Resin sand casting plays a significant role in enhancing metal fabrication productivity through various advantages and process improvements. Its versatility, speed, and precision contribute to improved productivity in several ways:
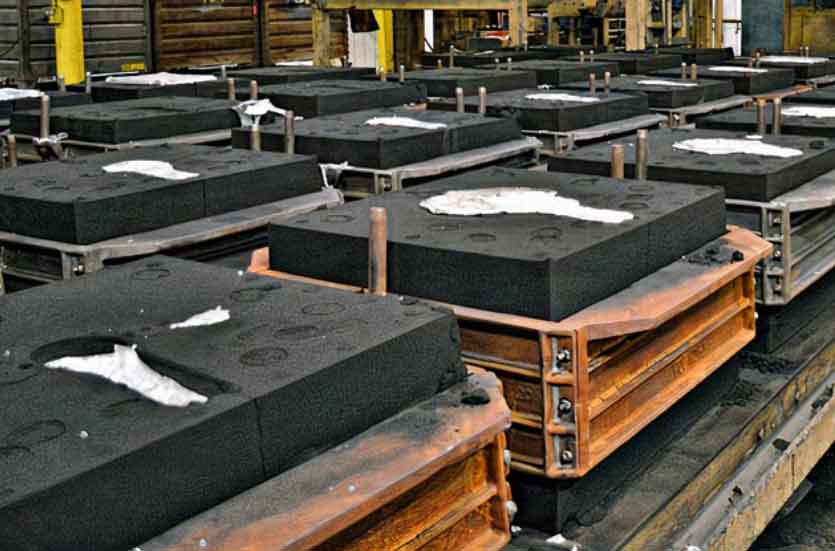
1. Rapid Prototyping and Short Lead Times:
Resin sand casting allows for the rapid production of molds, reducing the time required for pattern creation and mold preparation. This speed facilitates faster prototyping and shortens lead times, enabling manufacturers to bring new products to market more quickly.
2. Cost-Effective Tooling and Setup:
Resin sand casting requires simpler and more cost-effective tooling compared to other casting methods like die casting or investment casting. This reduces upfront costs and setup time, making it an attractive choice for projects with medium to large production runs.
3. Efficient Production of Complex Geometries:
The ability of resin sand casting to produce complex geometries and intricate designs in a single mold helps eliminate the need for multiple manufacturing steps or assemblies. This streamlines production and reduces the number of components that need to be joined together.
4. Reduced Post-Casting Finishing:
The high dimensional accuracy and surface finish achieved in resin sand casting often reduce the need for extensive post-casting finishing operations. This saves time and resources, further contributing to improved productivity.
5. Flexibility in Material Selection:
Resin sand casting is compatible with a wide range of metals and alloys. Manufacturers can choose materials that best suit the application’s requirements, such as strength, corrosion resistance, or thermal conductivity, enhancing product performance and reliability.
6. Integration with 3D Printing:
The integration of 3D printing with resin sand casting allows for the production of rapid and precise patterns and cores. This integration streamlines the design iteration process, making it easier to optimize component designs and reducing overall development time.
7. Tooling Flexibility for Small Batch Production:
Resin sand casting offers tooling flexibility that makes it ideal for small to medium batch production runs. Manufacturers can efficiently produce small quantities of components without incurring the high tooling costs associated with other methods.
8. Improved Quality Control and Consistency:
Resin sand casting’s precise molding techniques, along with the use of resin-coated sand, contribute to consistent and uniform mold properties. This leads to improved casting quality and dimensional accuracy, ensuring consistent and reliable final products.
9. Reduced Material Waste and Scrap:
Resin sand casting’s controlled mold filling and solidification processes help reduce defects and scrap, leading to higher material yields and cost savings.
10. Capacity for Design Optimization:
The design flexibility provided by resin sand casting allows engineers to optimize designs for material efficiency, weight reduction, and improved functionality, leading to more productive and innovative products.
Resin sand casting enhances metal fabrication productivity by streamlining processes, reducing lead times, and enabling the efficient production of complex and high-quality metal components. Its cost-effectiveness, versatility, and ability to integrate with advanced technologies contribute to improved efficiency and competitiveness in the manufacturing industry.