In recent years, there have been significant advancements and innovations in the field of casting parts, opening up new possibilities and improving the overall efficiency and quality of the process. Here are some key innovations in casting:
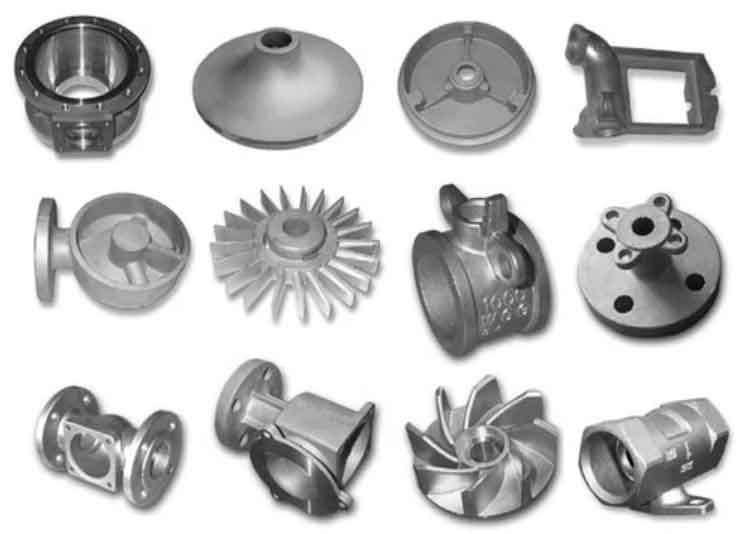
- 3D Printing/Additive Manufacturing: Additive manufacturing, or 3D printing, has revolutionized the casting industry. It allows for the direct production of complex casting patterns and molds, eliminating the need for traditional tooling. This technology enables faster prototyping, reduced lead times, and the ability to create intricate designs that were previously challenging with conventional casting methods.
- Digital Design and Simulation: Advanced digital design and simulation software have greatly enhanced the casting process. Computer-aided design (CAD) and computer-aided engineering (CAE) tools enable precise modeling, analysis, and optimization of casting designs. Casting simulation software predicts and helps mitigate potential defects, optimizing casting parameters and reducing the need for physical prototypes.
- Advanced Materials and Alloys: The development of new materials and alloys has expanded the range of possibilities for casting parts. High-performance alloys with superior strength, corrosion resistance, and heat resistance are now available, making castings suitable for even more demanding applications. Additionally, the use of lightweight materials, such as aluminum and magnesium alloys, has gained popularity in industries seeking to reduce weight and improve fuel efficiency.
- Improved Molding and Core Making: Innovations in molding and core making processes have led to enhanced accuracy and efficiency. Advanced molding materials and binders provide better dimensional stability and improved surface finish. Additionally, the development of environmentally friendly binder systems and sustainable sand additives contributes to a more eco-friendly casting process.
- Automation and Robotics: Automation and robotics have been increasingly integrated into casting operations. Automated pouring systems ensure precise metal pouring, reducing human error and improving consistency. Robotics are employed for tasks such as mold handling, post-casting operations, and quality inspection, enhancing productivity and reducing manual labor.
- Process Monitoring and Control: Real-time process monitoring and control systems enable better control over the casting process. Sensors and data acquisition systems collect information on variables such as temperature, pressure, and vibration, allowing for immediate detection of process deviations and quick adjustments to ensure optimal casting quality.
- Green Casting Technologies: Environmentally friendly casting technologies are gaining attention. Initiatives such as reduced emissions, energy-efficient melting practices, and waste recycling are becoming more prevalent in casting operations. The development of low-emission melting furnaces and sustainable mold materials contributes to greener casting processes.
These innovations and advancements in casting technology continue to push the boundaries of what is possible, offering improved efficiency, precision, and sustainability in the production of casting parts. Manufacturers are embracing these advancements to stay competitive, deliver high-quality parts, and explore new design possibilities.