In metal casting, minimizing defects is a crucial aspect of enhancing product quality and manufacturing efficiency. Various strategies can significantly reduce casting defects, including porosity, shrinkage, and hot tears. This article focuses on strategies for minimizing defects to improve the casting process.
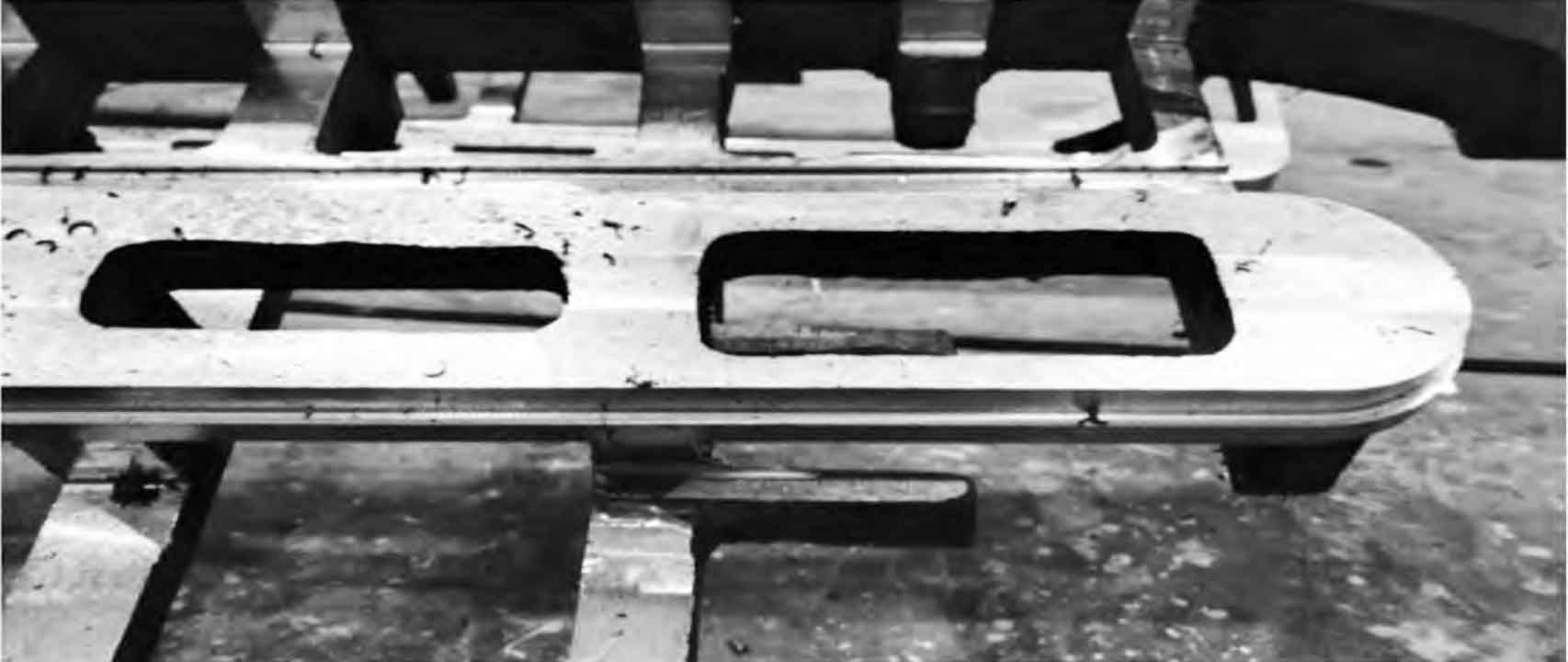
- Design Considerations: Designing the mold and gating system properly is crucial to minimize defects. This involves ensuring uniform cooling, strategic placement of risers and gates, and the use of chills to manage cooling rates in thick sections. Using simulation software can help visualize and predict potential issues before physical prototyping.
- Quality of Materials: The quality of both the casting metal and mold material can significantly affect the final casting’s quality. Ensuring the cleanliness of molten metal, proper degassing, and using quality mold materials can minimize defects like inclusions and porosity.
- Controlled Pouring: Maintaining the correct pouring temperature and velocity can prevent defects such as misruns, cold shuts, and gas porosity. Automated pouring systems can help maintain these parameters consistently.
- Controlled Cooling: Controlled cooling can minimize defects such as shrinkage and hot tears. Cooling rates can be managed by strategic mold design, placement of risers and chills, and post-pour heat treatment.
- Proper Venting: Proper venting in the mold can prevent gas-related defects like porosity and blowholes. This includes designing venting channels in the mold and using permeable mold materials.
- Post-Casting Inspection: Regular inspection of the castings can help identify recurring defects, enabling corrective action. Techniques like radiography, ultrasonic testing, and dye penetrant inspection can be used to identify both surface and subsurface defects.
- Continuous Process Improvement: Adopting a continuous process improvement approach, where data from inspections and tests are analyzed to identify root causes of defects and develop corrective actions, can significantly minimize defects over time.
Improving the casting process and minimizing defects requires a systematic approach that focuses on design, material quality, process control, and continuous improvement. As technologies advance, manufacturers have more tools at their disposal to predict, identify, and address casting defects, leading to improved product quality, reduced costs, and increased customer satisfaction. With a concerted effort, manufacturers can significantly minimize casting defects and improve the overall casting process.