Spheroidal graphite cast iron (SG iron), also known as ductile iron, is a versatile material known for its excellent mechanical properties, including high strength, ductility, and resistance to wear and fatigue. These characteristics make it an essential material in various industries, such as automotive, construction, and heavy machinery. However, achieving consistent quality in spheroidal graphite cast iron production remains a challenge due to the complexities involved in the casting process. This article explores strategies to improve the quality and consistency of spheroidal graphite cast iron, detailing the critical factors, techniques, and future trends in the production process. Comprehensive tables and lists are included to enhance understanding.
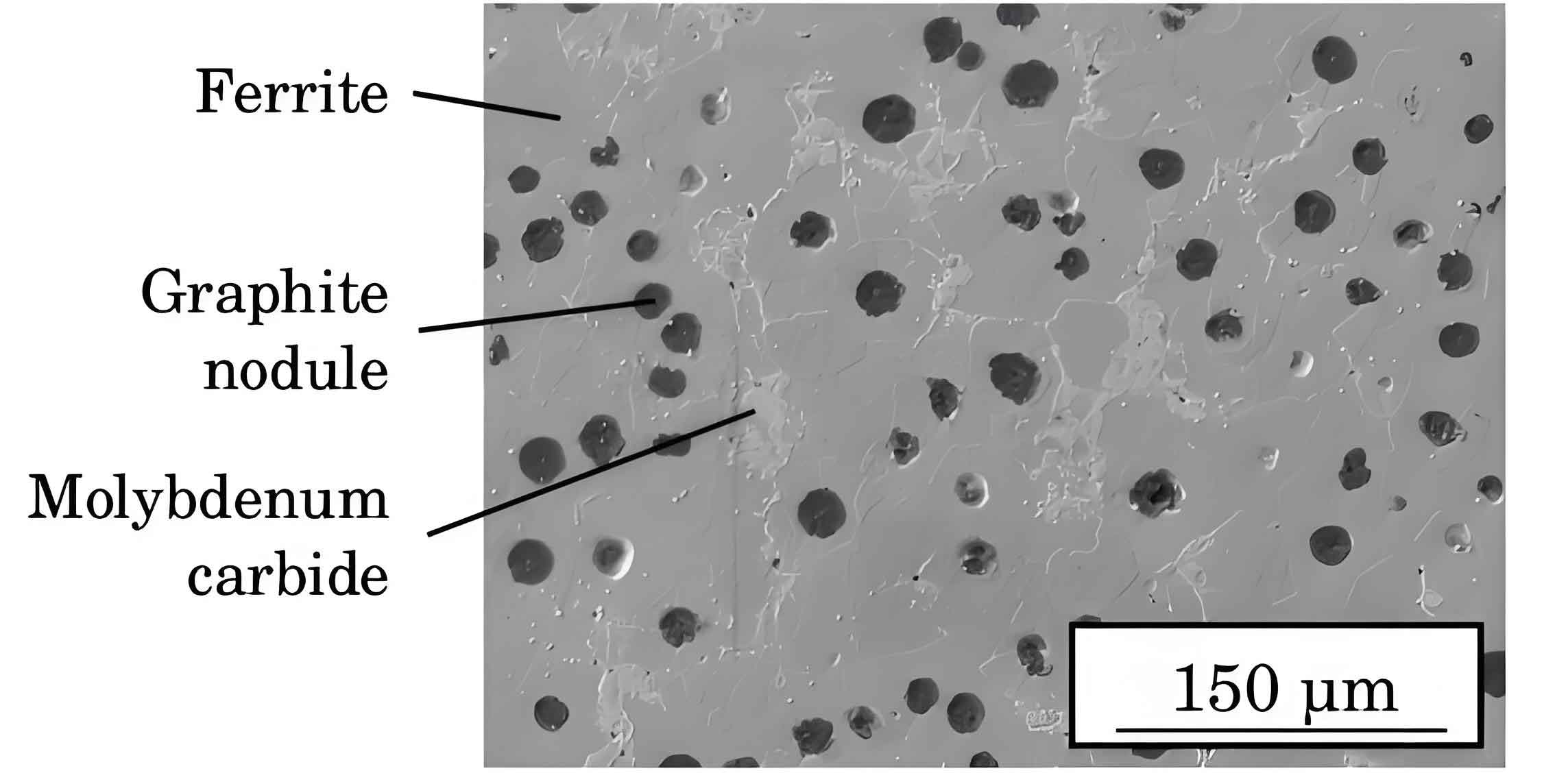
Introduction
The production of spheroidal graphite cast iron involves the addition of magnesium or cerium to molten iron, which modifies the graphite structure from flakes to spheroids. This transformation significantly enhances the material’s mechanical properties. However, the process requires precise control over various parameters to ensure consistent quality. Factors such as raw material quality, melt chemistry, inoculation techniques, and cooling rates must be meticulously managed to achieve optimal results.
Critical Factors in Spheroidal Graphite Cast Iron Production
- Raw Material Quality:
- High-quality raw materials are essential to minimize impurities and ensure consistent properties.
- Melt Chemistry:
- Accurate control of the chemical composition, including carbon, silicon, magnesium, and trace elements, is crucial.
- Inoculation Techniques:
- Effective inoculation promotes the formation of spheroidal graphite and prevents the formation of undesirable carbides.
- Cooling Rates:
- Controlled cooling rates are necessary to achieve the desired microstructure and mechanical properties.
- Process Control:
- Implementing rigorous process control measures to monitor and adjust parameters in real-time.
Table: Critical Factors in Spheroidal Graphite Cast Iron Production
Factor | Description | Impact on Quality and Consistency |
---|---|---|
Raw Material Quality | High-quality raw materials with minimal impurities | Ensures consistent properties |
Melt Chemistry | Accurate control of chemical composition | Maintains desired mechanical properties |
Inoculation Techniques | Effective inoculation to promote spheroidal graphite formation | Prevents formation of undesirable carbides |
Cooling Rates | Controlled cooling rates | Achieves desired microstructure and properties |
Process Control | Rigorous monitoring and adjustment of parameters | Ensures consistency and reduces defects |
Strategies for Improving Quality and Consistency
- Optimizing Raw Material Selection:
- High-Purity Pig Iron: Using high-purity pig iron to minimize impurities.
- Consistent Scrap Sources: Ensuring consistency in scrap material sources to reduce variability.
- Precision in Melt Chemistry Control:
- Spectrographic Analysis: Utilizing spectrographic analysis to monitor and adjust chemical composition.
- Automated Alloying Systems: Implementing automated systems for precise alloy additions.
- Advanced Inoculation Techniques:
- Pre-Inoculation: Adding inoculants to the molten iron before casting.
- Late Inoculation: Introducing inoculants just before pouring to enhance effectiveness.
- Controlled Cooling and Solidification:
- Chilling Methods: Using chill blocks to control cooling rates.
- Heat Treatment: Applying post-casting heat treatments to refine microstructure.
- Enhanced Process Control:
- Real-Time Monitoring: Implementing real-time monitoring systems for temperature, composition, and other critical parameters.
- Statistical Process Control (SPC): Using SPC techniques to analyze and control production processes.
List: Key Strategies for Improving Quality and Consistency
- Optimizing Raw Material Selection:
- High-purity pig iron
- Consistent scrap sources
- Precision in Melt Chemistry Control:
- Spectrographic analysis
- Automated alloying systems
- Advanced Inoculation Techniques:
- Pre-inoculation
- Late inoculation
- Controlled Cooling and Solidification:
- Chilling methods
- Heat treatment
- Enhanced Process Control:
- Real-time monitoring
- Statistical process control (SPC)
Future Trends in Spheroidal Graphite Cast Iron Production
- Integration of Industry 4.0 Technologies:
- IoT and AI: Utilizing IoT and AI for predictive maintenance, process optimization, and real-time data analytics.
- Digital Twin Technology: Creating digital twins of the production process to simulate and optimize performance.
- Sustainable Production Practices:
- Recycling and Reuse: Increasing the use of recycled materials to reduce environmental impact.
- Energy Efficiency: Implementing energy-efficient technologies to reduce the carbon footprint.
- Advanced Material Engineering:
- Nanotechnology: Incorporating nanomaterials to enhance mechanical properties and performance.
- Smart Materials: Developing smart materials with self-healing and adaptive properties.
- Collaborative Research and Development:
- Industry-Academia Partnerships: Fostering collaborations between industry and academia to drive innovation.
- Government Initiatives: Leveraging government initiatives and funding to support advanced research.
- Customization and Modular Production:
- Custom Alloys: Developing custom alloy compositions tailored for specific applications.
- Modular Casting Systems: Implementing modular casting systems for flexible and scalable production.
Table: Future Trends in Spheroidal Graphite Cast Iron Production
Trend | Description | Expected Benefits |
---|---|---|
Industry 4.0 Technologies | IoT, AI, and digital twins for process optimization | Predictive maintenance, real-time data analytics |
Sustainable Production | Recycling, reuse, and energy-efficient technologies | Reduced environmental impact, lower carbon footprint |
Advanced Material Engineering | Nanotechnology and smart materials | Enhanced mechanical properties, self-healing capabilities |
Collaborative R&D | Industry-academia partnerships and government initiatives | Innovation, advanced research support |
Customization and Modular Production | Custom alloys and modular casting systems | Flexible and scalable production |
Conclusion
Improving the quality and consistency of spheroidal graphite cast iron production is essential for meeting the demands of high-performance applications across various industries. By focusing on critical factors such as raw material quality, melt chemistry, inoculation techniques, cooling rates, and process control, manufacturers can achieve superior results. The integration of advanced technologies, sustainable practices, and collaborative research will further drive innovation and efficiency in spheroidal graphite cast iron production. As these trends continue to evolve, spheroidal graphite cast iron will remain a cornerstone material, delivering exceptional performance and reliability in engineering applications.