Porosity, characterized by the presence of voids or pores in a material, is a common challenge in sand casting. While the process offers a cost-effective method for producing complex metal parts, the occurrence of porosity can significantly impact the quality, performance, and aesthetic appeal of the final product. This article delves into the various ways porosity affects the quality of sand castings.
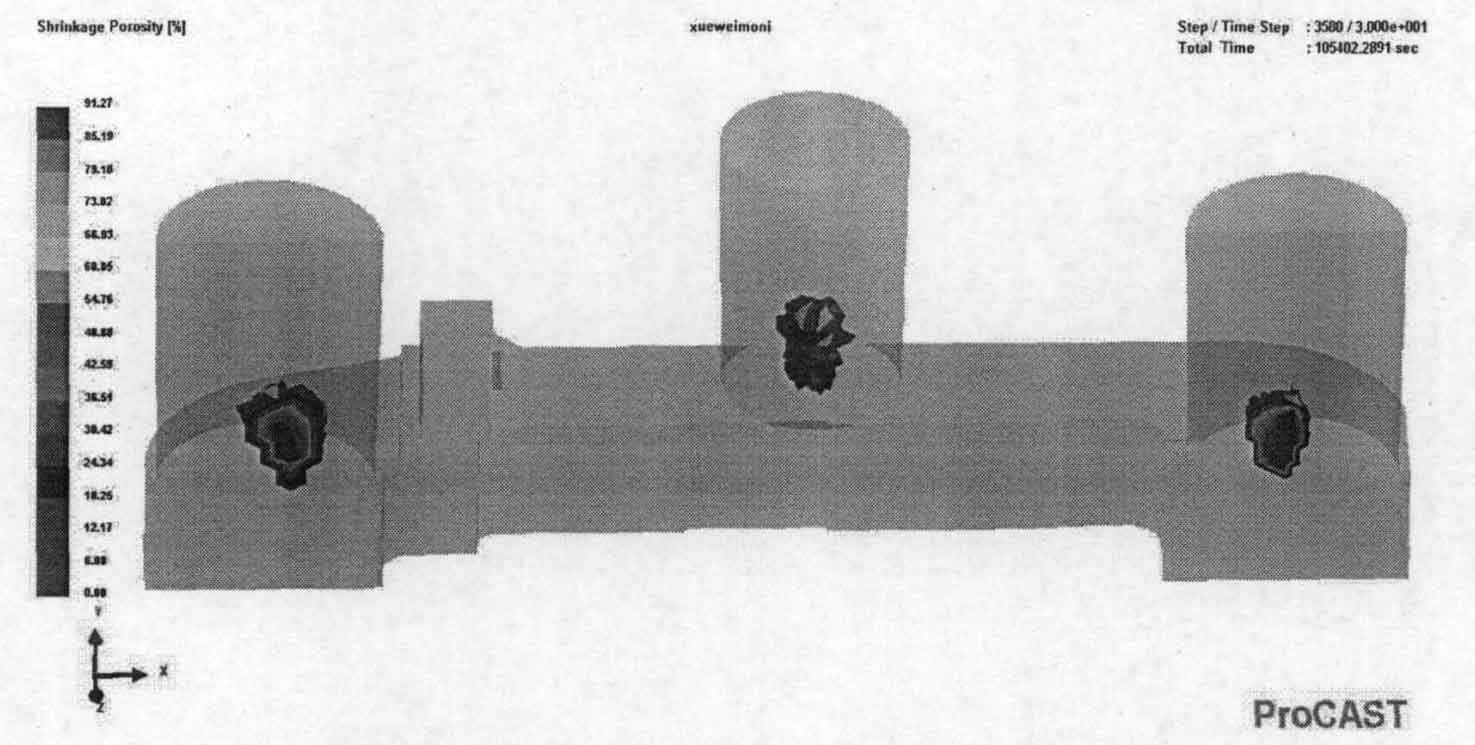
1.Mechanical Properties:
Porosity can drastically compromise the mechanical properties of a sand casting. The presence of voids within the material disrupts the metal’s structural integrity, reducing its overall strength and durability.
- Tensile Strength: Porous castings often exhibit lower tensile strength, making them more susceptible to failure under tension.
- Fatigue Resistance: Voids in the casting can serve as stress concentrators, acting as initiation sites for cracks. This can reduce the casting’s resistance to fatigue, leading to premature failure under cyclic loads.
- Impact Resistance: The impact resistance of a casting is also affected by porosity. The voids can absorb energy during an impact, leading to deformation or fracture.
2.Aesthetic Quality:
Porosity can lead to surface imperfections in the casting, impacting its aesthetic quality. Pores that reach the surface can result in rough, uneven textures that may require additional finishing processes to rectify. In applications where visual appeal is crucial, such as decorative pieces or consumer products, porosity can significantly detract from the product’s value.
3.Dimensional Accuracy:
Porosity can influence the dimensional accuracy of sand castings. Voids within the casting can cause it to deform during cooling, leading to deviations from the intended dimensions. This can pose challenges in applications where tight tolerances are required.
4.Corrosion Resistance:
Porosity can also compromise the corrosion resistance of sand castings. Voids in the material can trap corrosive agents, providing sites for localized corrosion to occur. This can reduce the lifespan of the casting, particularly in harsh or corrosive environments.
The impact of porosity on the quality of sand castings is multifaceted, affecting mechanical properties, aesthetic quality, dimensional accuracy, and corrosion resistance. Understanding the implications of porosity can help manufacturers identify strategies to mitigate this issue, such as optimizing mold design, controlling pouring techniques, and employing effective gas control methods. By doing so, it’s possible to enhance the quality and performance of sand castings.