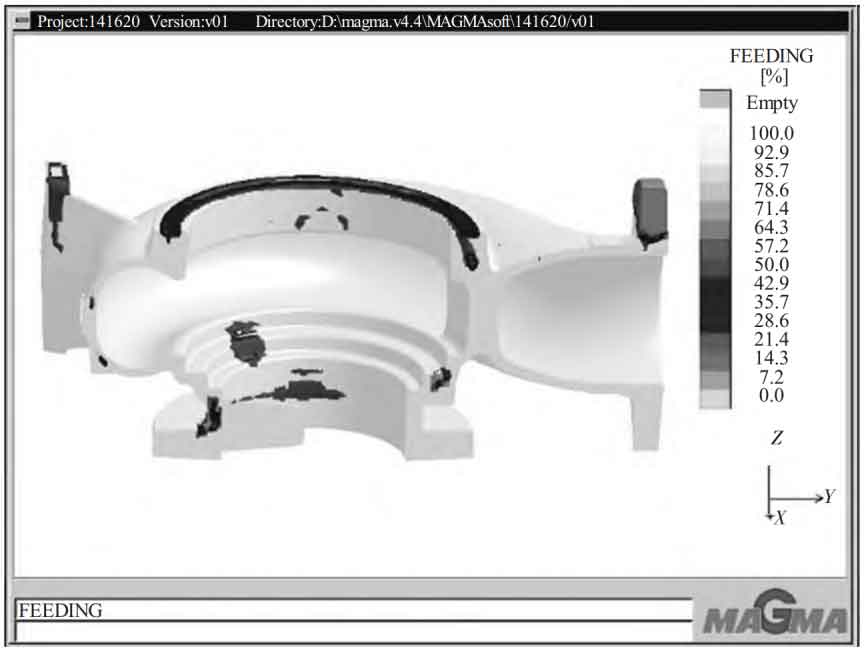
The castings without riser system were introduced into magma, and the pouring posture of the connecting flange at the top and bottom was respectively used for simulation. The starting temperature was 1580 ℃, and the defect prediction results were obtained, as shown in Fig. 1 and Fig. 2.
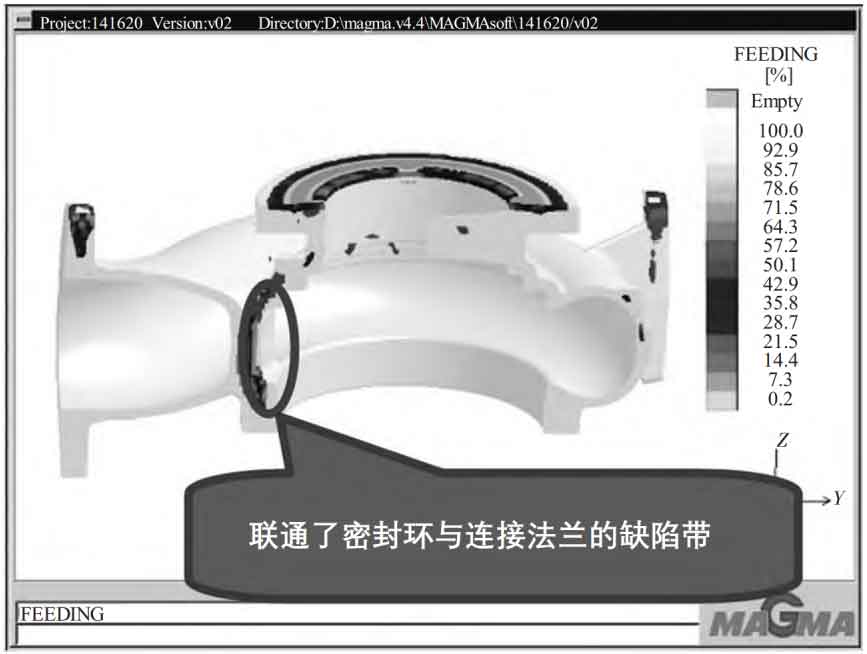
It is now the mainstream process method that the connecting flange faces upward. In this posture, the connecting flange can be fed through the riser. In the outlet junction area shown in Fig. 1, subsidies need to be increased to ensure the feeding effect; Due to the awkward size of the seal ring area, neither self feeding nor effective feeding of the lower inlet flange can be realized. It is necessary to set a large amount of subsidies on the blank surface and then place a riser on it, cooperating with the cold iron on the inlet flange, so as to effectively solve the defects of the seal ring and the inlet flange; The problems of outlet flange and foundation support can be solved through side riser. The final process scheme is shown in Fig. 3.
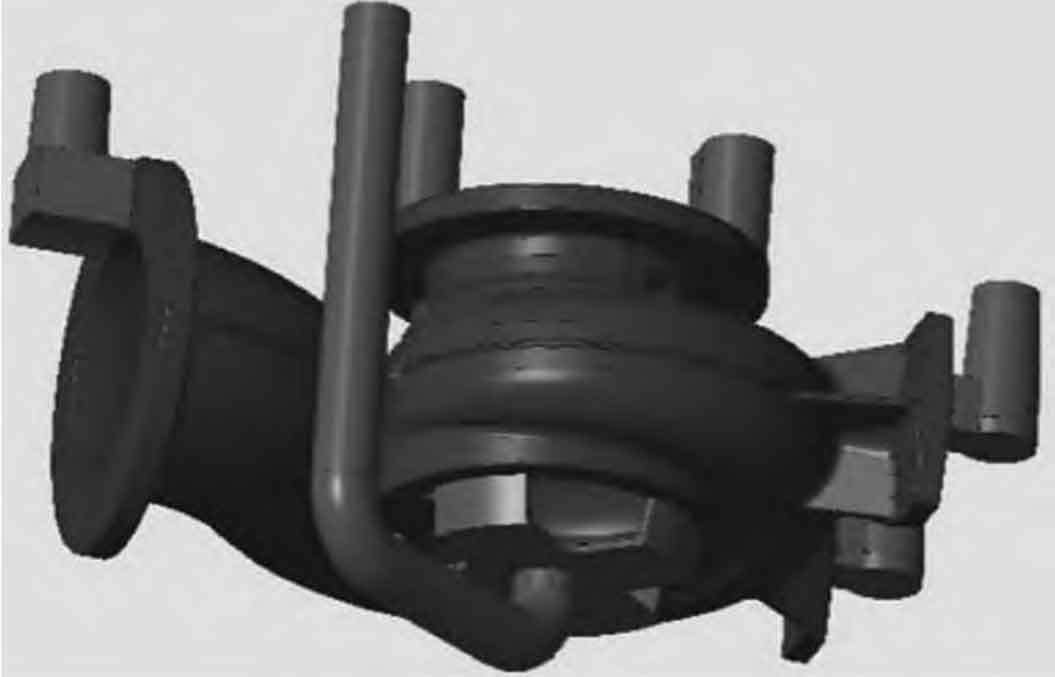
On the other hand, in the scheme with the connecting flange facing down, the size of the inlet flange is relatively large, which can fully feed the sealing ring area; The difficulty is that the sealing ring area can not feed the outlet junction area, resulting in a defective belt connecting the sealing ring and the connecting flange, as shown in Fig. 2. The defective belt is close to the water conservancy area, and it is difficult to apply feeding means. This problem is the root of the mainstream process.
Under the existing process scheme, defects are widely distributed, which requires a large amount of subsidies and feeding at the riser; The scheme with the connecting flange facing down has concentrated defects, but it is difficult to feed; In order to improve the yield of the process, it is necessary to adopt a new scheme and try to solve the defect band in Fig. 2.