Resin sand casting is a popular method for producing metal parts and components. To improve efficiency in resin sand casting, there are several best practices and techniques you can follow. Here are some key tips to consider:
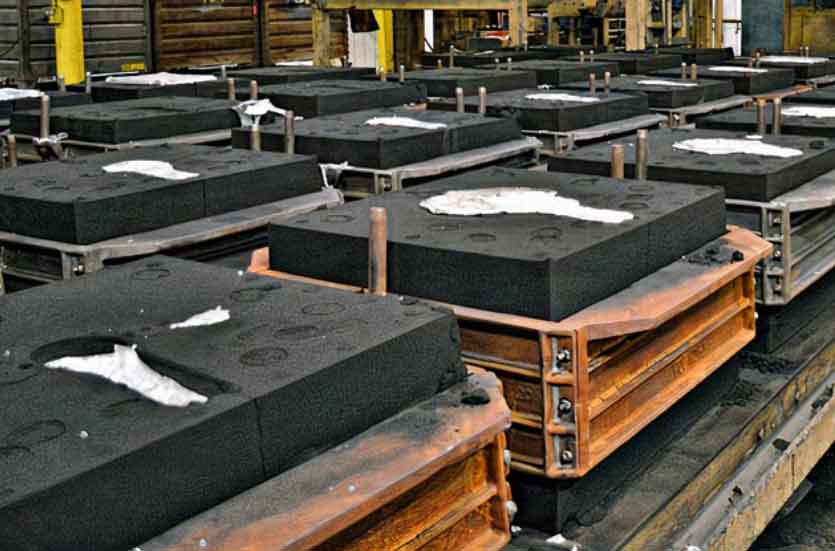
- Design optimization: Start by optimizing the design of the part to reduce material usage and minimize the complexity of the casting process. Simplifying the design can help improve efficiency in both pattern making and casting stages.
- Quality sand preparation: Proper sand preparation is crucial for resin sand casting. Make sure the sand is properly conditioned, free from moisture, and has the right additives and binders. This helps in achieving better mold quality and reducing defects.
- Pattern construction: Invest time and effort into creating high-quality patterns. Ensure that patterns are precise, smooth, and properly vented. High-quality patterns result in better mold formation and improve the overall casting process.
- Effective gating system: Optimize the gating system to allow for smooth and efficient flow of molten metal. Properly designed and positioned gates, sprues, and runners help minimize turbulence and reduce the likelihood of defects such as porosity and cold shuts.
- Venting and risers: Adequate venting of the mold is critical to allow gases to escape during casting. Properly placed vents help prevent defects like gas porosity. Additionally, the use of risers or feeders helps ensure a continuous supply of molten metal, minimizing the risk of shrinkage defects.
- Controlled pouring: Pay attention to the pouring process. Maintain consistent and controlled pouring techniques to achieve uniform filling of the mold cavity. This helps prevent defects like misruns and cold shuts.
- Cooling and solidification: Proper cooling and solidification of the casting are essential for dimensional accuracy and structural integrity. Employ effective cooling techniques such as the use of cooling channels in the mold to speed up the solidification process.
- Process monitoring: Implement a robust process monitoring system to detect and address any issues promptly. Regularly inspect the molds, patterns, and castings to identify potential problems early on. This allows for quick adjustments and reduces the likelihood of defective castings.
- Continuous improvement: Embrace a culture of continuous improvement. Analyze and learn from each casting to identify areas for enhancement. Collect data, measure key performance indicators, and implement corrective actions to refine the process over time.
- Collaboration and knowledge sharing: Encourage collaboration between design, pattern making, and casting teams. Promote knowledge sharing and cross-training to leverage the collective expertise of your team. This can lead to innovative ideas and process improvements.
By implementing these best practices and techniques, you can enhance the efficiency of resin sand casting, resulting in improved productivity, reduced waste, and higher quality castings. Remember, continuous learning and refinement are key to achieving optimal results.