Furan sand casting is a widely used casting process in the foundry industry. It involves the use of furan resin as a binder to create molds and cores for metal casting. While the basic principles of furan sand casting have remained relatively unchanged, there have been several advancements and innovations in recent years that have improved the process and expanded its applications in the industry.
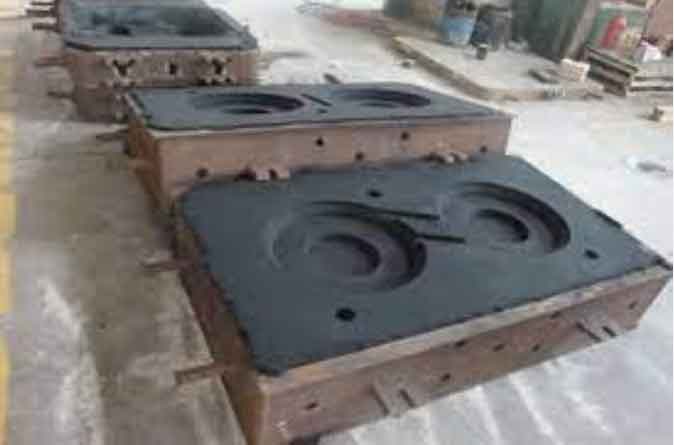
- Improved binders: Traditional furan binders have limitations in terms of strength and shakeout properties. However, advancements have been made in the development of furan binders that offer improved strength, better collapsibility, and reduced emissions during casting. These improved binders result in higher-quality molds and cores, leading to better castings with fewer defects.
- Additives and coatings: Various additives and coatings have been introduced to enhance the properties of furan sand molds and cores. For example, the addition of anti-veining agents helps reduce or eliminate surface defects caused by the penetration of molten metal into the mold. Similarly, coatings can be applied to the sand surface to improve the refractoriness and reduce metal penetration.
- Digital modeling and simulation: The use of computer-aided design (CAD) and simulation software has greatly advanced the capabilities of furan sand casting. Digital modeling allows for the creation and modification of complex mold geometries, facilitating the production of intricate castings. Simulation software enables foundries to predict and optimize casting performance, identify potential defects, and optimize process parameters, thus reducing time and cost associated with trial and error.
- Core-making advancements: Furan sand casting often involves the use of sand cores to create internal features in the castings. Advancements in core-making technologies, such as the use of 3D printing or additive manufacturing techniques, have expanded the design possibilities and reduced the lead time for producing complex cores. This enables the production of highly intricate and lightweight castings that were previously challenging or impossible to achieve.
- Sustainable practices: As environmental concerns grow, the foundry industry is focusing on adopting more sustainable practices. In furan sand casting, efforts have been made to reduce the emissions of harmful volatile organic compounds (VOCs) associated with traditional furan binders. Some companies have developed low-emission or even emission-free furan binders, contributing to a more eco-friendly casting process.
The advancements and innovations in furan sand casting have expanded its applications across various industries, including automotive, aerospace, energy, and more. Furan sand casting is particularly well-suited for producing medium to large-sized castings with complex geometries, such as engine blocks, pump housings, and turbine components. The improved quality, efficiency, and sustainability offered by these advancements make furan sand casting a competitive and reliable choice for metal casting in modern industry.