, the inner gate connects the riser and the ductile iron casting, and the pouring temperature is 1 355~1 365 ℃. The specific process diagram is shown in Figure 2.
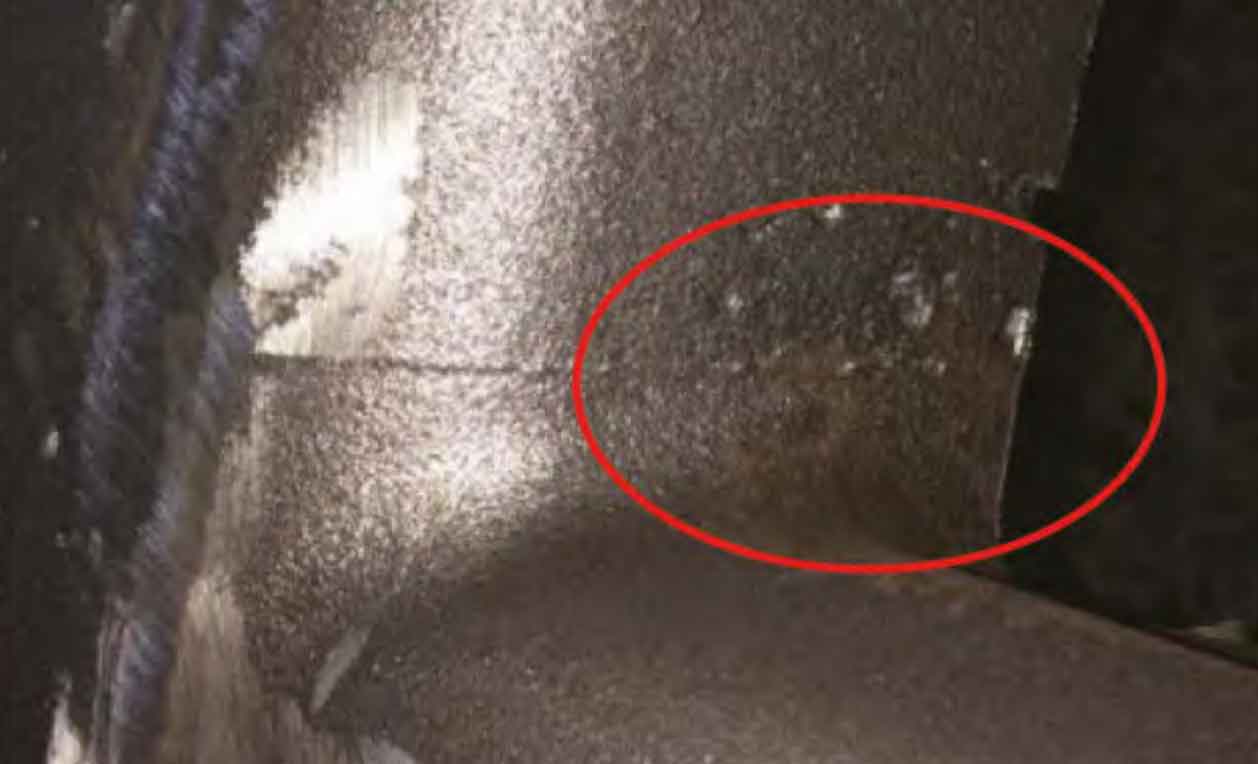
After the trial production of the sample, the tooth anatomy was verified. The shrinkage defect at the center of the tooth was eliminated. Only a few upper teeth had slight porosity. The anatomical results met the requirements of the technical conditions of the drawing. The anatomical results are shown in Figure 3. However, there are large pores on the surface of the casting, resulting in poor surface quality of the casting, as shown in Figure 4. Therefore, further process improvement is required for the surface quality of the casting.