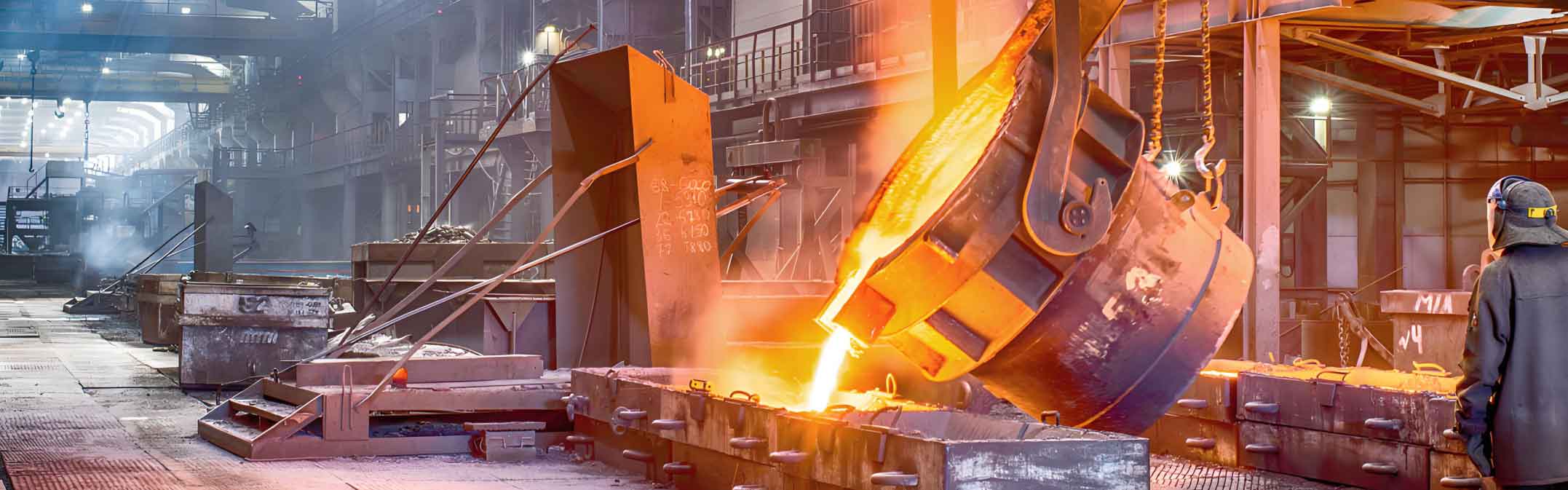
Sand casting is one of the most versatile and widely used casting methods, particularly well-suited for creating complex geometries in metals such as grey cast iron. Achieving high-quality castings with intricate shapes requires meticulous mold design and advanced techniques. This article explores strategies and best practices for improving mold design in sand casting to produce complex geometries, focusing on enhancing dimensional accuracy, surface finish, and overall casting quality.
Introduction to Sand Casting
Sand casting involves creating a mold from a sand mixture and pouring molten metal into the cavity formed by a pattern. The sand mold is then broken away to reveal the metal casting. This process is highly adaptable and economical, making it ideal for producing a wide range of metal components, from simple shapes to complex geometries.
Advantages of Sand Casting
- Versatility: Capable of casting a wide range of metals, including grey cast iron.
- Cost-Effective: Economical for producing large and heavy components.
- Design Flexibility: Allows for complex shapes and sizes.
- Short Lead Times: Quick turnaround for prototype and production runs.
Challenges in Sand Casting Complex Geometries
While sand casting offers numerous benefits, it also presents challenges, particularly when dealing with complex geometries. These challenges include:
- Dimensional Accuracy: Maintaining precise dimensions in complex castings can be difficult.
- Surface Finish: Achieving a smooth surface finish on intricate shapes.
- Defects: Increased risk of casting defects such as porosity, misruns, and cold shuts.
- Mold Stability: Ensuring mold stability and integrity during the casting process.
Strategies for Improving Mold Design
Improving mold design in sand casting for complex geometries involves a combination of advanced techniques, careful planning, and precise execution. The following strategies can help achieve high-quality castings with intricate shapes.
Advanced Pattern Design
The pattern is a replica of the final casting and is used to create the mold cavity. Advanced pattern design techniques can significantly enhance the quality of the mold and the final casting.
- Computer-Aided Design (CAD): Utilize CAD software to design precise and detailed patterns.
- Additive Manufacturing: Employ 3D printing technology to create complex patterns with high accuracy.
- Pattern Shrinkage Allowance: Incorporate appropriate shrinkage allowance in the pattern design to compensate for metal contraction during solidification.
Core Design and Placement
Cores are used to create internal cavities and complex shapes within the casting. Proper core design and placement are crucial for achieving intricate geometries.
- Core Prints: Design core prints to ensure accurate positioning and stability of cores within the mold.
- Core Venting: Incorporate vents in the core design to allow gases to escape, reducing the risk of defects.
- Core Strength: Use strong and stable core materials to maintain shape and integrity during casting.
Mold Material and Composition
The choice of mold material and its composition can significantly impact the quality of the casting, particularly for complex geometries.
- High-Quality Sand: Use high-quality sand with uniform grain size to create smooth mold surfaces.
- Binders and Additives: Select appropriate binders and additives to enhance mold strength and stability.
- Mold Coating: Apply mold coatings to improve surface finish and reduce metal-mold reactions.
Mold Design Strategy | Description |
---|---|
Advanced Pattern Design | Utilize CAD and 3D printing for precise patterns |
Core Design and Placement | Ensure accurate positioning and stability of cores |
Mold Material and Composition | Use high-quality sand, binders, and additives |
Mold Coating | Apply coatings to improve surface finish |
Gating and Risering Systems
The gating and risering systems control the flow of molten metal into the mold and ensure proper feeding during solidification. Optimizing these systems is essential for complex geometries.
- Gating Design: Design gating systems to ensure smooth and turbulence-free flow of molten metal.
- Riser Placement: Place risers strategically to provide adequate feed metal and minimize shrinkage defects.
- Chills and Insulators: Use chills and insulators to control the solidification rate and enhance the quality of the casting.
Simulation and Analysis
Computer simulation and analysis tools can predict potential issues in the mold design and casting process, allowing for optimization before actual production.
- Flow Simulation: Use flow simulation software to analyze and optimize the flow of molten metal within the mold.
- Solidification Analysis: Perform solidification analysis to predict and mitigate shrinkage and porosity defects.
- Stress Analysis: Conduct stress analysis to ensure mold stability and integrity during casting.
Process Control and Quality Assurance
Implementing strict process control and quality assurance measures can help achieve consistent and high-quality castings.
- Process Monitoring: Monitor critical parameters such as temperature, pressure, and metal flow during casting.
- Inspection and Testing: Perform regular inspection and testing of molds and castings to identify and address defects.
- Continuous Improvement: Continuously review and improve mold design and casting processes based on feedback and analysis.
Optimization Strategy | Description |
---|---|
Gating and Risering Systems | Design to ensure smooth metal flow and proper feeding |
Simulation and Analysis | Use software tools to predict and optimize mold performance |
Process Control and Quality Assurance | Monitor parameters and perform regular inspections |
Case Studies
Case Study 1: Complex Engine Block Casting
Challenge
A complex engine block with intricate internal passages and thin walls required precise mold design to avoid defects such as porosity and misruns.
Solution
- Pattern Design: Utilized CAD and 3D printing to create a detailed pattern with appropriate shrinkage allowance.
- Core Design: Designed cores with venting and strong core materials to ensure stability.
- Simulation: Conducted flow and solidification simulation to optimize gating and risering systems.
Result
The optimized mold design resulted in a defect-free engine block with excellent dimensional accuracy and surface finish.
Parameter | Details |
---|---|
Pattern Design | CAD and 3D printing for detailed pattern |
Core Design | Vented cores with strong materials |
Simulation | Flow and solidification simulation |
Result | Defect-free engine block with high accuracy |
Case Study 2: Intricate Gear Housing Casting
Challenge
A gear housing with complex geometry and internal cavities required a mold design that could ensure structural integrity and surface finish.
Solution
- Advanced Pattern Design: Used CAD software to design a precise pattern with core prints for accurate core placement.
- Core Placement: Implemented core prints and vents to ensure proper positioning and gas escape.
- Quality Assurance: Implemented strict process control and regular inspections to maintain quality.
Result
The gear housing casting was produced with minimal defects, high structural integrity, and an excellent surface finish.
Parameter | Details |
---|---|
Pattern Design | CAD software for precise pattern |
Core Placement | Core prints and vents for accurate positioning |
Quality Assurance | Process control and regular inspections |
Result | High integrity and excellent surface finish |
Conclusion
Improving mold design in sand casting for complex geometries involves a comprehensive approach that includes advanced pattern design, core design and placement, appropriate mold materials, and optimized gating and risering systems. Utilizing simulation and analysis tools further enhances the design process, ensuring high-quality castings with intricate shapes. By implementing these strategies and best practices, manufacturers can achieve superior grey cast iron castings that meet the stringent requirements of modern engineering and manufacturing.
Strategy | Description |
---|---|
Advanced Pattern Design | CAD and 3D printing for precise patterns |
Core Design and Placement | Ensure accurate core positioning and stability |
Mold Material and Composition | High-quality sand, binders, additives, and coatings |
Gating and Risering Systems | Design for smooth flow and proper feeding |
Simulation and Analysis | Use software tools for optimization |
Process Control and Quality Assurance | Monitor and inspect for consistent quality |
By adopting these advanced methods and technologies, the sand casting process can be significantly improved, resulting in high-quality, defect-free grey cast iron castings suitable for even the most complex and demanding applications.