Taking the circular casting defect with radius r as an example, the influence of the distance between the hole center and the structure surface on the stress concentration factor is analyzed, as shown in Fig. 1. The relative position of casting defects in the structure is represented by the ratio D / R of the distance d between the center of the casting defect and the surface and the casting defect radius R. It is divided into several grades: ① D / R ≤ – 1, no casting defects; ② – 1 < D / R < 0, there is only a small part of casting defects in the structure; ③ D / r = 0, half of the casting defects are in the structure, and the center of the casting defects is just on the surface of the structure; ④ 0 < D / R < 1, the structure contains most of the casting defects; ⑤ D / r = 1, casting defects are completely located in the structure and tangent to the surface of the structure; ⑥ D / R > 1 casting defects are completely contained in the structure.
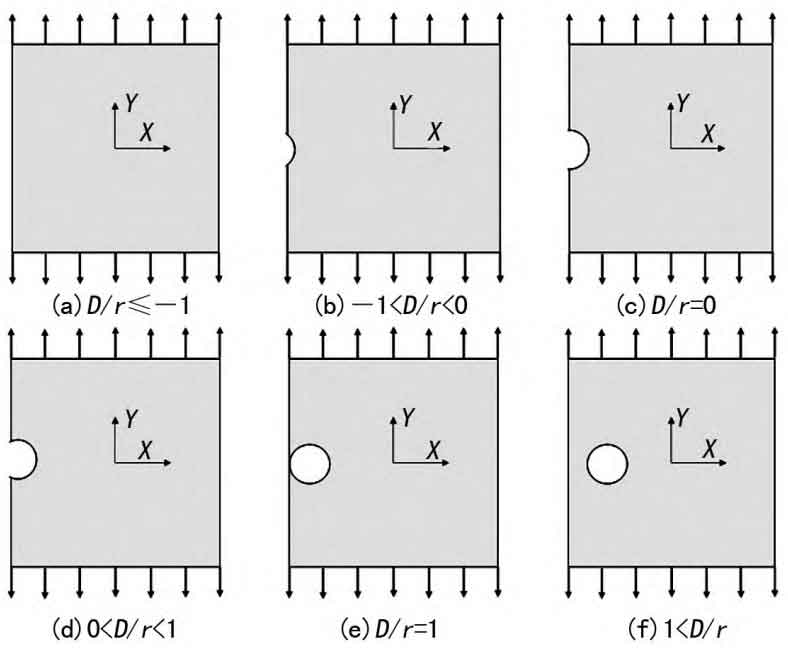
An infinite thin plate model containing circular defects is established by finite element software, the maximum stress value around the casting defects is extracted, and compared with the average stress value in case ①, the different stress concentration factors corresponding to different distances from the structural surface are obtained. The influence relationship of D / R on the stress concentration factors is obtained through statistical analysis, as shown in Fig. 2.
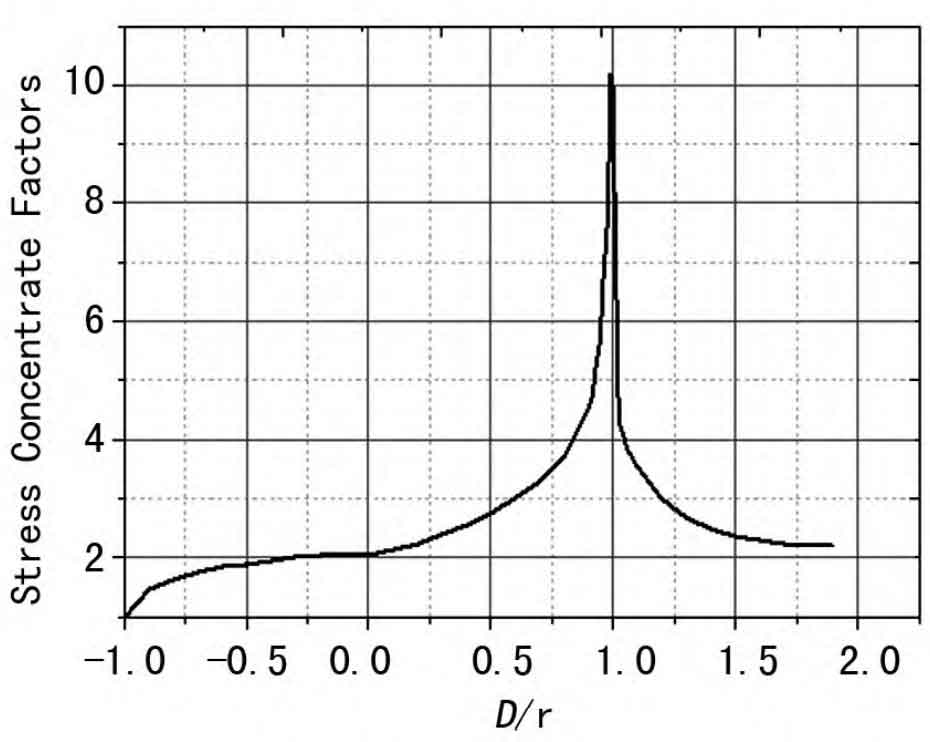
It can be seen from Fig. 2 that with the different positions of casting defects in the structure, the perturbation of stress distribution is different. Within the range of 0.5 < D / R < 1.5 between casting defect and structure surface, the sensitivity of stress distribution is high. And near D / r = 1, the stress intensity factor value is close to infinity. This stress amplitude is the stress surge caused by casting defects and small bearing area on the surface of the structure, which has little impact on the effective mechanical properties of the structure.