1. Introduction
Diesel engine exhaust pipes play a crucial role in the exhaust system of diesel engines. The quality of these pipes directly affects the performance and durability of the engine. However, during the casting process, various defects may occur, which can lead to reduced mechanical properties, increased porosity, and even failure of the pipes. This article aims to analyze the common casting defects in diesel engine exhaust pipes and propose corresponding prevention measures to improve the casting quality.
2. Casting Process of Diesel Engine Exhaust Pipes
The diesel engine exhaust pipes are typically made of QT400 – 18 material, which has specific requirements for tensile strength, yield strength, and elongation. The casting process involves several steps, as shown in the following table:
Casting Process Steps | Description |
---|---|
Molding | Using furan resin self – hardening sand for molding, with a specific parting method and layout. |
Core – making | Producing cores with appropriate materials and techniques. |
Assembly | Assembling the molds and cores. |
Pouring | Pouring molten metal into the molds from specific locations. |
3. Common Casting Defects and Their Causes
3.1. Porosity
Porosity is a common defect in exhaust pipe casting, which can be divided into different types. The main causes are as follows:
Cause | Explanation |
---|---|
High resin and curing agent content in molding sand | The reaction of resin and curing agent during pouring produces a large amount of gas, which may not escape in time and form pores. |
High moisture content in molds (cores) due to long storage time | The moisture evaporates during pouring, generating gas and leading to porosity. |
Poor venting of the mold cavity during pouring | The gas in the cavity cannot be discharged smoothly, resulting in pores. |
3.2. Sand Holes
Sand holes occur when sand particles from the mold or core enter the molten metal and remain in the casting. The reasons for this defect are:
Cause | Explanation |
---|---|
Low strength of molding (core) sand | The sand is easily washed into the cavity during pouring. |
Incomplete cleaning of broken sand in the cavity and gating system before core – setting and closing the mold | The remaining sand enters the cavity during pouring and forms sand holes. |
3.3. Cold Shuts
Cold shuts are caused by the improper fusion of molten metal during pouring, resulting in seams or gaps in the casting. The main factors contributing to cold shuts are:
Cause | Explanation |
---|---|
Unstable pouring process | Interruptions in the liquid flow can prevent proper fusion. |
Metal leakage from the parting surface during pouring | This leads to insufficient metal volume and cold shuts. |
Low pouring temperature | The molten metal may solidify too quickly to fuse properly. |
4. Prevention Measures for Casting Defects
4.1. Prevention of Porosity
To prevent porosity, the following measures can be taken:
Prevention Measure | Details |
---|---|
Drying the mold | Apply water – based graphite powder coating and dry the mold in a drying oven at 160 – 180°C for 3 – 4 hours. Regularly monitor the oven operation. |
Controlling the gas evolution of molding sand | Keep the loss on ignition of recycled sand below 0.3% and reduce the resin addition while ensuring sand strength. The current resin addition is 0.8% – 1.1%, and the curing agent addition is 30% – 60%. |
Protecting molds and cores from moisture | Adhere to the “first – made – first – used” principle, and ensure the storage time does not exceed 3 – 5 days. Protect them from rain and dry if wet. |
Improving mold venting | Ensure complete setup of risers and vents during molding and core – making. Check for blockages during mold assembly and ignition for gas extraction during pouring. |
4.2. Prevention of Sand Holes
The following methods can be used to prevent sand holes:
Prevention Measure | Details |
---|---|
Optimizing molding (core) sand formulation | Ensure a proper ratio of binder (0.8% – 1.2% of sand weight), curing agent (30% – 60% of binder weight), and control sand strength at 0.8 – 1.5 MPa. Monitor sand strength daily and test the ratio regularly. |
Controlling the use time of molding (core) sand | Adjust the curing agent addition based on environmental conditions to control the usable time within 10 – 15 minutes. |
Improving molding, core – making, and core – setting operations | Compact the sand during molding, especially in hard – to – reach areas. Wait for the gating system to harden before removing the pattern to avoid sand collapse. |
4.3. Prevention of Cold Shuts
To prevent cold shuts, the following steps can be implemented:
Prevention Measure | Details |
---|---|
Ensuring mold assembly quality | Clean the cavity and gating system thoroughly. Apply foundry glue to the parting surface to prevent leakage. Control the pouring temperature at 1350 – 1360°C. |
Controlling the pouring process | Measure the molten metal temperature before pouring. Align the ladle with the pouring cup and ensure a stable pouring process. |
5. Implementation and Effectiveness of Prevention Measures
Before implementing the prevention measures, the defect rate of a batch of exhaust pipe castings was 13.3%. After implementing the measures, 1230 exhaust pipes were produced, with 15 cases of porosity, 6 cases of sand holes, and 4 cases of cold shuts. The defect rate was reduced to 2.03%, significantly improving the casting quality.
6. Conclusion
In conclusion, the quality of molding (core) sand, the baking process of the mold, and the operation details in each casting step have a significant impact on the occurrence of casting defects. By implementing the proposed prevention measures, the defect rate of diesel engine exhaust pipe castings can be effectively reduced, improving the overall quality and performance of the pipes. Future research can focus on further optimizing the casting process and exploring new materials and techniques to enhance the casting quality of diesel engine exhaust pipes.
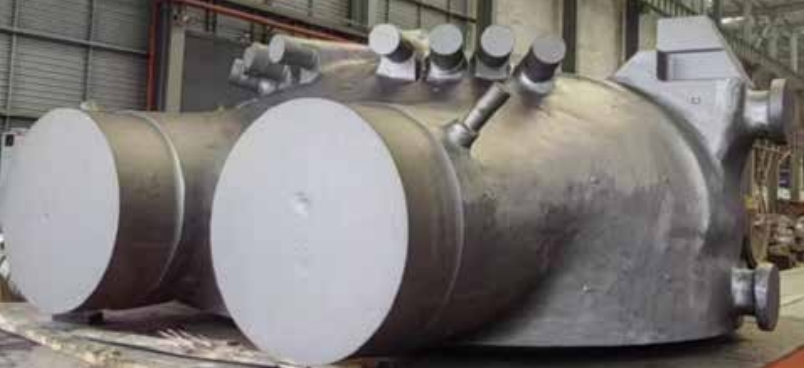