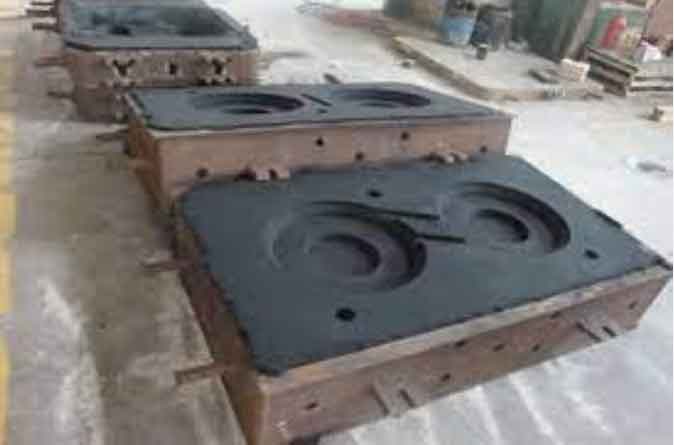
In recent years, there have been several innovations in furan sand casting that have further enhanced its capabilities and expanded its applications in various industries. These advancements have focused on improving process efficiency, material selection, and exploring new applications for this casting technique. Here are some notable innovations and their applications:
- Advanced mold and core materials: Researchers and manufacturers have developed advanced mold and core materials specifically tailored for furan sand casting. These materials exhibit enhanced thermal stability, dimensional accuracy, and reduced gas evolution during casting. They can withstand high temperatures and provide improved surface finish, making them suitable for complex and demanding applications in industries such as automotive, aerospace, and defense.
- Digital design and simulation: The integration of computer-aided design (CAD) and simulation tools has revolutionized the design and optimization of furan sand casting processes. Engineers can create virtual models, simulate the casting process, and analyze factors such as filling patterns, solidification behavior, and heat transfer. This enables them to optimize mold designs, reduce defects, and improve casting quality and performance.
- 3D printing of molds and cores: Additive manufacturing, or 3D printing, has found its way into furan sand casting. It allows the production of complex molds and cores with intricate geometries, undercuts, and internal cooling channels that would be difficult or impossible to achieve using traditional methods. 3D-printed molds and cores offer design flexibility, reduce lead times, and enable rapid prototyping and small-batch production.
- Lightweighting applications: Furan sand casting has gained popularity in industries aiming to reduce weight in their products, such as automotive and aerospace. By utilizing lightweight materials like aluminum or magnesium alloys, furan sand casting can produce complex, lightweight components with high strength-to-weight ratios. This helps improve fuel efficiency, increase payload capacity, and enhance overall performance.
- Hybrid casting processes: Furan sand casting has been integrated with other casting techniques to create hybrid processes that combine the benefits of different methods. For example, combining furan sand casting with investment casting (lost-wax casting) allows for the production of intricate components with fine details and precise dimensions. Such hybrid processes offer increased design freedom and open up possibilities for innovative part geometries.
- High-temperature applications: Furan sand casting has also found applications in industries requiring components with excellent heat resistance. The ability of furan resin binders to withstand high temperatures makes them suitable for casting alloys with high melting points, such as superalloys used in gas turbine engines. The superior thermal stability and dimensional accuracy of furan sand casting contribute to the production of reliable and high-performance parts for extreme operating conditions.
These advancements in furan sand casting have expanded its applications in various industries and facilitated the production of complex, lightweight, and high-performance components. With ongoing research and development, we can expect further innovations that will continue to push the boundaries of design and performance in the field of furan sand casting.